TC4钛合金组成为Ti-6Al-4V,属于(α+β)型钛合金,由于具有密度低、比强度高、优良的耐腐蚀性能和较好的焊接性能等而被广泛应用于航空航天、石油化工、生物医学等领域,其使用量已经达到世界钛消费品的50%以上。传统钛合金的制造技术由于存在需要大型锻压设备、材料利用率低和难易制造复杂形状结构件等问题而在一定程度上限制了诸如TC4钛合金等的应用。3D打印(增材制造)快速成形技术,以数字模型文件为基础,运用粉末状金属或塑料等可粘合材料,通过逐层打印的方式来实现实体零部件的制备,具有快速性、低成本、高柔性和高集成化等特性而被关注。国内外在送粉式3D打印钛合金的研究多集中在组织控制和成形性能上,通过后续的热处理可以获得性能良好的成形件,但是绝大多数采用的是CO2激光或者旁轴送粉,而采用光纤激光+同轴送粉方式的研究较少[1-2]。因此,本文采用同轴送粉的沉积方式研究了成形工艺和热处理工艺对3D打印TC4钛合金组织与性能的影响,为高性能TC4钛合金的制备提供了新的途径,并有助于3D打印钛合金工艺的优化与性能提升。

1、试验材料与方法
试验基材为尺寸160mm×50mm×5mm的热轧TC4钛合金板材,使用前需要进行表面去氧化膜(化学清洗法)、丙酮清洗和烘干等步骤。3D打印所用TC4粉末为采用等离子旋转电极法制备的粒度为-140~+320目球形粉末,化学成分(质量分数,%)为:6.1Al、4.1V、0.14Fe、0.02C、0.02N、0.003H,余量为Ti。3D打印的主要装备包括德国YSL-10000型光纤激光器、德国KUKA公司的六轴机械人、德国YC52同轴熔覆头、PT2/3型双桶送粉器以及气体保护装置(氩气)等。采用同轴送粉式3D打印所采用的同轴熔覆头焦距为200mm、聚焦光斑直径设定为准0.25mm、熔覆头喷涂与基材之间的距离控制在11mm,在制备过程中的保护气包括同轴保护气6L/min、载粉气4.5L/min以及束流气12L/min。为了对比不同3D打印工艺参数对TC4钛合金成形性能的影响,主要通过控制激光功率(300~800W)、扫描速度(0.12~0.60m/min)、送粉速度(0.8~7.6g/min)和扫描方向(单向和往返)来制备沉积态TC4钛合金。采用石英管真空密闭方法对3D打印TC4钛合金成形件进行固溶和时效热处理,固溶处理温度在900~1000℃,保温时间为1h,时效处理温度为540℃,保温时间为4h,都采用空冷(AC);另一种对比热处理工艺为950℃保温1h后随炉冷却(FC)。对TC4钛合金成形件的横截面和纵截面进行打磨、机械抛光,然后采用体积比HF∶HNO3∶H2O=1∶2∶5的腐蚀剂进行腐蚀后,在SMZ1500体视显微镜上进行低倍组织观察。高倍组织观察采用体积比为HF∶HNO3∶H2O=3∶10∶87的混合试剂腐蚀后,在OlymplusGX51光学显微镜上观察;采用捷克TESCANVEGAⅡ型扫描电子显微镜对组织和断口形貌进行观察;采用美国MTS-810液压伺服电子万能拉伸试验机对TC4钛合金试样进行常温拉伸力学性能测试,拉伸速率为1.5mm/min,以3组试样平均值作为测试结果。
2、试验结果及讨论
2.1激光功率
图1为单向扫描方式和扫描速度为0.36m/min条件下不同激光功率下TC4钛合金的低倍宏观形貌。可以看到,激光功率为300W、500W和800W时的宏观组织都为定向外延生长的粗大β柱状晶形态,但是不同激光功率下柱状晶的尺寸存在明显差异。当激光功率为300W时,TC4钛合金中β柱状晶的晶粒尺寸约为320μm;随着激光功率增加至500W和800W,TC4钛合金中β柱状晶的晶粒尺寸分别为538μm和866μm。由此可见,在扫描方向和扫描速度不变前提下,β柱状晶的晶粒尺寸会随着激光功率的增加而增大。这主要是由于随着激光功率的增加,沉积件熔池中的温度梯度会有所降低,在扫描速度不变情况下,合金中的晶粒尺寸会有所增大[3]。
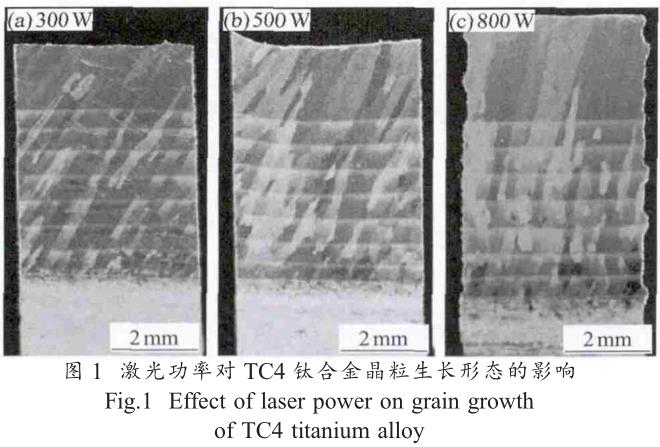
图2为不同激光功率下TC4钛合金的常温拉伸力学性能测试结果。随着激光功率的增加,TC4钛合金的抗拉强度和屈服强度都表现为先升高而后降低的趋势,在激光功率为500W时取得最大值;而断后伸长率随着激光功率的增加而呈现逐渐降低的趋势,在激光功率为800W时,TC4钛合金的断后伸长率为4.80%。从3种激光功率下TC4钛合金
的力学性能上来看,3D打印钛合金的抗拉强度和屈服强度都超过了国标GB/T6614-2014和国标GB/T2965-1996中对铸件和锻件退火态的要求(抗拉强度≥895MPa,屈服强度≥825MPa),但是断后伸长率未超过铸件(6%)和锻件退火态(10%)的标准[4]。
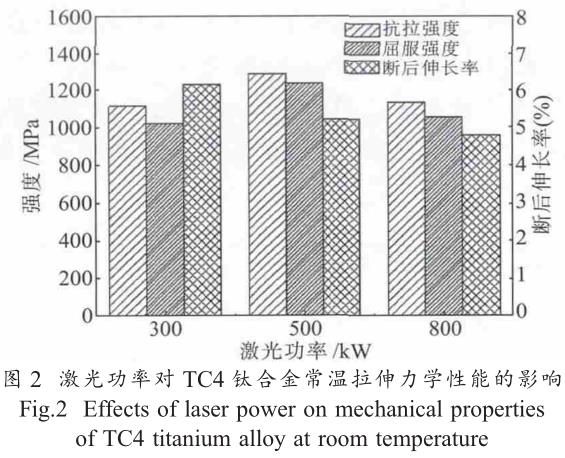
2.2扫描速度
图3为单向扫描方式和激光功率为500W条件下不同激光扫描速度下TC4钛合金的低倍宏观形貌。可以看到,当扫描速度在0.36~0.60m/min时,TC4钛合金的晶粒形态都为柱状晶,而扫描速度为0.24m/min时的晶粒形态为柱状晶和等轴晶。
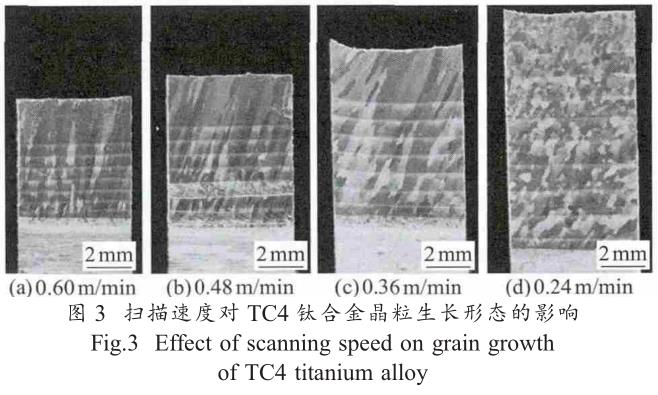
从扫描速度对柱状晶形态的影响上来看,当激光扫描速度从0.24m/min增加至0.60m/min时,柱状晶的宽度呈现逐渐减小的趋势,而柱状晶高度逐渐增加。这主要是由于扫描速度的升高会增加熔池中的温度梯度,熔池冷却过程中的过冷度增加,柱状晶宽度会减小。如果扫描速度较低(0.24m/min),熔池中的温度梯度减小,使得固液界面和熔池内部的形核条件接近一致就会形成等轴晶。此外,还可以发现,随着扫描速度的增加,柱状晶与扫描方向的夹角逐渐增大,在扫描速度为0.60m/min时柱状晶与扫描方向几乎垂直。这主要是由于扫描速度较大时,成形过程中基体上形成的温度场范围变小,晶粒会垂直于熔池中心线生长,而形成了近似于与扫描方向呈90°的柱状晶[5]。
图4为不同扫描速度下TC4钛合金的常温拉伸力学性能测试结果。随着扫描速度的增加,TC4钛合金的抗拉强度和屈服强度都表现为逐渐降低的趋势,而断后伸长率逐渐升高。在扫描速度为0.24m/min时TC4钛合金的抗拉强度和屈服强度分别为1360MPa和1282MPa,而断后伸长率为4.25%;在扫描速度为0.60m/min时TC4钛合金的抗拉强
度和屈服强度分别为1106MPa和1008MPa,而断后伸长率为7.15%。由此可见,单相扫描、激光功率500W、扫描速度0.12~0.60m/min时TC4钛合金沉积件的抗拉强度和屈服强度都超过了铸件和锻件退火态的要求,但是断后伸长率的变化范围与不同激光功率下的沉积件相似,且都未超过铸件和锻件退火态的标准。
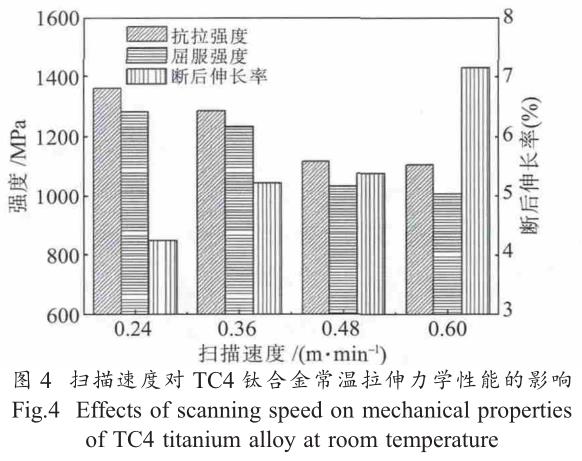
2.3扫描方向
图5为激光功率为500W、扫描速度0.36m/min时单向扫描和往返扫描方式下TC4钛合金的低倍宏观形貌。对比分析可见,在其它工艺参数一定条件下,单向扫描时TC4钛合金的柱状晶呈现定向外延生长趋势,而往返扫描时TC4钛合金的柱状晶由定向生长转变为双相生长,且沉积层间还出现了一定数量的等轴晶,同时可见往返扫描条件下TC4钛合
金沉积件的高度更高。这主要是因为往返扫描条件下会产生较多的热积累,熔池面积更大从而可以吸收更多的粉末,而单向扫描条件下的热积累较少[6],沉积件的高度相对较低;此外,在热积累过程中,往返扫描时熔池中的温度梯度会有一定程度降低,为等轴晶的形成创造了条件,且由于沉积层上部分的等轴晶在沉积下一层时不能完全重熔,因此,宏观形貌中会出现柱状晶和等轴晶交替的形态[7]。
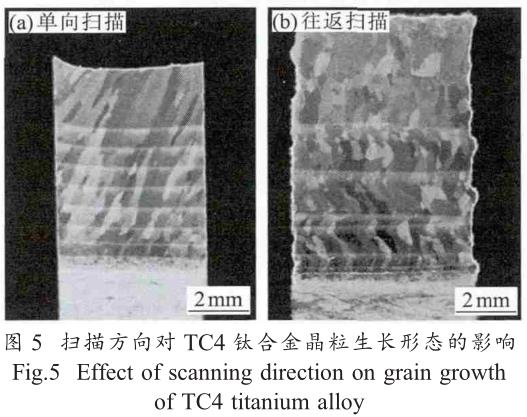
图6为单向和往返扫描条件下TC4钛合金的常温拉伸力学性能测试结果。在其它工艺参数一定条件下,激光扫描方向从单向转变为往返扫描,TC4钛合金的抗拉强度和屈服强度都有所提高,但是断后伸长率却下降较为明显。在往返扫描方式下TC4钛合金的抗拉强度和屈服强度分别为1322MPa和1250MPa,而断后伸长率为2.32%。这可能是由于往返扫描时定向外延生长的柱状晶形态发生破坏,形成了柱状晶与等轴晶交替的形态,在拉伸过程中会有更多的晶界阻碍,而使得往返扫描沉积件具有高强低韧的特征[8]。
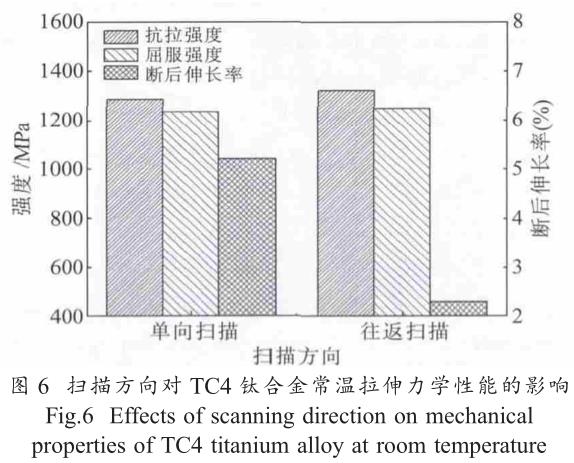
2.4固溶与时效热处理
对沉积态和不同固溶时效热处理工艺下的3D打印TC4钛合金的常温力学性能进行测试,结果见表1。沉积态TC4合金进行910~990℃固溶+540℃时效热处理后空冷得到的试样的抗拉强度和屈强强度有所降低,但是断后伸长率却明显提高;尤其是热处理工艺为950℃/AC/1h+540℃/AC/4h时试样的抗拉强度和屈服强度分别达到1206MPa和1122MPa,而断后伸长率达到13.42%,其强度和塑性都超过了国标对TC4钛合金铸件和锻件退火态的要求。相比950℃/FC/1h的热处理,试样的强度略有提高,但是断后伸长率却大幅度降低至2.42%,明显低于沉积态试样。由此可见,通过固溶和时效热处理可以有效改善沉积态TC4钛合金的强度和塑性,热处理后的冷却速度对钛合金的强度和塑性影响较大,在实际应用过程中应该加以控制。
图7为沉积态、950℃/AC/1h+540℃/AC/4h和950℃/FC/1h热处理态TC4钛合金的金相组织。对于沉积态TC4钛合金,金相组织为马氏体α'针为主的魏氏组织;经过950℃/AC/1h+540℃/AC/4h热处理后,金相组织转变为网篮组织;950℃/FC/1h热处理后金相组织转变为双态组织,合金中部分α相发生球化,而另一部分仍然具有网篮组织特征。其中,魏氏组织的塑性和冲击韧性较差,网篮组织的强度、塑性以及高温蠕变性能较好,而双态组织的强度较高、塑性较差[8]。对比分析炉冷和空冷方式下TC4钛合金网篮组织的扫描电镜显微形貌,结果见图8。
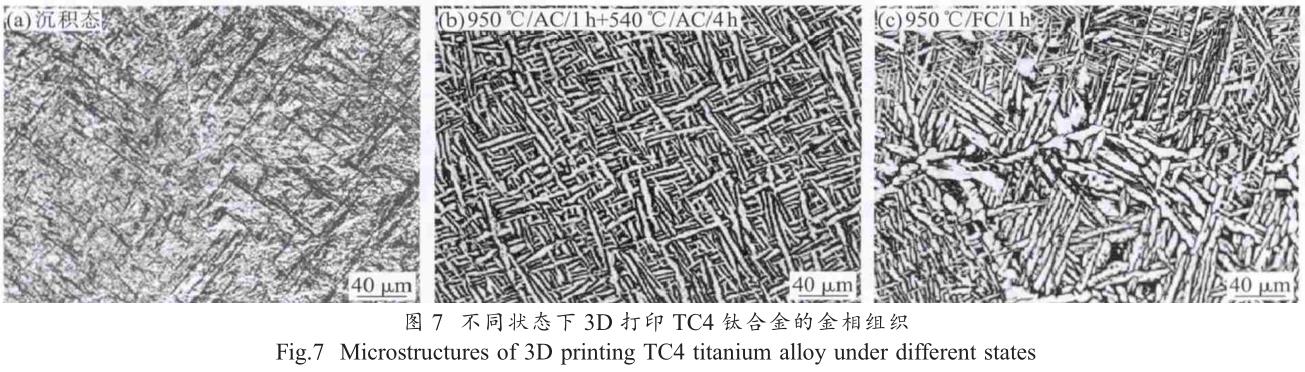
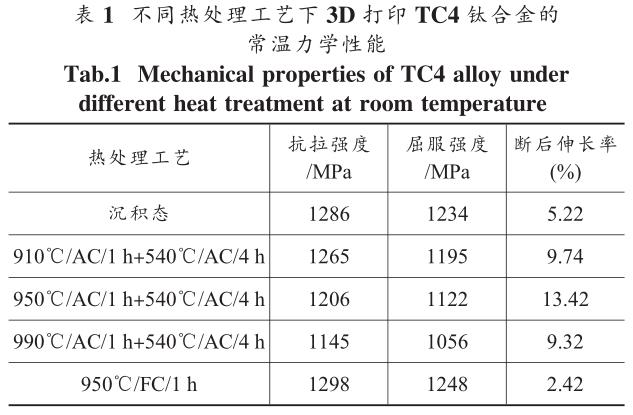
在空冷制度下,TC4钛合金将发生半扩散型相变,合金在固溶处理后得到杆状的初生α相,随后经过时效处理后,初生α相之间的β相会以细小次生α相形式出现(图8(a));炉冷制度下,TC4钛合金将发生扩散型相变,固溶处理后会由于成分偏析而形成双态组织,合金中初生α相之间的β相由于没有后续的时效热处理而并没有析出次生α相(图8(b));同时对比分析可见,炉冷制度下晶界α相和晶内α相都要相对空冷制度下更粗大,受外力作用下的裂纹更容易在炉冷条件下的晶界处萌生和扩展,造成合金的塑性降低。
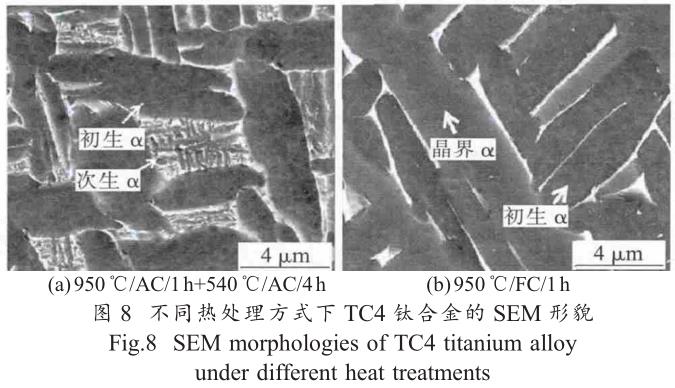
3、结论
(1)在扫描方向和扫描速度不变前提下,β柱状晶的晶粒尺寸会随着激光功率的增加而增大。随着激光功率的增加,TC4钛合金的抗拉强度和屈服强度都表现为先升高而后降低的趋势;在激光功率为500W时取得最大值;而断后伸长率随着激光功率的增加而呈现逐渐降低的趋势。
(2)当扫描速度在0.36~0.60m/min时,TC4钛合金的晶粒形态都为柱状晶。而扫描速度为0.12m/min时的晶粒形态为柱状晶和等轴晶;当激光功率从0.12m/min增加至0.60m/min时,柱状晶的宽度呈现逐渐减小的趋势,而柱状晶高度逐渐增加;随着扫描速度的增加,TC4钛合金的抗拉强度和屈服强度都表现为逐渐降低的趋势,而断后伸长率逐渐升高。
(3)在其它工艺参数一定条件下,单向扫描时TC4钛合金的柱状晶呈现定向外延生长趋势。而往返扫描时TC4钛合金的柱状晶由定向生长转变为双相生长,且沉积层间还出现了一定数量的等轴晶;激光扫描方向从单向转变为往返扫描,TC4钛合金的抗拉强度和屈服强度都有所提高,但是断后伸长率却下降较为明显。
(4)固溶+时效热处理可以有效改善沉积态TC4钛合金的强度和塑性,其强度和塑性都超过了国标对TC4钛合金铸件和锻件退火态的要求。
参考文献:
[1]Dutta B, Froes F H.Additive manufacturing of titanium alloys [J].Advanced Materials& Processes,2014,172(2):18-23.
[2]Nassar A R, Keist J S, Reutzel E W.Intra-layer closed-loop control of build plan during directed energy additive manufacturing of Ti-6Al-4V [J].Additive Manufacturing,2015(6):39-52.
[3]Lin X, Yue T M, Yang H O.Solidification behavior and the evolution of phase in laser rapid rorming of graded Ti6Al4V-Rene88DT alloy [J].Metallurgical
and Materials Transactions A,2007,38(1):127-137.
[4]Heigel J C, Michaleris P, Reutzel E W.Thermo-mechanical model development and validation of directed energy deposition additive manufacturing
of Ti-6Al-4V [J].Additive Manufacturing,2014(5):9-19.
[5]Carroll B E, Palmer T A, Beese A M.Anisotropic tensile behavior of Ti-6Al-4V components fabricated with directed energy deposition additive manufacturing [J].Acta Materialia,2015,87:309-320.
[6]Gong H, Rafi K, Gu H.Influence of defects on mechanical properties of Ti-6Al-4V components produced by selective laser melting and electron beam melting [J].Materials & Design,2015,86:545-554.
[7]Tsai C J, Wang L M.Improved mechanical properties of Ti-6Al-4V alloy by electron beam welding process plus annealing treatments and its
microstructural evolution [J].Materials & Design,2014,60:587-598.
[8]Zhao X, Li S, Zhang M.Comparison of the microstructures and mechanical properties of Ti-6Al-4V fabricated by selective laser melting and electron beam melting [J].Materials & Design,2016,95:21-31.
相关链接