天津化工厂离子膜工程根据工艺要求采用了大量的TA2工业纯钛管,直径范围φ18mm~φ500mm,壁厚1.5mm~6mm。TA2材料属首次焊接钢种。TA2工业纯钛比重小、比强度高、塑性及韧性良好、耐腐蚀性能好、高温强度较高,但由于其导热系数低、热容量小、线膨胀系数大,在高温下具有很高的活泼性,极易被氮、氢、氧等污染,引起金属脆化,造成气孔、裂纹等缺陷,可焊接性较差。在施工工期紧、焊接工作量大的条件下,为攻克钛管焊接难题,做了如下试验,并取得成功。
1、TA2钛管焊接工艺性试验
1.1 钛管工艺方案的制订
TA2钛管焊接中易形成冷裂纹、焊接接头区易脆化、对气孔较敏感,在制订焊接试验方案中,针对其焊接特性进行了认真分析并做了必要的前期准备。
1.1.1 由于钛材在焊接时熔池温度较高,且熔池在高温停留时间较长,晶粒长大粗化严重,同时在焊缝中氧、氢、氮含量较多时,焊缝和热影响区的性能变脆,焊后易出现冷裂纹和延迟裂纹。为减少焊缝及热影响区产生冷裂纹的倾向,选用对焊件热输入量相对较小的钨极氩弧焊。
1.1.2 为增强焊缝和热影响区的抗脆化倾向,避免因填充焊丝带入过量碳、氢、氧等元素,降低钛材塑性和韧性指标,在焊接过程中除加强保护措施外,应采用与母材等成分的焊丝。
1.1.3 为减少焊缝在焊接中产生气孔,应当在焊前对焊丝、焊件表面的氧化膜和其它杂质进行认真清理、清洗,采用合理的焊接工艺参数。
1.1.4 根据离子膜工程钛管的规格尺寸及有关资料介绍的参考工艺值,选择了适当的管径及壁厚(φ89×3)制订出供钛管焊接工艺规范参数,详见表1。

1.2 焊接工艺方案的实施
根据制订的焊接工艺方案,进行了两次焊接工艺试验,第一次焊接试验焊了2对钛管(试件编号TA2一1、TA2一2),第二次焊接试验焊了3对钛管(试件编号TA2—3、TA2—4、TA2—5),试件形式及尺寸见图1。
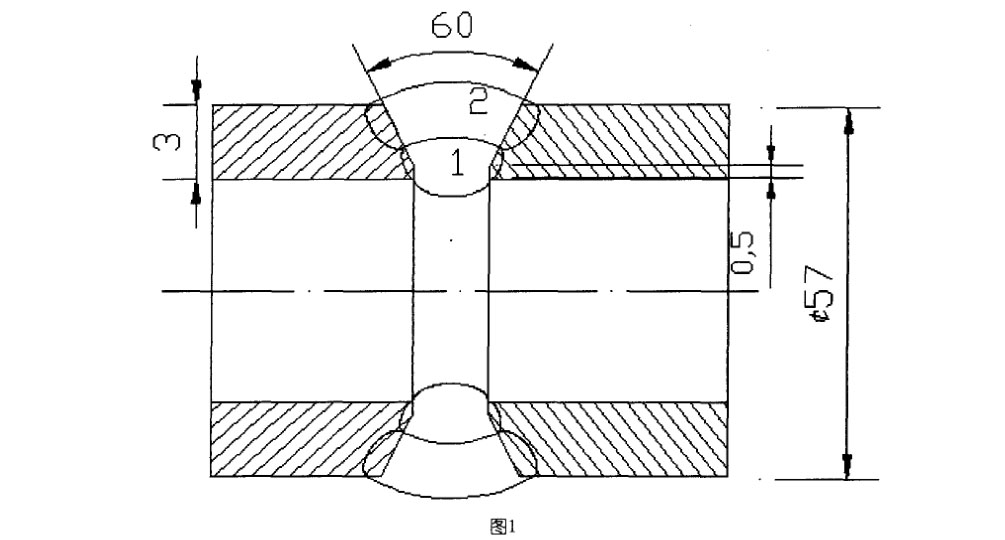
1.2.1 第一次焊接试验因经验不足焊后的焊缝质量较差,试件填充焊丝材质均为与试管同质的TA2焊丝。焊接试验时采取的主要措施是施焊前对焊丝表面及管件坡口内外和邻近区域分别用不锈钢丝刷、酸洗+丙酮的方式进行清洗,酸洗配方为3%HF+3%HNo3+余量H2O,在酸洗液中浸泡15min,然后实施试件的组对及焊接。其中TA2一1、TA2一2试件实测的焊接参数见表2、表3。在焊接过程中每对试管均焊两层,每层焊缝都采用填充焊丝法并在试件背面通氩气保护,采用单面焊双面成型工艺。
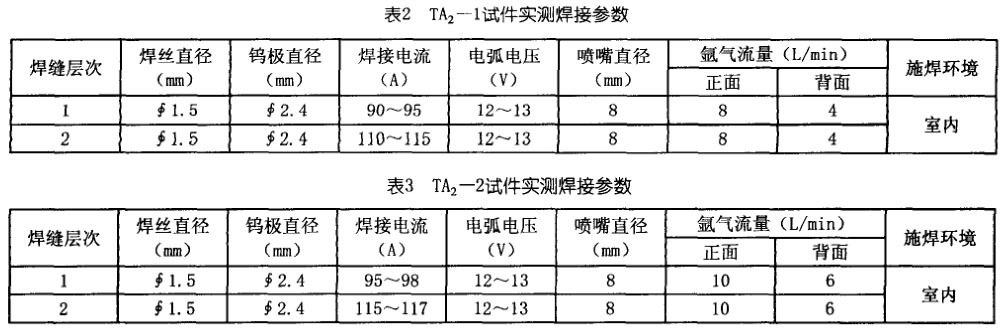
焊后对2对钛管试件分别进行了外观检验、x射线探伤检验、力学性能检验,其检验结果如下。
1.2.2外观检验
焊接TA2一1钛管试件后发现焊缝氧化较严重,随后在焊接TA2一2试件时加强了正面和背面的氩气流量保护,但2对试件焊后焊缝表面颜色仍呈灰白色,氧化色彩较强,说明焊接过程中保护气流挺度偏弱形成层流,使焊缝氧化现象较严重:TA2一1试件打底层有7个表面气孔,经修磨焊补后盖面层有l0个表面气孔,无裂纹;TA2一2试件打底层有4个表面气孔,经修磨焊补后盖面层有8个表面气孔,无裂纹;焊缝背面均己焊透且成型良好。
1.2.3 焊缝X射线探伤检验
在TA2一1、TA2—2试件的x射线探伤底片显示焊缝内存在多量气孔,探伤级别均为Ⅳ级。
1.2.4 力学性能检验
TA2一1试件压扁试验,压板间距(H)34mm合格,实测压扁值为62mm时焊缝部位开始出现裂纹。TA2一2试件压扁试验,实测压扁值为69mm时焊缝部位开始出现裂纹。TA2一1、TA2一2试件的抗拉强度值都低于TA钛材标准值440~620MPa(GB/T3624)。力学性能检验结果见表4。

1.2.5 原因分析
针对试件焊缝内存在多气孔、压扁试验不合格、焊缝氧化等问题进行了分析,初步结论为:氩气保护流量偏低;保护托罩及保护措施不完善;试管清洗后焊接前的时间间隔过长,导致试管、焊丝在存放期形成新的氧化膜;试管表面清洗效果不佳影响焊缝质量。
1.2.6 改进措施
增加焊缝正面和背面氩气保护流量,将焊缝正面氩气保护流量由8~10L/min增加到12~16L/min,将焊缝背面氩气保护流量由4~6L/min增加到7~10L/min:增加保护拖罩尺寸,做到拖罩外边缘与试件外侧紧密贴合且弧度一致,以增加焊接区的保护面积和延长焊接区的保护时间;改进保护罩结构,将保护拖罩的材质由原来的镀锌钢板改为柔性较好的紫铜板,通保护气用管由单一向上的排孔改为在原有排孔基础上同时在侧面90。方向上各增加一排孔并用铜丝网包覆,避免因保护气流增大后出现紊流。同时改进焊缝背面保护措施,除增加保护气流量以外,根据氩气密度大于空气的特点,试件背面通保护气点选择在低点,而排气点选择在试件高点,为减少背面保护气体的损失和提高背面保护效果,对试件暂不焊接的坡口部位用胶带纸封住;细化试件焊前清洗程序,适当增加机械打磨深度,延长酸洗浸泡时间至20min,试件坡口酸洗后增加流动水冲刷和烘干程序,清洗后试件放置时间最长不超过2h。
1.3 改进工艺后的验证性焊接试验
为增加焊接试验的可比性,第二次试验共焊接了3对试件,其规格、接头形式与第一次相同。
试件编号为TA2—3、TA2—4、TA2一5。试件坡口内及两侧机械打磨深度不小于0.01mm,酸洗液中浸泡时间20min,水冲洗后用强力风扇吹干。
1.3.1焊接试验
TA2—3、TA2—4、TA2—5试件的实测焊接参数见表5、表6、表7。
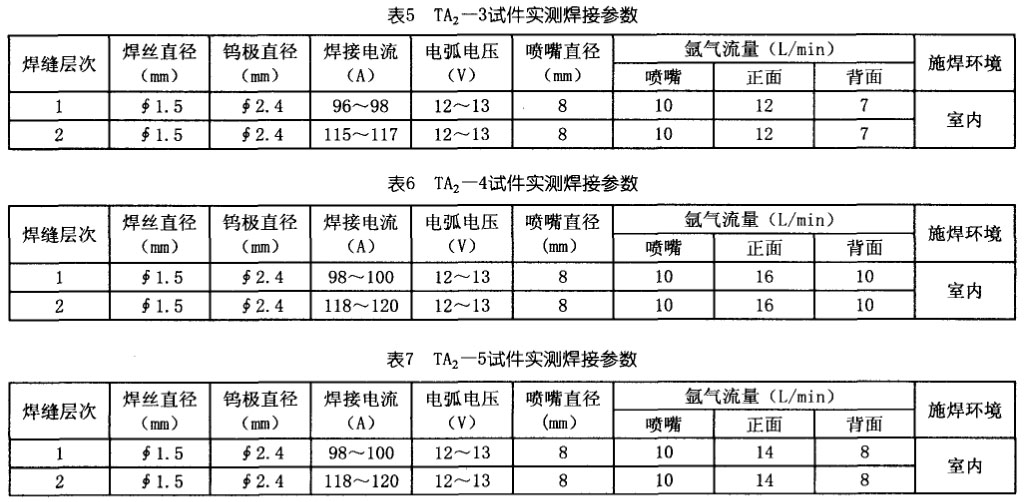
焊后对3组试件分别进行了外观检验、x射线探伤检验、力学性能检验,各项检验结果如下。
1.3.2外观检验
TA2一3、TA2一5试件的打底层及盖面层均未发现气孔及裂纹,TA2一4试件的打底层表面气孔4个,盖面层表面气孔5个,打底层及盖面层均未发
现裂纹;TA2一3、TA2一5试件焊缝背面颜色均为金黄色,盖面层焊缝均呈银白色,TA2一5试件的盖面层焊缝颜色更白亮,TA2一4试件的焊缝背面为深蓝色,盖面层焊缝颜色呈浅蓝色,说明保护气流量不宜过大,过大易使保护气流形成紊流,保护效果反而变差;3组试件焊缝背面均已焊透。
1.3.3焊缝x射线探伤检验
TA2一3试件x射线探伤底片显示焊缝内有4个0.5~lmm气孔(/I级片);TA2一4试件x射线探伤底片显示焊缝内有9个气孔,并在焊缝的起弧与收弧搭接处有1处密集气孔(IV级片)。
TA2一5试件x射线探伤底片显示焊缝内有1个0.7mm气孔(I级片)。
1.3.4 力学性能检验
TA2—3、TA2—5试件压扁试验合格,TA2—4试件压扁试验不合格;TA2—3、TA—4、TA2—5试件抗拉强度值均高于标准值440~620MPa(GB/T3624),仅TA2—4试件抗拉强度值略高于其下限值。力学性能检验结果见表8。

2、焊接试验结果分析
从两次焊接试验对比不难看出,钛管焊接中存在的主要问题是焊接接头的氧化和气孔,正常焊接条件下焊接裂纹产生的概率较小。如何减少焊接接头的氧化和气孔,避免产生焊接裂纹,是保证钛管焊接质量的关键所在。如焊丝、焊件焊前清理效果,保护气体流量过小或过大,保护措施不当等,都会将保护效果变差,使熔池金属发生氧化并在冷却凝固过程中吸收的气体来不及逸出残留在焊缝金属中,导致焊接接头出现氧化和气孔。
3、焊接工艺试验结论
3.1 焊丝、焊件焊前必须进行机械及化学清洗,保证足够的化学清洗时间,清洗后焊接前的问隔时间不宜超过2h。
3.2 焊前按有关标准、规范要求组对焊件。
3.3 在焊缝的正面、背面选择正确的保护措施和适当的氩气保护流量。
3.4 选择合适的焊接工艺参数。
4、工程应用
钛管焊接试验初步成功后,工作重点转向离子膜工程钛管现场焊接,以验证焊接试验工艺参数的适用性。
4.1 首批TA2钛管焊接
4.1.1 首批57X3mm钛管对接共38道焊口,施焊中根据第二次焊接试验结果制订的焊接工艺参数见表9。

4.1.2 对第一天焊接的8道焊口进行了x射线探伤检验,其中有3道焊口探伤底片上有多量超标气孔缺陷且焊缝表面呈浅蓝色氧化色彩,现场分析认为产生气孔的原因有:管件化学清洗后与实际施焊时间间隔过长(超过4h),因焊工忙于其它工作,造成酸洗后管件表面形成新的氧化薄膜。焊接工作台面不清洁,导致酸洗后焊件被再次污染;焊接操作时距厂房门口较近,管的一端未加封堵,在对流风作用下,电弧轴线中心发生偏移,空气混入熔池,使熔池及背面保护效果变差,导致焊缝金属中产生多量气孔。
4.2 改进措施
选择封闭条件较好,通风设施比较齐全的施工厂房,开辟专用钛管焊接场地,并用橡胶铺设地面,操作人员脚穿鞋套,带洁净手套,用于组焊的焊接工作台面工作前必须进行仔细擦拭,以减少污染;必须做到化学清洗后管件、焊丝放置时间不得超过2h,否则焊前必须重新清洗;焊接前首先在管内通35min氪气后再进行焊接。对于管径乏159mm的管件,为避免氪气的浪费并增加焊接区保护效果,采取局部隔离充氪气保护措施,结构简图见图2。为加强焊缝背面保护效果,对点固后尚未焊接的焊口表面粘贴胶带纸。
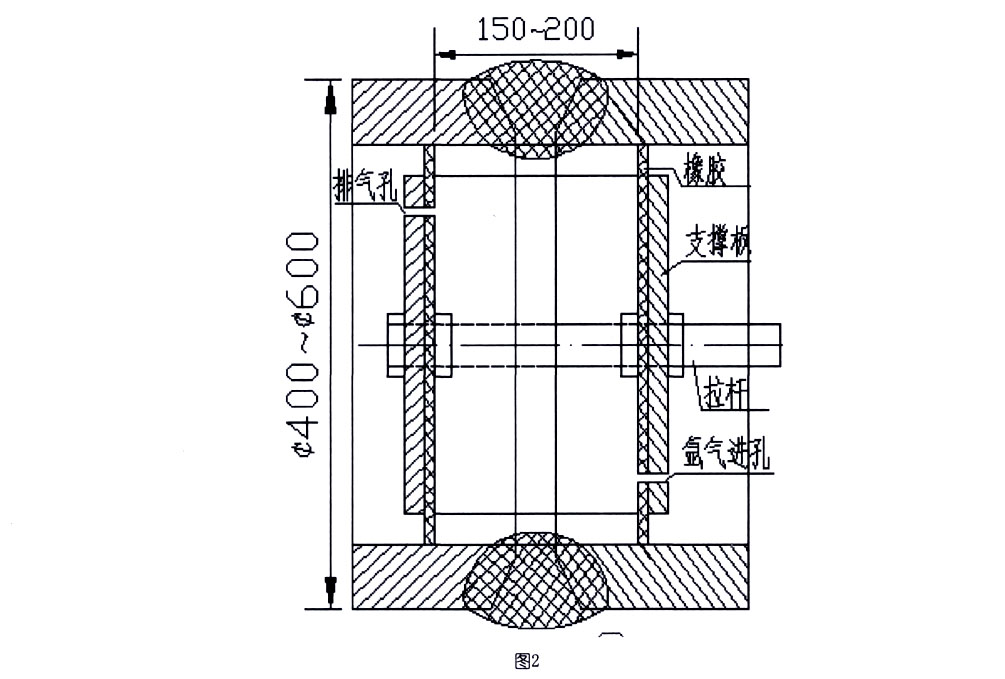
4.3 实施
4.3.1 对剩余30道焊口按改进后工艺进行焊接,并分别进行了X射线探伤检验,探伤结果显示除有1道焊口气孔缺陷超标CN级片)外,其余29道焊口的气孔数量大大减少,均达到探伤合格标准,其中I级片7道,II级片18道,田级片5道。
4.3.2 现场实践表明,改进后的焊接工艺措施更贴近实际,更趋千合理,达到了较好效果,整个离子膜工程TA2钛材管道长2700m共1154道焊缝,仅有7道焊口不合格。优良的焊接质益为离子膜工程按期完工,创造了必要的条件。
参考文献
[1]李亚江,王娟,刘强有色金属焊接及应用[M]北京:化学工业出版社,2006,112-116
[2]压力容器相关标准汇编(第四版,上卷)[S].北京:中国标准出版社,2006,414.
相关链接