引 言
磁控溅射是一种常见的物理气相沉积方法,具有 沉积温度低、沉积速度快、方便多个靶材进行材料合成 等优点,常用于金属[1-3]、半导体[4-6]、绝缘体[7-9]等多 种薄膜材料的制备。然而,在磁控溅射过程中,不同材 料的溅射原子角分布差异很大[10],而且合金材料的一 些参数不易设定,因此采用晶振片监测沉积薄膜厚度 有很大的局限性。在实际使用中,通常选择控制溅射 工艺时间来控制所制备沉积薄膜厚度。具体做法是: 在一小段时间内溅射沉积某种薄膜,采用台阶仪测得 厚度值并换算成沉积速率;当制备具体厚度的该材料 薄膜时,只需简单的比例运算,就可得到沉积该厚度所 需要的时间。
在大量的实验记录中发现,通过控制溅射工艺间来控制薄膜厚度的方法也存在一定的缺陷。当溅射 靶材为铜、铝、钛、铬等金属靶材时,沉积薄膜厚度和溅 射工艺时间符合线性规律,采用溅射工艺时间控制沉 积薄膜厚度比较科学。然而,当靶材为氧化锌、二氧化 硅等导热差的材料时,随着溅射工艺时间的延长,溅射 速率在一定时间后突然增加,出现“溅射失重”现 象[10],让沉积薄膜厚度变得不再可控。为此,根据所 用设备的特点和靶材的实际导热情况以及溅射时腔内 的温度变化建立数学模型,采用Matlab软件模拟靶材 表面温度随溅射工艺时间的变化关系,阐明氧化锌、二 氧化硅靶材溅射速率突然增加的原因。
1、实验部分
磁控溅射镀膜设备为explore14多靶磁控溅射镀 膜系统,共有3个直径为3in(1in = 2.54 cm)的水冷 靶枪,配备2个直流电源和1 个射频电源。水冷靶枪 的常年温度约为25 ℃ 。靶材中心距工件台中心约为15 cm,靶平面与工件台平面的夹角约为45°。选用直 径3 in的铜、铝、氧化锌和二氧化硅靶材,靶材纯度均 为99 999% ,靶材厚度为5 mm。衬底均为4 in 清洗 干净的单面抛光硅片。所有待沉积薄膜的硅片在放置 于工件台之前,贴好十字形聚酰亚胺胶带,方便后序台阶仪测量薄膜的厚度。
1.1 铜靶材溅射
在2个直流靶上分别安装铬和铜靶材。将腔内抽 真空到0.1MPa后,对2个靶材预溅射清洗2 min。靶 材溅射清洗具体工艺条件为:工作气压0.8 pa,溅射功 率300 W。然后,对已经放置于工件台上的硅片衬底 溅射沉积薄膜。具体做法如下:先在硅片上溅射约10 nm的铬,增加铜和衬底的黏附性。溅射铬的工艺 条件为:溅射功率300 W,工作气压0.8 pa,溅射工艺 时间40 s,工件台旋转速度10 r/ min。关闭铬靶电源, 打开铜靶电源对衬底进行溅射。溅射铜的工艺条件 为:溅射功率300 W,工作气压0.8 pa,溅射工艺时间15 min,工件台旋转速度10 r/ min。溅射完毕后,取出 样品并测量厚度。更换为全新的铜靶和待沉积的硅片 样品,重复上述制备铜膜的工艺步骤,将溅射工艺时间 分别延长为30、45、60、75、90、105、120 min。需要注意 的是,为了实验的严谨性,每制备一次新样品都要更换 全新的铜靶材。在所有溅射过程中,为了防止腔内环 境温度升高,腔壁吸附的水分子释放出来影响溅射速 率,采用液氮在分子泵前端的冷阱进行制冷。制冷间 隔为每30 min加注一次液氮。
1.2 铝靶材溅
铝靶材溅射和铜靶材溅射的工艺步骤相同,溅射 前对靶材预溅射清洗2 min。铝靶材的溅射功率为300 W,工作气压为0.8 pa,工件台旋转速度时间分别为30、45、60、75、90、105、120 min。2 个直流 靶上分别安装钛和铝靶材,钛作为铝膜的黏附层每次 沉积约10nm。工艺条件为:溅射功率300 W,工作气 压0.8 pa,溅射工艺时间30 s。每制备一次新样品后 都要更换全新的铝靶材
1.3 氧化锌靶材溅射
氧化锌靶材安装在射频电源靶枪上。腔内抽真空 到0.1 mpa后,对氧化锌靶材预溅射清洗2 min。预溅 射功率为300 W,工作气压为0.8 pa。在沉积氧化锌 薄膜之前,用50 W 的负偏压功率对衬底预清洗3 min,增加薄膜和衬底的结合力。溅射氧化锌靶材的 工艺条件和溅射铜、铝靶材的工艺条件相同。每制备 一次新样品都要更换全新的氧化锌靶材。后续的系列 实验将溅射工艺时间分别设定为30、45、60、75、90、 105、120 min,制备好样品后测量厚度。
1.4 二氧化硅靶材的溅射
二氧化硅靶材的溅射工艺参数与步骤和氧化锌靶 材的完全相同,实验细节不再赘述。
2、实验结果
去掉硅片上的聚酰亚胺胶带,采用KLA-TencorP7台阶仪多次测量硅片不同位置所制备样品薄膜的厚 度,求平均值。相同溅射功率、不同溅射工艺时间下沉 积的铜、铝、氧化锌、二氧化硅薄膜具体厚度如表1 和 图1所示。
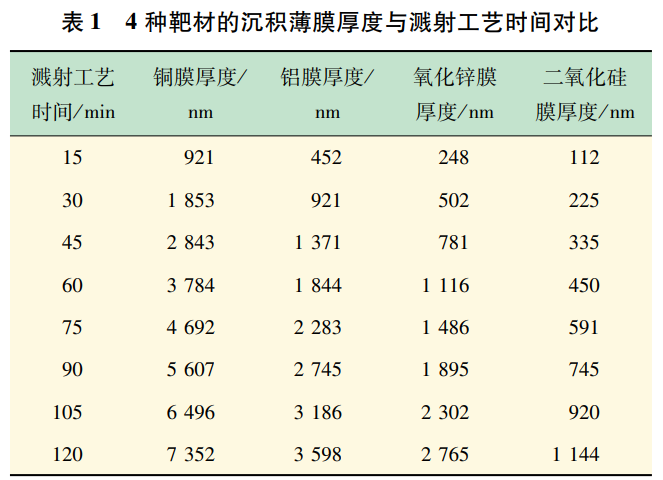
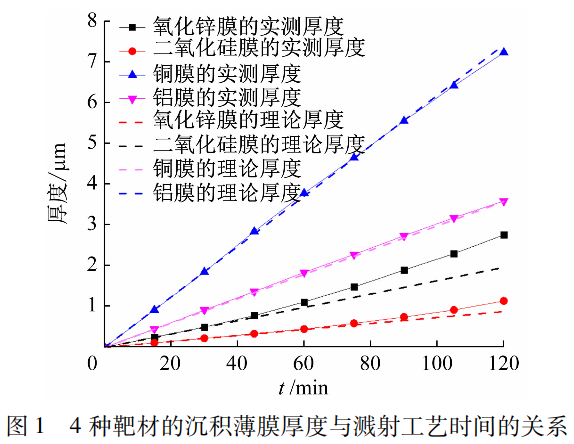
3、分析与讨论
由实验测试结果可知,铜、铝2种金属的沉积薄膜 厚度和溅射工艺时间几乎呈线性变化。在溅射工艺时 间40 ~ 80 min区间内,铜膜的实际沉积厚度比理论值 略有增加。造成这种结果的原因可能是:随着铜靶材 的消耗、刻蚀槽的加深,更多的磁场力线露出靶 面,对电子的束缚能力更强,电子与氩气碰撞产生更多
的氩离子,造成溅射产额增加,薄膜的沉积速率略快; 当溅射工艺时间超过90 min,刻蚀槽的继续加深导致 “空心阴极效应”现象的产生,加速铜膜沉积速率的降 低[11]。在溅射工艺时间60 ~ 105 min 区间内铝薄膜 沉积速率略增加,在105 ~ 120 min区间内沉积速率略 下降,这是因为铝靶的溅射速率比铜靶慢,变化趋势也 会相应延迟。
氧化锌和二氧化硅薄膜实际沉积厚度在前期与理 论值较吻合,当溅射工艺时间继续增加后,实际厚度逐 渐比理论值偏大,甚至出现了“溅射失重”的现象。这 可能是由靶材的导热性能不好、靶材表面温度过高所 造成的。根据所用溅射镀膜设备的具体特点和靶材的 导热情况尝试建立数学模型。
当靶材的溅射功率为300 W时,大约只有1%的 入射离子能量转移到逸出的溅射原子中[12]。剩下的 能量一部分消耗在靶材的表层,转化为晶格的热振动, 使靶材表面温度升高;另一部分用于氩气电离,释放的 热量以热辐射的形式对外传热。设靶材表面温度为T,当时间为t、冷水靶枪的温度恒定为25 时,温度与 时间的关系为

其中:S为实际导热面积;λ为材料的平均导热系数;h为靶材厚度;K为靶材和靶枪两界面间的传热系数;m为靶材质量;c为靶材比热容;Q为溅射时整个腔体吸 收的热量。
以铜靶材为例,在溅射过程中氩离子轰击主要集 中在刻蚀槽区域,靶材底部的实际导热面积S约为4 cm2,平均导热系数λ约为400 W/(m·K),厚度h为5 mm,K约为1 mW/(m2·K),m约为0.2kg,c约为0.4 mJ/(kg·℃ ),腔体吸收的热量Q与靶材表面的 温度存在比例关系(Q = 200T)。代入以上数据,铜靶 材表面温度与溅射工艺时间的关系为
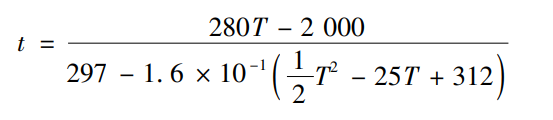
将另外3种材料的平均导热系数、靶材质量、靶材 比热容等数据代入式(1)后,用Matlab软件模拟出靶 材表面温度随溅射工艺时间的变化,如图2所示。
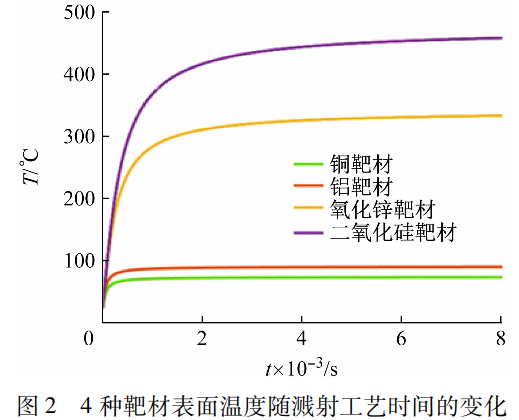
由图2模拟结果可知,对于铜、铝2 种靶材,在溅 射开始时靶材表面温度迅速升高。随着靶材表面和水 冷靶枪温差变大,热量传输更加迅速。由于铜、铝的导 热性能良好,在工艺开始的10 min后,溅射产生和导 走的热量趋于平衡,铜靶和铝靶表面温度不再升高,分 别约为75 ℃和94 ℃ 。两者均没有达到材料“溅射失 重”的临界温度,所以在整个实验中沉积薄膜厚度和 溅射工艺时间几乎是呈线性变化的。
对于氧化锌和二氧化硅2 种靶材,由于材料的导 热性能较差,加上材料温度的升高,因此导热性能随之 下降[13]。靶材表面的热量向水冷靶枪传输比较困难, 靶材表面温度不断升高。在约345 ℃和472 ℃时,氧 化锌和二氧化硅靶材表面温度趋于稳定。靶材表面温 度的升高造成材料键长增加和稳定性变差。当温度达 到某一临界值时,氩离子轰击靶材表面,更多的原子克 服材料间的键能而逸出靶面,因此出现了“溅射失重” 现象。在相同的工艺条件下,氧化锌靶材“溅射失重” 现象比二氧化硅靶材出现较早,这可能是由氧化锌的 键能约为270 kJ/ mol,而二氧化硅的键能约为799kJ/ mol[14],氧化锌靶材中氧和锌键能较低的缘故造成的。
4、结语
在使用磁控溅射镀膜设备沉积薄膜时,随着溅射 工艺时间的延长,铜、铝靶材的溅射速率变化不大,而 氧化锌、二氧化硅等靶材出现突然加速的“溅射失重” 现象。由靶材表面温度与溅射工艺时间的变化关系可 知,氧化锌和二氧化硅导热性能不良造成靶材表面温 度比铜、铝靶材表面温度高。靶材表面温度超出“溅 射失重”的临界温度,可能是氧化锌和二氧化硅靶材 溅射速率突然增加的原因。
参考文献(References):
[1] Tsekou A,Martinho F,Miakota D,et al. The effect of soft-annealing on sputtered Cu2 ZnSnS4 thin-film solar cells[J]. Applied Physics A,2022,128:970.
[2] Li Y,Wang Q. Composition control and selective infrared radiative properties of copper alloy oxides by DC reactive sputtering[J]. Journal of Physics:Conference Series,2022,2248:012008.
[3] Lin X,Zhang Y,Zhu Z,et al. Radio frequency sputtered films of copper-doped zinc telluride [J]. Chemical Physics Letters,2021, 767:138358.
[4] Augustin A,Udupa K R,Bhat K U. Characterization of DC magnetron sputtered copper thin film on aluminum touch surface[J]. Transactions of the Indian Institute of Metals,2019,72 (6 ): 1683-1685.
[5] Ylldlrlm C,Kaar E,K-sac-k ?,et al. Investigating mechanical properties of B4C films produced by magnetron sputtering PVD[J]. Solid State Sciences,2023,146:107336.
[6] 付学成,乌李瑛,权雪玲,等. Mg和V2O5 共溅射制备+ 4价钒的 氧化物薄膜[J].红外技术,2022,44(1):79-84.
[7] 焦宇泽,杜欣欣. CdTe薄膜射频磁控溅射法制备研究[J].光源 与照明,2023(8):57-59.
[8] 许 飞,朱江转,陆 慧,等.射频反应磁控溅射生长ZAO薄膜 的光电性质[J].实验室研究与探索,2019,38(11):46-50.
[9] 郝兰众,刘云杰,张亚萍,等.金属Pd掺杂对MoS2 / Si异质薄膜 微结构和光伏性能的影响[J].实验室研究与探索,2017,36(6): 13-17.
[10] 张以忱.真空镀膜技术[M].北京:冶金工业出版社,2009.
[11] 郑泽林,付学成,王 英,等.铝溅射沉积速率与刻蚀槽深度变化 关系研究[J].真空科学与技术学报,2018,38(7):610-614.
[12] 石玉龙,闫凤英.薄膜技术与薄膜材料[M].北京:化学工业出版 社,2015.
[13] 黄 昆.固体物理学[M].北京:高等教育出版社,2002.
[14] 夏玉宇. 化学实验室手册[M]. 2 版. 北京:化学工业出版 社,2015.
相关链接