1 、前言
铌铪合金是一种低强度高塑性并且有良好焊接性能的合金,1965 年,美国研制成功 Nb-10Hf-1Ti 合金,并于 1969年用于阿波罗载人登月舱液体火箭发动机辐射冷却喷管延伸
段,1975 年,中国也研制成功 Nb-10HfTi1Zr0.7 铌合金。试验证明,我国研制的铌铪合金的主要性能指标已经达到国外同类合金的水平。目前能生产直径 220mm,高 900mm 的铸锭 ;同时也能生产直径 110mm,长 1200mm~1500mm 的挤压棒以及各种规格的板材。
由于铌铪合金材料具有特有的高熔点,低强度、高塑性并且有良好焊接性能的特点,其广泛应用于电子、冶金、钢铁、石油、化工、汽车、通讯、建筑、交通、核能、航空应用
及航天航空等领域[1]。
另外,铌铪合金是航天工程和技术中应用量最多的一种铌合金,对金属铌来说,它在难熔金属中具有的出色综合性能,如熔点高达 2448℃,比重为 8.57 克 / 立方厘米,在1093℃ ~1427℃范围比强度最高,温度低至 -200℃仍有良好的塑性和良好的加工性能,而铌铪合金是以铌为基加入一定量铪和其他元素形成的铌合金 , 在二元相图上,铌和β-Hf 形成置换固溶体,铪是一种活性元素,与铌中的氧和碳化合生成 HfO2 和 HfC 化合物,起弥散强化作用,同时降低间隙元素的有害影响,改善铌合金焊接性能和涂层性能 ,从而使它成为在宇航方面优先选用的热防护材料和结构材料。但是,它的高温抗氧化性能不好,在 450℃以上必须氧化保护涂层。具体应用场所 :
(1)液体火箭发动机辐射冷却喷管延伸段,此种结构简单、可靠、适用于承受长时间工作和多次起动,所以多用于顶级发动机和宇宙飞行器发动机。如 ;大力神Ⅲ C 的过渡级发动机喷管延伸段采用辐射冷却 ;阿波罗载人登月飞船服务舱发动机辐射冷却喷管延伸段 ;阿波罗登月舱下降发动机辐射冷却喷管延伸段等等 ;
(2)双元液体推进剂姿控发动机 ;R-4D 反作用控制发动机是用铌铪合金棒材机加工制成燃烧室 ;阿金纳火箭其推力室的燃烧室也是用铌铪合金机加工制成 ;
(3)可伸出喷管民兵Ⅲ第三级可伸出喷管延伸段方案采用铌铪合金制成,长度约 406 毫米,用 4 个气动作动器在点火几秒后展开,喷管面积从 24 加大到 43,提高了推力效率,为提高导弹射程或有效载荷提供了可能。
但是,确保产品正常顺利工作和使用的首要条件是产品必须无任何质量问题,特别是上面所说的应用于航天方面的火箭发动机更是不能有一丝一毫的问题,如果当产品存在潜在的各种缺陷如裂纹等,不仅无法保证产品的正常使用,对航天类产品而言,还将由于此问题将造成设备或装备的致命的损伤,从而导致无法正常工作,其后果是非常严重的。因此非常有必要明确缺陷的产生原因并提出相应的检测方法。
在这里,我们仅针对棒材在机加工后出现的肉眼可见裂纹缺陷产生原因进行分析,并提出相应的预防和解决办法。
2、 实验
2.1 实验用材料来源及缺陷分类
2.1.1 材料生产过程及来源
将铌、铪、钛三种合金按一定比例配料,用氩弧焊方法制成电极,在真空自耗电弧炉上经两次熔炼制取铸锭,然后将铸锭包钢套在挤压机上开坯,再锻成棒材,经机加至规定尺寸。
此次收集的棒材为在机加工生产工序中发现存在裂纹缺陷的废品。
2.1.2 缺陷分类
依据发现裂纹缺陷的部位,分为棒材外表面及侧面存在长度及深度不等的裂纹、内部裂纹及表面较浅的小缺陷三类缺陷作为分析对象。具体为 :图 1-5 为外表面及侧面存在长
度及深度不等的裂纹、图 6-7 内部裂纹及图 8 为表面较浅的裂纹小缺陷。
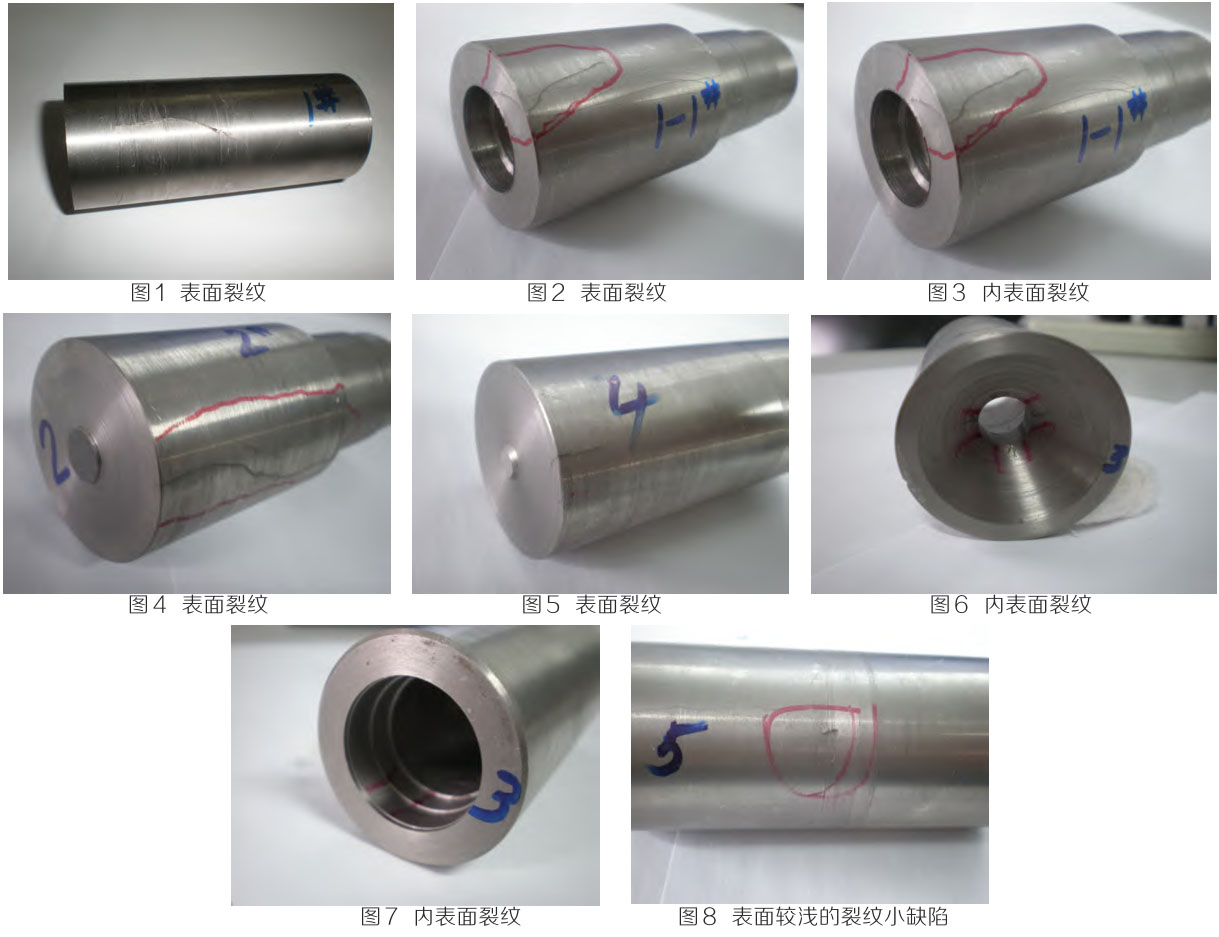
2.2 实验用检测设备原理及型号
2.2.1 超声波探伤仪
(1)超声波检测原理。超声波检测是应用最广泛的无损检测方法之一,超声波检测方法利用进入被检测材料的超声波对材料表面与内部缺陷进行检测。利用超声波对材料的宏观缺陷进行探测,依据的是超声波在材料中传播时的一些特性,如 :声波在通过材料时能量会有损失,在遇到两种介质的分界面时,会发生反射等等,常用频率为 0.5—25MHz。
通常以来自材料内部各种不连续的反射信号的存在及其幅度、入射信号与接收信号之间的声传播时间、声波通过材料以后能量的衰减的进行发现缺陷并对缺陷进行评估的基本信息。超声波检测的适用范围非常广,可用于各种金属材料和非金属材料,从检测形状上来说,可以是板材、棒材、管材、锻件等 ;从缺陷的特点来说,既可以是表面缺陷,也可以是内部缺陷[2]。
(2)超声波检测设备型号。检测时选用武汉中科创新技术股份有限公司生产的汉威 HS610e 型 A 扫描超声波探伤仪器,该仪器具有检测灵敏度高、可对缺陷精确定位、操作方便和选用范围广的特点。
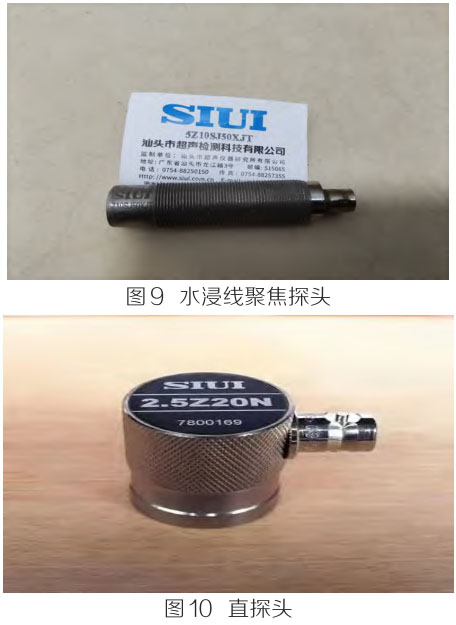
(3)超声波检测设备选配探头。检测时选用广东汕头超声电子股份有限公司生产的 5Z10SJ50XJT 水浸线聚焦探头( 图 9) 以及 2.5Z20N直探头 ( 图 10)。为保证检测过程中,水浸聚焦探头始终以固定角度入射到工件上,对探头采用马鞍架固定,并且马鞍架与工件接触部位,马鞍架采用线切割的方法,加工成与工件曲率相同的外形,保证了检测的稳定性与准确性,再辅以直探头,对直径方向上的内部缺陷进行检测。
(4)超声波检测对比试块选择。采用与工件相同材质的,相同规格的纵向人工刻槽缺陷以及带曲率的平底孔试块。纵向人工刻槽缺陷参数为 3mm×0.1mm×0.05mm(长× 宽 × 深);平底孔试块人工缺陷埋深一般用壁厚的 3/4 作为基础。
(5)超声波检测灵敏度选择。通过前期对检测设备及探头角度的调试和确定,最终检测时所用的基础灵敏度为61.4dB。为了便于发现缺陷,一般在检测时,在基础灵敏度的数值上增加 6dB 作为检测灵敏度,当发现缺陷时,恢复至基础灵敏度作为当量的判定,得出该缺陷的当量值大小。
2.2.2 X 射线探伤机
(1)X射线检测原理。X射线检测技术是一种重要的无损检测技术,它依据的是被检工件由于成分、密度、厚度等的不同,对射线产生不同的吸收或散射的特性和对被检工件的质量、尺寸、特性等作出判定[3]。当强度均匀的射线束透照射物体时,如果物体局部区域存在缺陷或结构存在异常,它将改变物体对射线的衰减,使得不同部位透射射线强度不同,这样,采用一定的检测器(例如,射线照相中采用胶片)检测透射射线强度,就可以判断物体内部的缺陷和物质分布等。
(2)X射线检测设备型号及参数。检测时选用德国进口的飞利浦450X射线探伤机,该机具有灵敏度高,穿透力强的特点;根据工件材质和厚度,通常电压选用100KV~360KV,电流选用 10mA,透照时间选用2min; 胶片选用爱克发工业胶片。
3、 实验结果
3.1 超声波检测结果
对上述三种类型的裂纹缺陷进行水浸横波超声波检测,其结果见图 11-17。
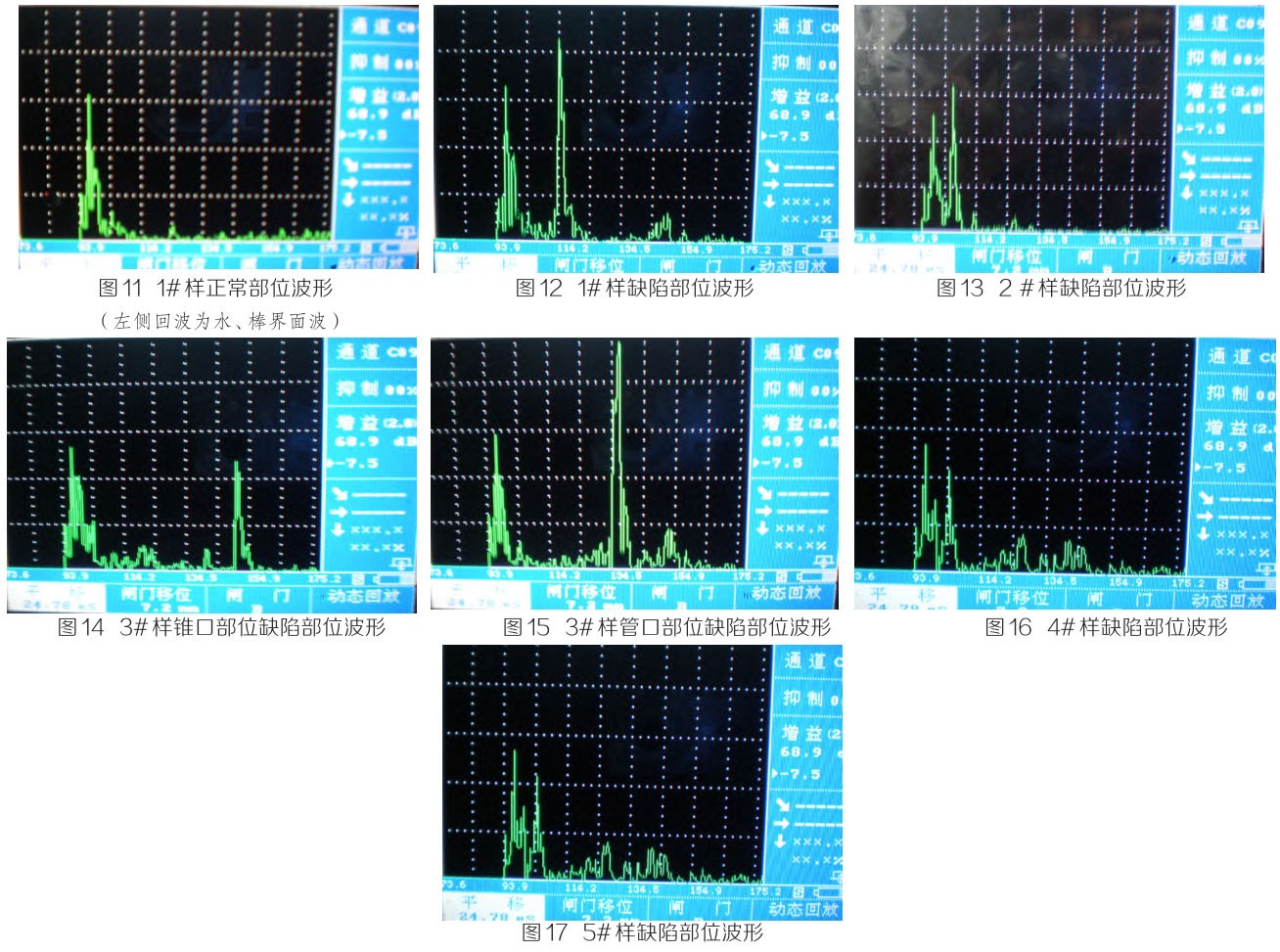
从图中的检测试验情况可以看出,上述三类缺陷,通过超声波检测是可以发现的。若再进一步确定方法,设计实验、确定人工参数试样后,该类产品中的缺陷是具有可检性和可控性的。
3.2 X 射线检测结果
(1)选取具有代表性的三种样品进行 X 射线检测,具体方法是每个样品从相互垂直的两个方向进行 X 射线检测。如图 18-20。
从图中的检测情况可以看出,由于铌铪合金比较致密,上述三种样品中,仅 3# 样品可以发现其内部存在的缺陷,其它两种样品是无法发现样品中所存在的缺陷的。
(2)检测结果如下 :如图 21-26。
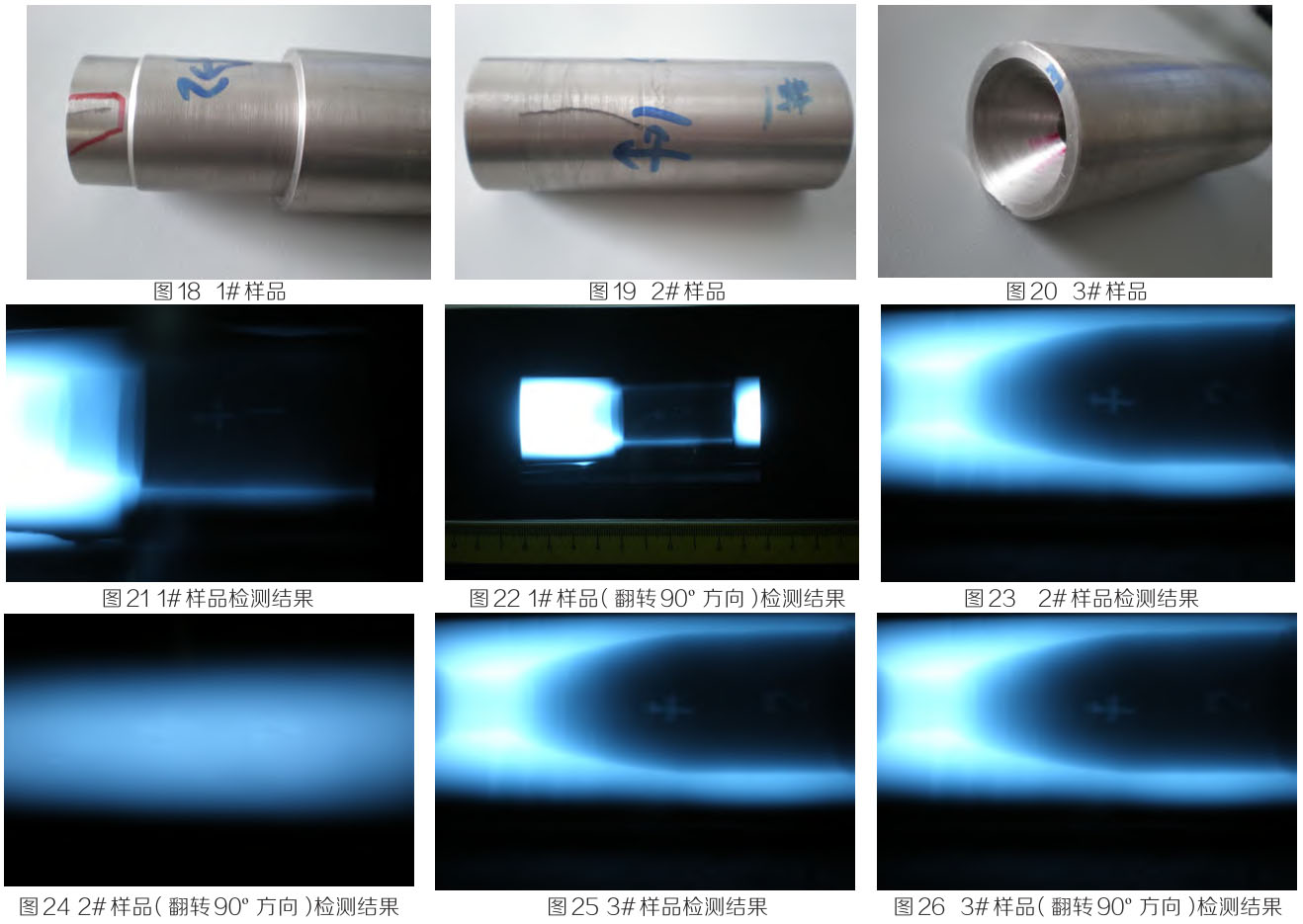
4、 缺陷特征及原因分析
4.1 缺陷特征
通过对缺陷部位进行多方位的观察,我们发现该缺陷具有如下特征 :
第一类缺陷裂纹从棒材表面向内部逐渐延伸,裂纹长度及深度不等,与棒材整体存在一定的角度,大部分约为 45度,并且在分布上没有规律可循,具有典型的锻造折叠裂纹特征。
第二类缺陷为机加后发现的内表面裂纹,该缺陷大部分处于棒材的中心部位,并且均在棒材的一端。
第三类缺陷为机加后发现的外表面较浅的小缺陷,由于此时棒材已进行了部分机加工,外径变小,缺陷已部分切除掉,但通过对残留部分进行观察,可以判定同属于第一类缺陷。其在分布上是随机的。
通过对上述样品存在三类缺陷部位进行观察,缺陷部位没有存在异类金属和非金属所形成的夹杂和偏析,不存在冶金缺陷问题。
4.2 缺陷产生原因分析
该批产品经过熔炼——挤压—锻造——机加——检查——入库这些工序后交付用户。产品在后期生产过程中需要不断进行修磨、加热、锻造及切头等工序,并最终进行表面加工至合同所要求的尺寸公差范围内。在这里修磨及锻造是非常重要的,若坯料表面修磨不彻底,或由于局部修磨较深,则锻造后将产生裂纹将或坯料折叠,最终导致成品外表面存在裂纹和折叠 ;压下量增大有利于提高产品的锻透性,改善金属的内部组织,但如果过大,继续锻造时就会形成折叠 ;同样对送进量的控制也是非常重要的,若送进量过小或锻造过程中送进量控制不理想 , 也容易产生横向折叠,即我们所说的锻造折叠。并且变形量仅集中在表面,使内外组织不均。就会形成前面的说的第一类缺陷。
另外,在锻造过程中,由于其变形特点,使棒坯的心部和表层金属流动性有很大的差异,在棒材的头部均会产生不同程度的缩尾,通常对该缩尾采用锯切的方法去除,随后通过目视检验确认,因缩尾仅位于棒材头部区域,通常的方法是可以完全去除的,但由于该类产品在机加工中较粘,棒材表面和两端在进行车(磨)光及切头后机加后金属屑非常容易将缺陷掩盖,与机加工后的痕迹混淆在一起,如果个别非常小的裂纹,检查员目视不易发现很容易引起漏检,棒材在加工过程中形成的缩尾如果未彻底切除干净就会形成前面的说的第二类缺陷。
5、 结论
上述缺陷的产生原因是由于在锻造过程未将锻造折叠和上一道锻造折叠因未修磨干净所产生的裂纹以及锻造缩尾未清除干净而保留了下来形成的。
通过上面的检测情况可以看出,超声波检测是可以发现的,因此通过进一步的工作,对该类产品的这种缺陷具有可检性和可控性 ;而 X 射线检测则无法有效发现此类问题。
制定合理的生产工艺,加强对锻造过程中压下量及送进量控制,最大程度避免上述缺陷的产生。
加强对机加工后产品检查力度,不漏检和误判,确保产品符合使用要求。
参考文献:
[1]李青云等 . 稀有金属材料加工手册 [M]. 北京 :冶金工业出版社,1984.25-28.
[2]史亦伟等 . 超声检测 [M]. 北京 :机械工业出版社 ,2012.22-25.
[3]郑世才等 . 射线检测 [M]. 北京 :机械工业出版社 ,2011.40-42
无相关信息