TC11钛合金大型燃机转子零件结构采用电子束焊接方法实现整体制造 。 受接头型式 、 锻件冶金质量 、 零件表面状况及焊接工艺等诸多因素的影响 , 电子束焊接过程中可能会
形成工艺缺陷 。 这些工艺缺陷包括内部气孔 、 裂纹和局部凹陷 ( 低于焊后机械加工面尺寸 ) 等 , 焊缝裂纹和表面凹陷以及超岀焊接质量检验标准规定尺寸的内部气孔都必须修复补焊 。 补焊方法为手工钨极氩弧焊 , 填充材料为 TA0 纯钛焊丝 。
对挖排后的缺陷采用氩弧焊补焊 , 因填充 TA0 纯钛焊丝导致缺陷区域重新熔融合金化,可能会形成该焊接区域的微观组织差异 , 影响该区域的力学性能 , 另外 , 随挖排和补焊区
域大小 ( 尺寸 ) 的不同 , 其影响程度也可能不相同 。 因此 , 有必要针对电子束焊缝不同类型 、 不同深度和尺寸的超标缺陷开展相应的补焊工艺研究 , 评定补焊措施和补焊工艺对零件电子束焊接接头质量和力学性能的影响 。
1、试验材料与过程
试验使用的材料为 TC11钛合金板材 , 其化学成分见表1 、 力学性能见表 2 。 试板规格为 400mm x 150mm x 15. 5mm( 带锁底 ) 及 400mm x 150mm x 8. 5mm 。 两块试板经电子束焊接后 , 在焊缝上选择 6 处位置 ( 编号依次为 : 1 、 2 、 3 、 A 、 B 、C ) 进行机械挖排来模拟电子束焊接超差缺陷 , 然后进行手工氩弧焊补焊工艺试验 。
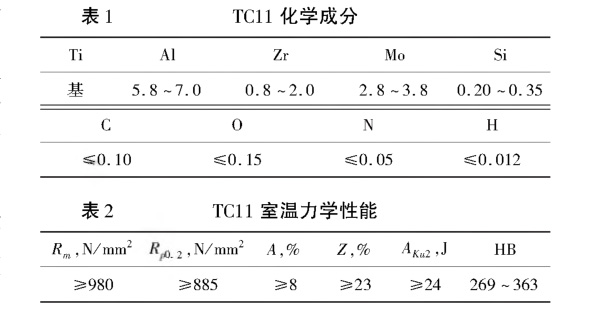
由于通过焊缝的 X 射线检测光片只能确定缺陷尺寸 , 不能确定缺陷的深度位置 。 根据零件焊缝缺陷可能存在的深度和零件接头处加工后的最终尺寸 , 对模拟缺陷的挖排深度
采取由浅至深原则 , 最终确定缺陷补焊试验缺陷的挖排深度分别为 2mm 、 5mm 和 8mm 。
采用手工机械磨削方式 , 对电子束焊接超标缺陷进行挖排,缺陷挖排后状态如图 1 所示 。
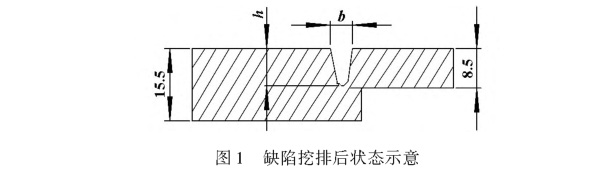
焊前对挖排区域表面严格清理 , 采用手工氩弧焊工艺进行补焊 , 填充材料为 0 2.0mm 规格的 TA0 纯钛焊丝 , 氩弧焊焊机型号为 : PRESTPTIG 300 AC/DG 。 手工钨极氩弧焊补焊工艺按照 HB/Z 120( 钛及钛合金钨极氩弧焊接工艺 》 规定执行 ,所采用的焊接工艺参数见表 3 。
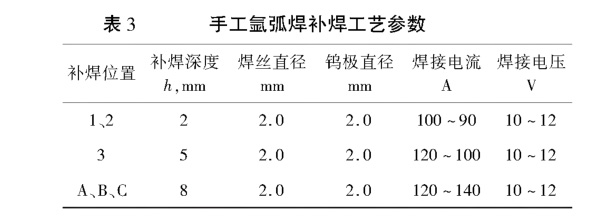
对氩弧焊补焊后的试板进行 X 射线无损检测 , 焊缝质量满足 H255.105. 111 -89 《 电子束焊检验和允许的缺陷 》 I级要求 。 补焊合格的焊接试板随实际零件进行热处理 , 热处理制度为 (530 ±10)t/(11 ~12)h,FC o在氩弧焊补焊过的 6 处位置取样 , 并加工成厚度为 6mm的标准拉伸力学性能试样 , 拉伸工作区宽度为 20mm 。 为保证所取力学性能试样包含补焊区域 , 取样时沿试板上层取 。加工完成的试样再进行 X 射线检测 。
2、试验结果与分析
2.1 挖排缺陷深度为 2mm 的氩弧焊补焊
1 号和 2 号位置挖排深度为 2mm, 挖排区域尺寸分别为212mm x 6mm 和 14mm x 6mm 。图 2 所示分别为 1 号和 2 号位置氩弧焊补焊前后的状态 。
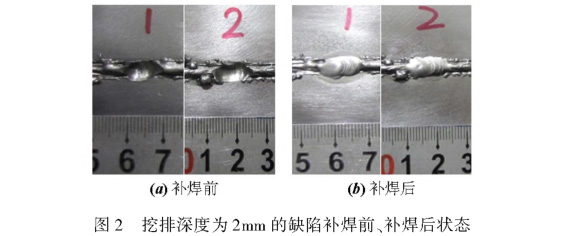
图 3 所示分别为 1 号和 2 号位置补焊后加工去除焊缝余高和锁底前后 X 射线底片的对比 。 由图 3 可以看岀 , 在保留焊缝余高和锁底状态下, X 射线底片上并未发现有色差 。
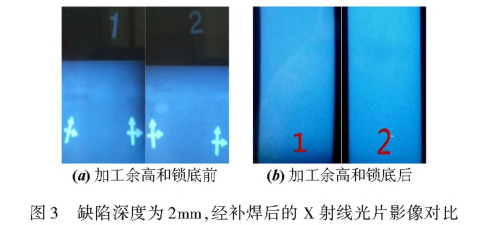
但经机械加工去除焊缝余高及锁底后 , X 射线光片影像显示 , 补焊区域与原电子束焊缝相比 , 存在浅灰色影像的色差 。但由于该位置挖补深度较小 , 色差不太明显 。
2.2 挖排缺陷深度为 5mm 的氩弧焊补焊
3 号位置挖排深度为 5mm, 挖排区域尺寸 12mm x 8mm,该位置氩弧焊补焊前后的状态如图 4 所示 。
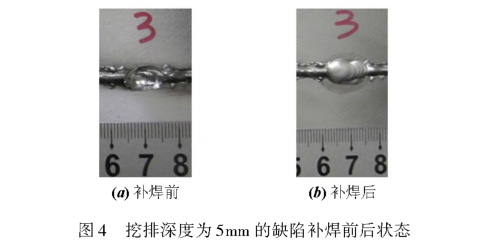
图 5 所示为 3 号位置补焊后加工去除焊缝余高和锁底前后 X 射线光片影像对比 。 可以看岀 , 在加工去除焊缝余高及锁底后 , 补焊位置呈现浅灰色影像 , 与原电子束焊缝有较明显的色差 。 其色差度超过 2mm 深度缺陷的补焊 2. 3 挖排缺陷深度为 8mm 的氩弧焊补焊挖排深度为 8mm 的位置分别为 A 、 B 、 C 3 处 , 其挖排区
域尺寸分别为 14mm x9mm 、 15mm x 7mm 和 13mm X 7mm 。
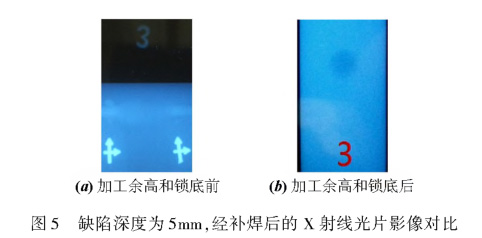
图 6 所示分别为 3 处位置氩弧焊补焊前后的状态 。
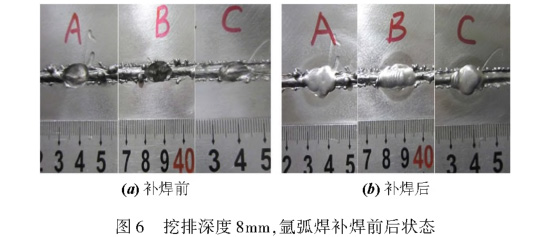
图 7 所示分别为补焊深度为 8mm时加工去除焊缝余高和锁底前后 X 射线底片影像对比 。 从图 7 可以看岀 , 在去除焊缝余高和锁底前 , 由于余高和锁底厚度对射线透射的干
扰 ,X 射线光片影像并未发现明显色差 。 经机械加工去除余高和锁底后 ,X 射线光片影像显示氩弧焊补焊区域同原电子束焊缝差异明显 。 可以认定 , 随着挖补深度增加 , 填充的
TA0 纯钛焊丝在补焊熔池区域中的熔敷比也明显增加 , 所形成的弧焊区域组织组成对 X 射线透射率也增加 , 因此影像中的色差也明显增加 。
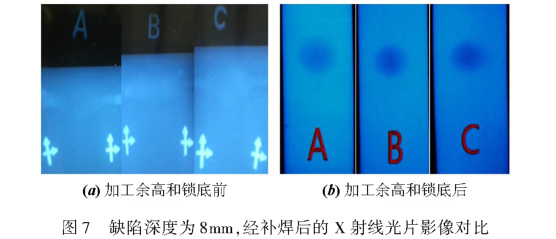
2.4 补焊深度及尺寸对接头力学性能的影响
对 3 类缺陷经补焊后的接头截取标准的力学性能试样 ,经随零件真空热处理后进行性能测试,测试结果见表 4 。
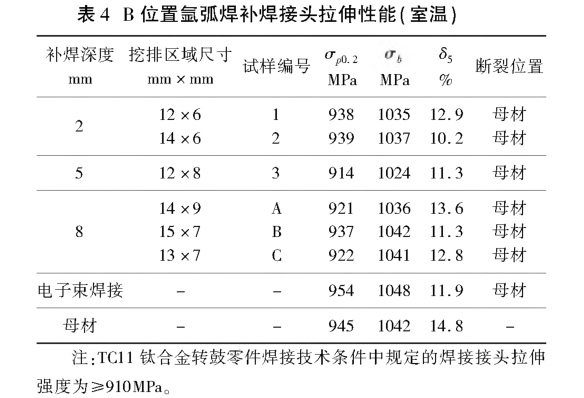
注 : TC11钛合金转鼓零件焊接技术条件中规定的焊接接头拉伸强度为 A910MPa 。
从表 2 可以看岀 ,3 种类型的缺陷经补焊后的接头力学性能较原电子束焊接接头无明显差异 , 性能试样均断裂在接头母材部位 , 如图 8 所示 。 可以认为 , 其强度与零件 TC11 合
金母材相当 , 均能够满足技术条件中规定强度不低于 910MPa 的要求。
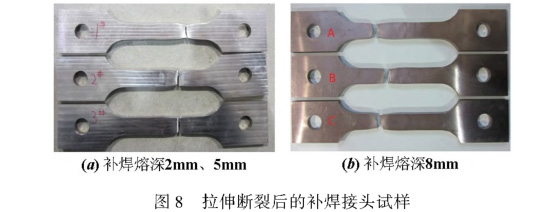
3、结 论
(1) 通过手工机械磨削方式挖排 , 并采用手工氩弧焊补焊工艺 , 能够有效地排除零件电子束焊缝超标缺陷 , 补焊工艺质量能够满足技术标准 H255. 105. 111 -89( 电子束焊检
验和允许的缺陷 》 规定的 I 级焊缝要求 。
(2) 电子束焊缝缺陷的挖排 、 氩弧焊补焊工艺研究结果表明 ,3 种类型的缺陷经补焊后的接头力学性能较原电子束焊接接头无明显差异 , 性能试样均断裂在接头母材部位 ; 其
强度与零件 TC11合金母材相当 , 均能够满足技术条件中规定强度不低于 910 MPa 的要求 。
(3) 因填充 TA0 纯钛焊丝 , 补焊区域重新合金化 。 所获得的组织组成和组织形态对 X 射线的透射影响与原电子束焊缝不同 , 导致在 X 射线影像岀现不同程度的色差 。 随着填
充量的增加 , 其透射程度增加 , X 光片的色差更加明显 。
(4) 补焊结果表明 , 通过挖排和氩弧焊补焊工艺 , 并填充TA0 焊丝 , 能够对 TC11钛合金转子类零件电子束焊接生产过程的超差缺陷实施补焊修复 , 同时也证明了本文的补焊工
艺合理 。
相关链接