航空航天领域的制造水平的高低,是一个国家综合制造实力的体现。近些年航空航天领域的高速发展,实现了神舟系列载人飞船的顺利升空,空间站的在轨运行,我国的航天事业取得了令人瞩目的成就。随着航空领域越来越受到关注,航空器的各类结构组成件的加工技术问题也备受重视[1]。
航天异形紧固件作为航空航天器的基础连接件,它的精度高低直接影响着航天器的装配制造精度和整机运行的可靠性[2]。大型关键航天构件由专门精密机床进行加工,但机床核心技术仍受制于国外机床制造公司,对我国存在着一定程度的技术封锁。
相比于重要构件,异形紧固件有体积尺寸较小、应用面广和加工精度要求高的特点,但行业存在着加工设备落后、加工工序分散,加工效率和加工精度低的问题。通过引进国外机床加工技术,不仅引进成本较高,后期运行维护成本也较大,而且无法掌握机床加工核心技术,提升我国的航空航天领域制造业竞争力。
为满足企业紧固件月计划产能4.5万件,解决航天异形紧固件生产的加工难题,针对某型号紧固件特开发出该多工位自动化组合机床,并对机床的控制系统进行设计,将多轴运动控制器运用于机床的加工控制系统。
1、 多工位组合机床的总体设计
1.1 异形紧固件工艺设计
异形紧固件毛坯预制为冷镦加工,内孔预制有ϕ4.6 mm 孔,外圆尺寸精度较高可做为内孔加工的装夹基准。紧固件内孔加工需求为台阶孔、两端锥角、MJ螺纹,紧固件加工成品详细尺寸如图1所示。

图 1 紧固件加工成品尺寸图
紧固件现阶段的生产工艺为:装夹紧固件外圆→车紧固件台阶孔、螺纹底孔和左端锥角→掉头装夹→车右端锥角→装夹于攻丝机上攻螺纹。该加工过程中,紧固件需要多次装夹,在不同机床上完成所有尺寸加工。多次装夹影响紧固件的加工精度,分散加工增加辅助工时,不仅降低生产效率,而且成品的一致性差。
通过对紧固件加工工艺分析优化[3],综合机床结构设计需求,紧固件的生产工艺更改为:自动上料气动夹紧外圆→激光测定台阶厚度内部换算刀具起点→扩孔加工→铰孔加工→倒右端锥角→攻螺纹。
在该工艺中,紧固件通过中空气动卡盘夹紧,只需一次装夹,通过转盘分度,即完成各个工序内容的同时加工,提高加工精度和加工效率,实现紧固件的自动化生产。
1.2 多工位机床的整机结构及动作流程
参考组合机床结构设计[4],结合紧固件的加工工艺,通过相关参数设计计算和选型,确定采用八工位转盘分度,该多工位组合机床的结构示意图如图 2 所示。
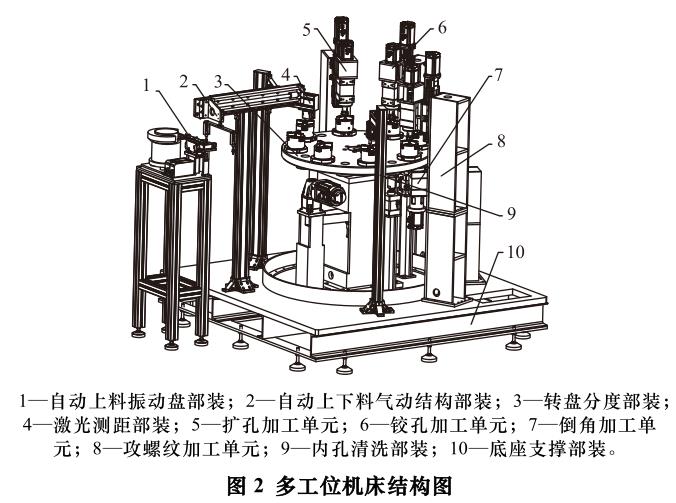
整机加工的工作流程为:振动盘理料滑入气动定位槽→上料气动手指内涨取料→送料气缸平移送料→气动卡盘夹紧工件→转盘分度→定位销伸出定位→激光测距→定位销缩回→转盘分度→转盘定位销伸出定位→扩孔加工→定位销缩回→转盘分度→转盘定位销伸出定位→铰孔加工定位销缩回→转盘分度→转盘定位销伸出定位→倒角加工→定位销缩回→转盘分度→转盘定位销伸出定位→攻螺纹加工→定位销缩回→转盘分度→转盘定位销伸出定位→内孔清洗→定位销缩回→转盘分度→转盘定位销伸出定位→下料气动手指内涨取料→气动卡盘松开工件→送料气缸平移送料→气动手指缩回放料。
2、 多工位机床的控制系统设计
2.1 多工位机床控制系统平台搭建
由多工位机床的机械设计结构,扩孔、铰孔、倒角、攻螺纹单元加工主轴和Z轴进给均采用伺服电机提供动力。转盘在分度过程中要求转速平稳,采用伺服电机配减速机通过带传动确保分度精准。机床伺服轴较多,故选用正运动ZMC406多轴运动控制器为控制核心,通过脉冲控制伺服,抗干扰能力强,可靠性高[5]。运动控制器以 ZDevelop软件作为PC端程序的开发调试。程序以ZBasic为编程语言,连接到运动控制器通过对伺服驱动器的信号输入实现对各个伺服电机轴的控制。该多工位机床的整机控制方案如图3所示。
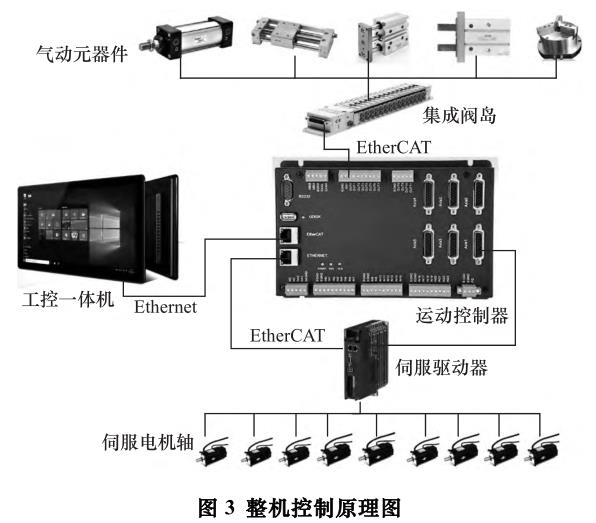
通过二位五通电磁阀控制气体的通断,实现紧固件的上下料、夹紧,以及分度转盘的定位和加工过程中的吹气。测距工位的激光位移传感器测定紧固件台阶厚度,程序自动处理得出刀具加工起点位置。两个霍尔传感器,用于感应分度转盘在启动后是否处于零位,以及分度是否到位配合定位销使用。
上位机用 C#语言,在 Microsoft Studio 环境内进行上位机程序的编写和调试。为方便操作人员对机床操作和参数设置,触摸屏采用工控一体机,配备 Windows 操作系统,具有快速响应和大量加工数据储存能力[6−7]。工控一体机触摸屏和运动控制器通过 Ethernet 百兆网口进行通讯。Ethernet 通讯接口和 EthereCAT 通讯接口均采用标准以太网RJ45。
2.2 控制系统整体方案设计
结合多工位机床结构和总体控制系统平台,要实现紧固件的加工,控制系统需控制机械结构完成的具体动作:(1)能够控制与机械主轴相联结的伺服电机的转速和转动方向,达到紧固件内孔的光洁度要求。(2)能够对直线模组配备的伺服电机的转速控制,并能控制 Z 轴上升下降的具体停靠位置。(3)能够控制多工位分度转盘每次均匀分度,并在分度完成后控制定位销升降实现定位。(4)能够控制自动上下料机械夹爪,在上料工位无待加工件时上料,下料工位有加工完成件时取料。(5)能够控制激光测距传感器,在有待加工件时将刀具加工零位数据传输至后台系统,进行加工换算。(6)能够监测每个工位的加工状态,停机再生产启动后可完成后续加工。(7)可对刀具使用寿命进行检测,达到预设加工次数后设备报警提示,进行刀具更换。(8)可实现对切削加工过程中的冷却润滑与吹气的通断控制等[8]。多工位组合机床的控制系统方案原理如图 4 所示。
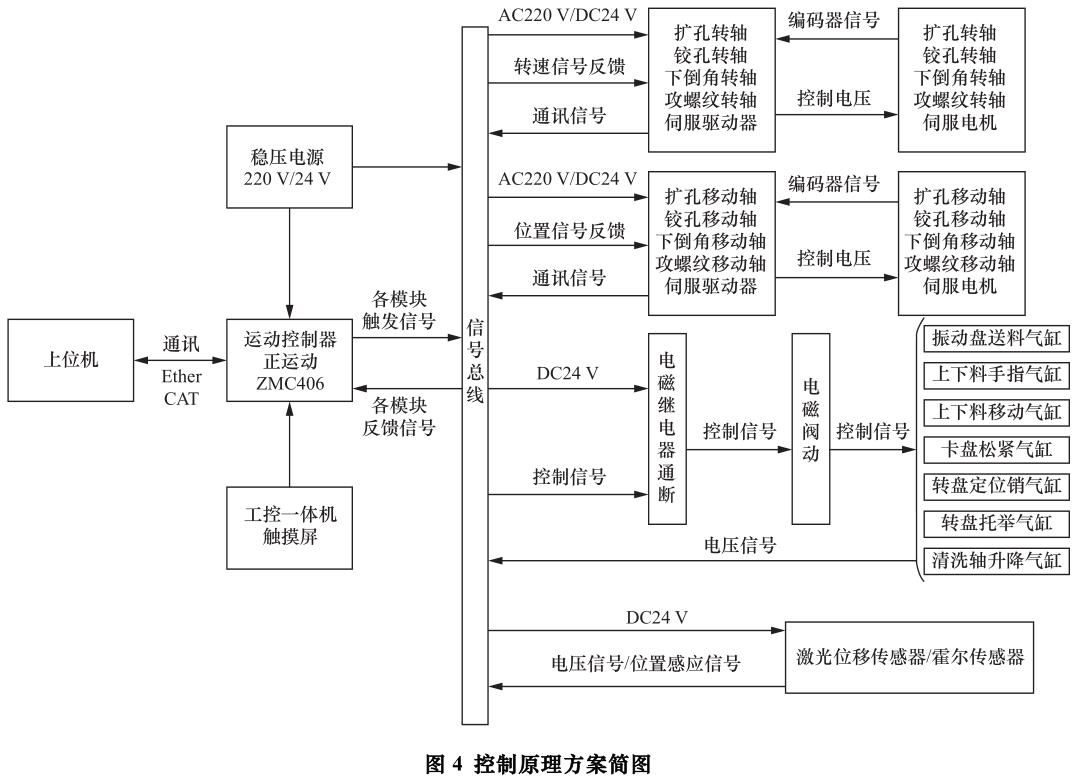
2.3 控制系统软件设计
根据紧固件加工机床的功能要求,对实现该加工功能进行模块划分。根据控制流程和加工工艺将控制系统划分为加工前处理模块、加工模块和加工过程中处理模块,方便程序的模块化设计以及后续对各个模块进行衔接[9]。系统的模块框架如图 5 所示。
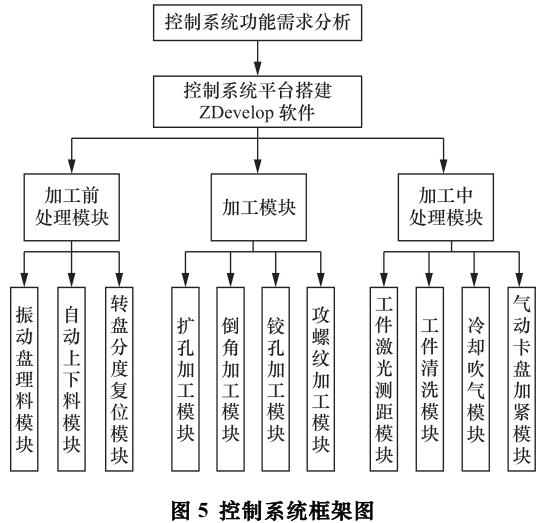
通过对控制系统模块化设计,在三大模块的基础上进行了细分出各个具体功能模块[10]。每个小功能模块下可再细分为自动/手动两种操作模式,分别进行程序设计,方便对各个模块单独调用和调整,提高编程的效率。
多工位机床的触摸屏采用工业控制一体机,具有高速处理数据的优势。利用 C#语言进行控制界面的编写,通过人机界面交互操作,实现对机床的方便直观操作[11]。机床触摸屏参数设置界面如图6所示。在操作界面,可进行手动和自动界面的切换。
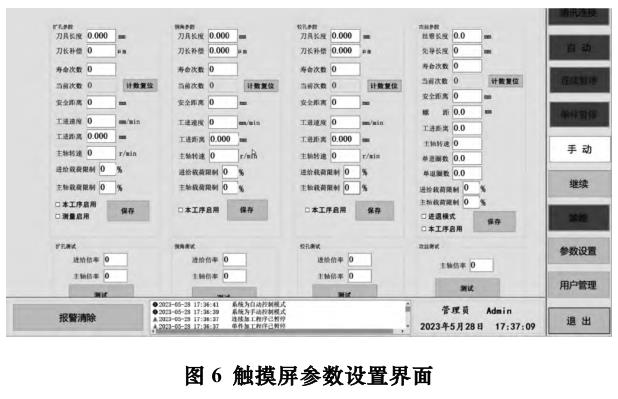
自动化界面可实时显示加工主轴转速和Z轴移动位移。切换至手动界面时,可进行加工速度、加工刀具参数的设定,并可对各个部件实现手动操作。在触摸屏界面最下方有机床工作日志,方便对机床的加工状态进行定期统计分析。
3、 多工位机床系统调校及试加工
3.1 整机系统调校
组合机床的调校,包括机械结构相对位置的校正和控制程序的调试。机床上电后,通过 Ethernet接口连接至PC端 ZDevelop软件,将编制程序通过PC端连接至运动控制器,下载到运动控制器[12]。
设计的机床按照控制程序模块进行分步动作调试。
机床单步动作调校完成后,可利用紧固件样品对机械动作进行验证。调校时出现加工主轴与紧固件定位卡盘不同心,通过利用加工主轴自加工方式,对气动卡盘软爪进行加工,保证两者同心。对分度转盘控制调校时,转盘外径和转动惯量较大,会出现分度位置过冲的情况,为解决该问题,在转盘下方增加霍尔开关。当伺服电机带动转盘按照程序预设度数分度到位时,开关触发,转盘定位销伸出,确保转盘分度位置准确,解决方案如图 7所示。图中一个开关为机床上电后转盘复位感应开关,另一个为加工过程中防止转盘过冲感应开关。
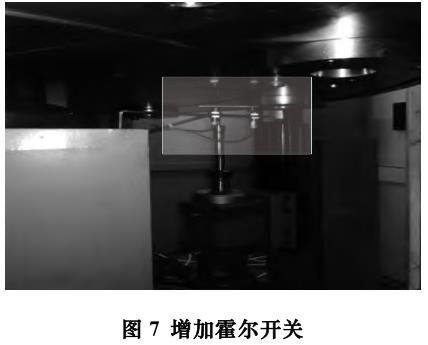
3.2 试加工及分析
企业现有加工模式对紧固件加工的实际情况见表1。企业现阶段加工精度和效率都较低,无法满足企业月计划产能需求。
按照程序模块对机床动作调试完成后,整机联动进行自动程序的空运行。空运行一段时间,无任何故障后,进行小批量紧固件的试加工。对试加工紧固件结果进行统计分析,结果见表2。利用研发组合机床加工紧固件,提高零件的加工精度和加工效率,成品紧固件的尺寸一致性较好,满足企业月计划4万件的加工需求。该多工位组合机床的实物如图8所示。经该多工位机床试加工出的异形紧固螺母部分成品如图9所示。
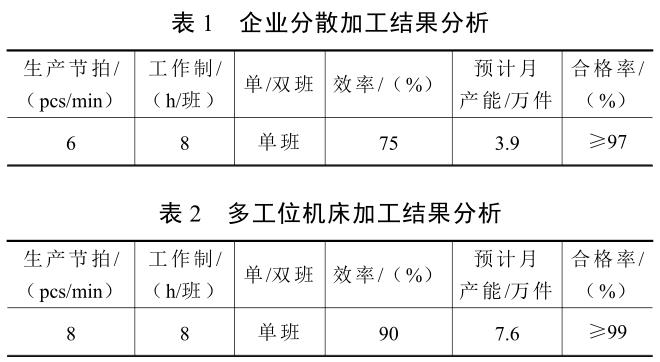

对比两种生产模式下紧固件的加工结果,研制该组合机床达到预期设计目标,提高了紧固件加工技术水平。
4 、结语
针对异形航天紧固件内孔加工工序分散、加工效率和精度低的问题,研发出多工位自动化机床。
机床采用“工控 PC机+运动控制器”的模式,设计机床控制系统,配合机械结构完成特定型号异形紧固件内孔尺寸的精加工。
(1)该机床可实现自动上下料,通过一次装夹完成内孔尺寸加工,提高加工的精度和效率。
(2)所有加工工序集中于一台加工设备,避免了紧固件加工过程中的多次周转和装夹,缩短辅助加工时间。
(3)经实际加工验证,研发机床加工紧固件成品生产节拍较快,产品合格率高,产品一致性较好。
(4)设计开发控制程序满足紧固件自动化加工精度要求,运行可靠、稳定。
(5)该机床当前只针对特定异形紧固件进行加工,但紧固件型号和结构较多,需考虑通过模块化设计,通过快换定位夹具和刀具,满足不同型号的加工。
参 考 文 献
[1]李一帆. 航空航天制造技术及设备现状与趋势 [C]. 全国第三届“智能电网”会议论文集,2019:69-71.
[2]王肇宇. 国际航空航天紧固件发展现状及趋势研究 [J]. 宇航总体技术,2018,2(4):1-7,30.
[3]李益民. 机械制造工艺设计简明手册 [M]. 北京:机械工业出版社,1997.
[4]大连组合机床研究所. 组合机床设计(第一册)机械部分 [M]. 北京:机械工业出版社,1975.
[5]吴宏,蒋仕龙,龚小云,等. 运动控制器的现状与发展 [J]. 制造技术与机床,2004(1):24-27.
[6]袁国锋,王效岗,刘建龙,等. 双枪纵缝数控焊接机床控制系统设计 [J].组合机床与自动化加工技术,2016(4):121-123,131.
[7]李梁,滕峻林,肖铁忠,等. 摩托车曲轴箱孔系钻铰复合加工工艺 [J].组合机床与自动化加工技术,2018(1):106-108.
[8]王丽珍. 双面钻孔组合机床控制系统设计 [J]. 机械工程与自动化,2017,12(6):180-181,184.
[9]熊幸明,王新辉. 基于 PLC 的二工位组合机床控制系统设计 [J]. 组合机床与自动化加工技术,2004(6):38-42.
[10]李益东,严思杰,廖黎波,等. 一种多工位复合自动钻床的设计 [J].机电工程,2012,29(12):1419-1422.
[11]陆波,盛强. 基于 PLC 的绝热层打磨机控制系统设计 [J]. 制造技术与机床,2020(3):32-34.
[12]李春木,章明众,郑新武,等. Ether CAT 总线在伺服运动控制系统中的应用 [J]. 机电工程,2011,28(11):1336-1338.
第一作者/通信作者:李雪晓,女,1973 出生,高级工程师,主要从事数控机床设计与制造等技术方面的工作,安阳鑫盛机床股份有限公司研发中心副主任,河南省学术技术带头人。E-mail:ayxslxx@163.com
无相关信息