1、序言
钛合金具有比强度高、抗蚀性强和耐高温等优良性能,被广泛应用于航空、航天、军工及生物医疗等领域。随着工业的发展,传统行业和一些新兴行业对钛产品需求不断增加,进而引起钛产品的毛坯(钛锭)需求量陡增。同时,对钛锭的质量要求也越来越高,但钛锭车削加工困难,给实际生产带来一些问题,严重妨碍生产效率和成材率的提高。
因此,根据钛锭加工特点研究最佳的刀具参数和切削用量尤为重要。
2、钛合金切削加工特点
(1)变形系数小钛合金切削变形系数ε≈1,而普通碳钢的变形系数ε≈3,在切削过程中,切屑在刀具前刀面接触时间很短,导致切削力在切削刃附近过于集中,因而加快了磨损。
(2)切削温度高钛合金的导热系数低(约为钢的1/5),造成切削过程产生的大量热量集中在刀具与工件挤压的区域,高温会加速硬质合金中黏结剂Co的扩散,从而使刀具硬度下降,磨损加剧。
(3)冷硬现象严重因为钛在高温下化学性质活泼,很容易吸收空气中的氧和氮形成硬而脆的外皮,同时切削过程中的塑性变形也会造成表面硬化,加剧刀具磨损。
(4)刀具磨损严重由于钛合金的弹性模量小,约为钢的1/2,所以使得钛合金在切削时加工表面的回弹量很大,后刀面与已加工表面的摩擦剧烈,加剧了刀具磨损。
从上述钛合金加工特点来看,钛合金在切削过程中需要考虑的条件复杂,其材料是一种非常难加工的材料,其加工也是近年来切削加工领域的热门课题。
3、钛锭生产现状及切削存在问题
(1)钛锭生产工序目前,国内主要采用真空自耗电弧炉(VAR)熔炼钛锭。对于普通的钛锭熔炼,一般都要采用2~3次的熔炼才能完成。下面以生产直径为720mm的TC4合金锭为例,其生产流程如图1所示。
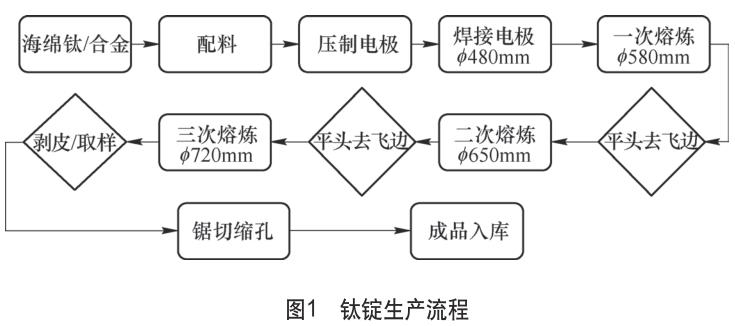
流程图中φ580mm和φ650mm这两种规格的钛锭只平头不剥皮,目的是去除飞边、锭冠,为熔炼做准备,在φ720mm成品钛锭的头、中、尾取屑样和块样。
(2)钛锭切削存在的问题钛锭切削过程(见图2)主要存在以下问题:①导热性差,刀具磨损严重,切削效率低。钛的导热性很差,切削时大量的热集中在刀头上,刀头容易磨损。同时,切削过程钛锭表面冷隔、鼓包、氧化皮、皮下气孔和组织不均等缺陷及机床的径向振动,对刀头冲击力大,磨损严重。在切削过程要不断更换、磨刀和调整夹持,再加之钛合金本身难加工,切削速度低。因此,机床一般选刚性好、功率大、间隙小、径向圆跳动小的重型机床。通常在钛锭生产周期中,平头和剥皮加工就占了1/3以上的时间,如生产一只牌号为TC4的铸锭,机械加工时间约40h,加工TC18、TC21等高强度钛锭,则需要更长的加工工时。因此,钛锭机械加工耗时长,严重制约着生产效率的提高。②切屑形态不佳。钛锭切削是以去除余量为目的的粗加工,切削刀具刃倾角一般为λS≤0°。在切削钛合金锭时由于变形系数小,容易挤裂切屑,微观形态表现为锯齿状形态(见图2d)。在切削纯钛锭时,容易出现带状切屑,体积不易控制,容易缠绕在工件或刀头上,加速刀具的磨损,且存在一定的安全隐患。钛锭产生的切屑给搬运、存储也带来一定困难。③硬质合金刀具带来钨污染风险。目前钛合金切削使用最普遍的仍是钨钴类硬质合金刀具,如YG8。此类刀具中含有85%~95%的碳化钨和5%~14%的钴,钴作为黏结剂金属,其熔点是3410℃,一旦引入半成品锭中,在熔炼时是不被熔化的(因熔池温度只有2000℃左右),后期的加工也无法消除。钛合金广泛应用于飞机的重要承力构件,由钨污染造成的质量缺陷,有可能导致灾难性的事故。因此,钛及钛合金在机械加工过程中,杜绝钨污染成为评判钛合金质量的一个重要指标。
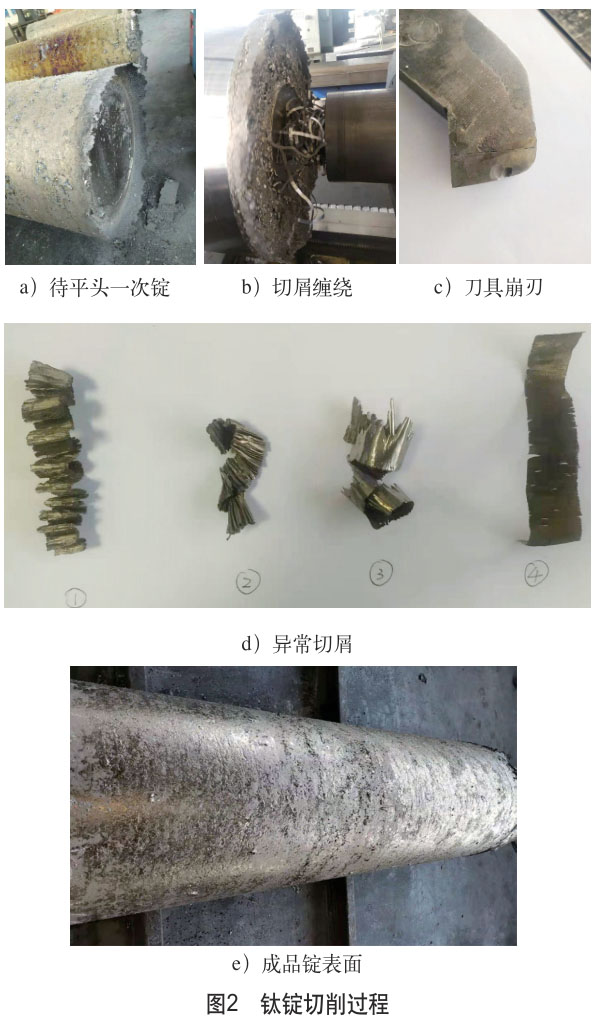
钛锭切削过程引入钨污染有两方面原因:一是切削刃崩裂嵌入钛锭表面;二是刀具切削过程刀具的磨损扩散到铸锭表面。在平头工序中,因锭冠的厚薄不一,凹凸不平(见图2a),切削时造成的间歇性交变冲击力,更容易发生以上两种情况。因此,对刀具参数和切削用量选择要谨慎对待。④冷硬现象比较严重。钛在高温下性质活泼,在较高的切削热作用下,很容易与空气中的氧、氮、氢反应,生成其化合物,致使表面硬化、脆化,甚至粘结在刀头上,造成粘结磨损,加剧刀具的磨损、崩裂,同时,给准确取样和回收钛屑带来困难。⑤尽量不用切削液。半成品钛锭平头时如使用切削液有可能污染钛锭,造成重熔后引入新杂质。成品锭切削时使用切削液对回收钛屑又造成一定困难,因此,通常情况下,切削钛锭不使用切削液。这给本身就难加工的钛合金带来更大的困难。近年,也有学者研究干式切削加工、可降解型切削液加工、低温干式切削加工、低温冷风切削加工和低温冷风微量润滑加工等绿色加工技术。
4、对策分析
正确选择刀具参数及切削用量是防止刀具崩刃,提高刀具寿命和切削效率,降低生产成本最为直接有效的办法。
4.1刀具材质和主偏角选择
常用刀具分为四大类,即工具钢刀具、硬质合金刀具、陶瓷刀具和超硬刀具。铸锭剥皮车削是以去除表面氧化皮和裂纹等缺陷为目的的粗车,由于铸锭表面及皮下组织的复杂性,刀具需具有一定的抗冲击性和耐磨性,行业内长期实践的结果还是选择硬质合金刀具(如YG8)最为经济和实用。
刀具主偏角在相同进给量和背吃刀量下车削,减少主偏角可使切屑变薄,切削刃参加切削的长度增加,切削刃的散热面积增大,更利于散热。从切削受力分析看,主偏角减小时,径向力增大,轴向力减小;主偏角增大时,径向力减小,轴向力增大,也就是主偏角可以调整径向力和轴向力。
在钛锭切削时,既需要一定的切削深度(径向力),又要延长刀具的寿命,因此选择主偏角为45°的整体式焊接车刀。这样,既能满足单刀进行平头加工,也能进行外圆剥皮加工。减少换刀次数和刀具数量,提高效率,降低成本。
4.2刀具参数选择
(1)刀尖刀尖是刀具最薄弱的部位,切削环境也最为恶劣。此处散热条件不好,刀尖处积累的切削热很容易使刀具磨损。合适的刀尖半径不仅可以大大降低崩刃几率,还可以延长刀具耐磨度。在通常的机械加工手册中刀尖半径推荐为0.2~2.4mm。但是在钛锭剥皮中,应选择尽可能大的刀尖半径以获得最高的强度。增大刀尖半径,既增加了刀尖强度,又可以使用大进给提高切削效率。然而并非刀尖半径越大越好,因为随着刀尖半径的增大,径向分力也增大,振动也会加大,因此根据钛锭剥皮的特点和YG8刀具的强度,切削钛合金选择R2.0mm刀尖,切削纯钛选择R3.0mm刀尖。
(2)前角角度切削刃的锋利性和坚固性由前角的大小决定。理论上,正前角可以阻止切屑弹性变形、塑性变形,降低切屑排出时与前刀面的摩擦阻力,有利于散热和切削。但是,增大前角会使楔角减小,又会使切削刃强度降低、热量过于集中,容易造成崩刃,刀具耐磨度也下降,刀具前角受力情况如图3所示。
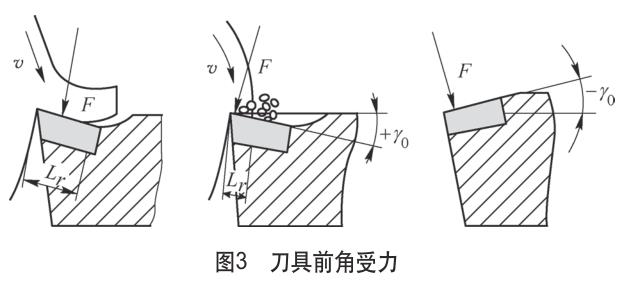
钛锭切削刀具前角一般较小,通常为-10°~0°,一般情况下多采用0°前角。这样既保证了刀具的强度,又使刀具有一定的锋利度。
(3)后角角度后角是配合前角调整切削刃的锋利程度和强度的角,它的主要作用是减小切削过程中加工表面与刀具后刀面之间的摩擦力,因而它对刀具寿命和加工表面质量有很大的影响,刀具后角与接触层长度的关系如图4所示。
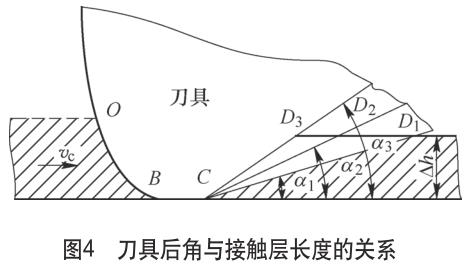
因钛合金弹性模量小,在切削时加工表面的回弹很明显,由图3可知要延长刀具寿命必须增大后角角度才能减少与回弹面的摩擦。但是增大后角角度,使楔角减小,反而降低刀具的强度,导致刀具过快磨损甚至崩刃。综合考虑,一般情况下,钛合金的车削加工后角的选择为10°~16°。
(4)前刀面形状选择刃区剖面形式如图5所示。锋刃型半径很小,切削刃很锋利(见图5a),但是锋刃的抗冲击性能差,即使切削过程遇见小突起,都极有可能导致崩刃。钝圆型切削刃(见图5c),不但在提高切削刃强度方面获得与负倒棱型(见图5b)同样的效果,而且比负倒棱型更有利于消除刃区微小裂纹。同时,在切削过程中对已加工表面还有一定的熨压和消振作用,不但有利于提高已加工表面质量,还提高了刀具的寿命。因此,钛锭切削应选用倒棱型和钝圆型这两种前刀面形状。
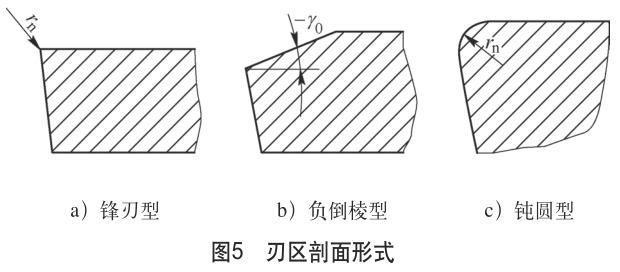
(5)刃倾角刃倾角是主切削刃与基面之间的夹角,其作用是控制切屑排出的方向。当刀尖为主切削刃上最高点时,则λS>0°;当刀尖为主切削刃上最低点时,则λS<0°;当主切削刃与基面平行时,则λS=0°。多数情况下车刀具都是取λS=0°,刃倾角与切削刃受冲击位置的关系如图6所示。
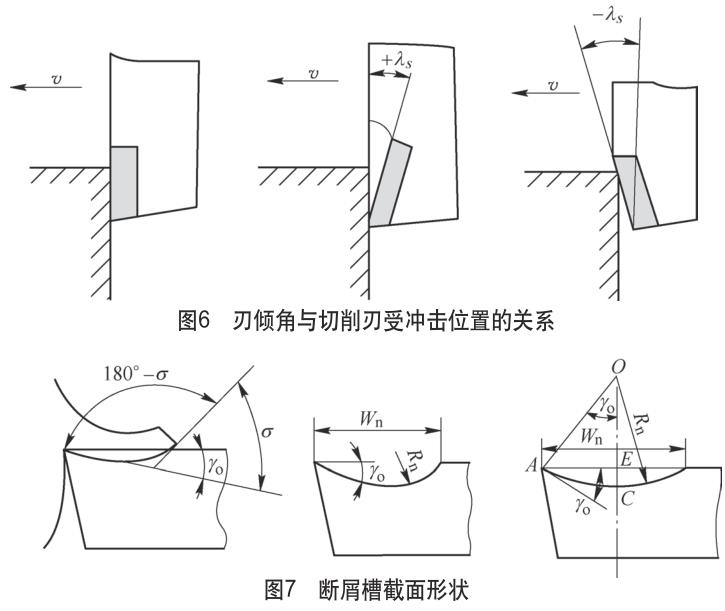
刃倾角的选择原则:①精加工时刃倾角一般取正值,粗加工时刃倾角取负值。②断续切削时刃倾角应取负值。③工艺系统刚性好时,刃倾角可加大负值。
钛锭切削为粗加工,且切削时存在间歇性交变冲击力,应该选用负刃倾角,但是大到一定角度后,径向切削力增大,冲击力变大,散热条件变差,综合考虑刃倾角一般在-10°~5°之间选择。
(6)断屑槽断屑槽可以有效控制切屑形状、体积和排出方向,降低了切削抗力,延长刀具寿命,同时也减小了劳动强度,降低了安全风险。断屑槽的形状及尺寸,需结合切屑性质、刀具参数及切削用量选择,断屑槽截面形状如图7所示。
4.3切削用量选择
(1)切削深度切削深度由工艺加工余量决定,但也需根据铸锭实际氧化皮厚度、皮下缺陷深度灵活调整,一般情况单边去除量8~12mm。切削时尽可能采用大切削深度,使刀尖深埋于硬皮和冷硬层以下,这样避免切削刃过早磨损和崩裂。当然,切削过程还要考虑成材率,不能扎入太深降低成材率。
(2)进给量进给量对铸锭表面粗造度影响最大,其次是切削深度和切削速度。钛锭剥皮主要目的是为去除铸锭表面氧化皮和内部缺陷,对成品铸锭表面粗造度值要求不高,通常Ra为12.7~25μm。因此,在工艺、设备系统所能承受的范围内采用最大进给量。因强度原因,加工合金锭进给量选0.8mm/r,加工纯钛锭进给量选1.4mm/r。
(3)切削深度、进给量和切削速度的匹配钛合金切削容易产生锯齿形切屑,导致切削力高频率周期波动,进而使单位切削力增大,切削温度升高刀具磨损严重,采用低速、大进给量、大切削深度的方法,可以降低锯齿形切屑产生的频率。
5、实例验证
在机加车间,将青岛铭泰机床厂的CG84125-4500重型轧辊车床作为试验机,使用YG8硬质合金的整体式焊接车刀,用如下刀具参数(见表1)和切削参数(见表2),分别对规格为φ720mm×1650mm,质量为3t的纯钛锭(TA1)和钛合金锭(TC4)外圆进行车削剥皮。
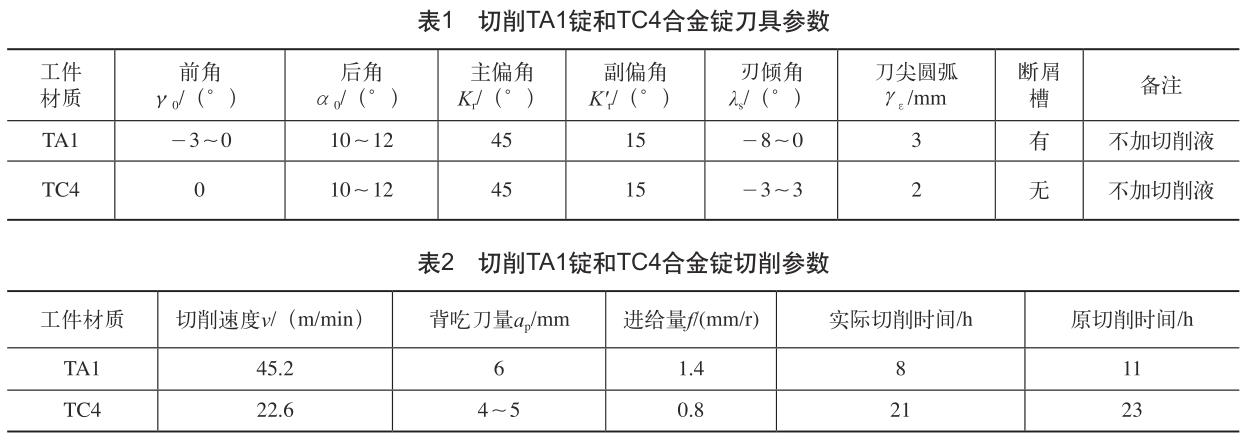
因合金强度高,切削难度大,为了保护刀具强度,所以没有开切削槽。从切削效率、换刀次数、切屑形貌与未改进前进行对比,纯钛切削时间均缩短了3h,钛合金切削时间缩小了2h;合金原来车削200mm就得换刀,此试验中车削300~500mm换刀一次,而且锯齿状切屑从原来的30%下降到了10%。实例结果表明,改进后的刀具参数和切削用量,使切削效率大幅提升,同时刀具磨损降低,切屑形状也得到了有效控制。
6、结束语
通过分析钛合金加工的特点,指出了实际生产中钛锭切削过程中存在的问题,对刀具参数和切削用量进行探讨分析,并用实例验证了钛锭切削所选刀具参数和切削用量的可行性,对钛锭高效率、低成本生产有一定的指导意义。
参考文献:
[1]贾翃,逯福生,郝斌.2019年中国钛工业发展报告[J].钛工业进展,2020,37(3):33-39.
[2]齐德新,马光锋,张桂木.钛合金切削加工性综述[J].煤矿机械,2002(11):3-4.
[3]张春江.钛合金切削加工技术[M].西安:西北工业大学出版社,1986.
[4]周连贵.钛合金的切削加工[J].飞航导弹,1986(7):60-64.
[5]列兹尼科夫.高强度钢高温合金和钛合金的切削加工[M].北京:机械工业出版社,1980.
[6]刘东.TC4钛合金切削中切屑塑性变形分析[J].宇航材料工艺,2017,47(4):71-74.
[7]石磊.钛合金切削加工中刀具与工件性能匹配的研究[D].济南:山东大学,2007.
[8]赵欢欢,等.低温冷风微量润滑加工技术的研究状况[D].上海:上海理工大学,2006.
[9]张震,何曙华.低温冷风切削技术浅谈[J].工具技术,2002(6):32-33.
无相关信息