汽车模具被称为“汽车工业之母” ,模具产业在很大程度上成为衡量一个汽车制造商乃至一个国家汽车产业发展水平的标志。目前中国汽车模具技术水平和能力虽然经过十几年发展,进步很快,但在世界汽车制造业中仍处于中低水平。
据相关资料介绍,大约有90%的模具并非“中国制造” ,绝大多数的中高档汽车模具依赖进口,尤其是轿车外覆盖件模具80%需要进口。
我们在完成烧结双金属滑动轴承制造技术少无切削改造的同时,也完成了世界汽车制造业中耗铜巨大并已使用T94年历史的整体铸铜汽车模具标准件的改制。为创建中国自主知识产权的自润滑汽车模具标准件的资源节约型新型制造业、再制造打下了基础。
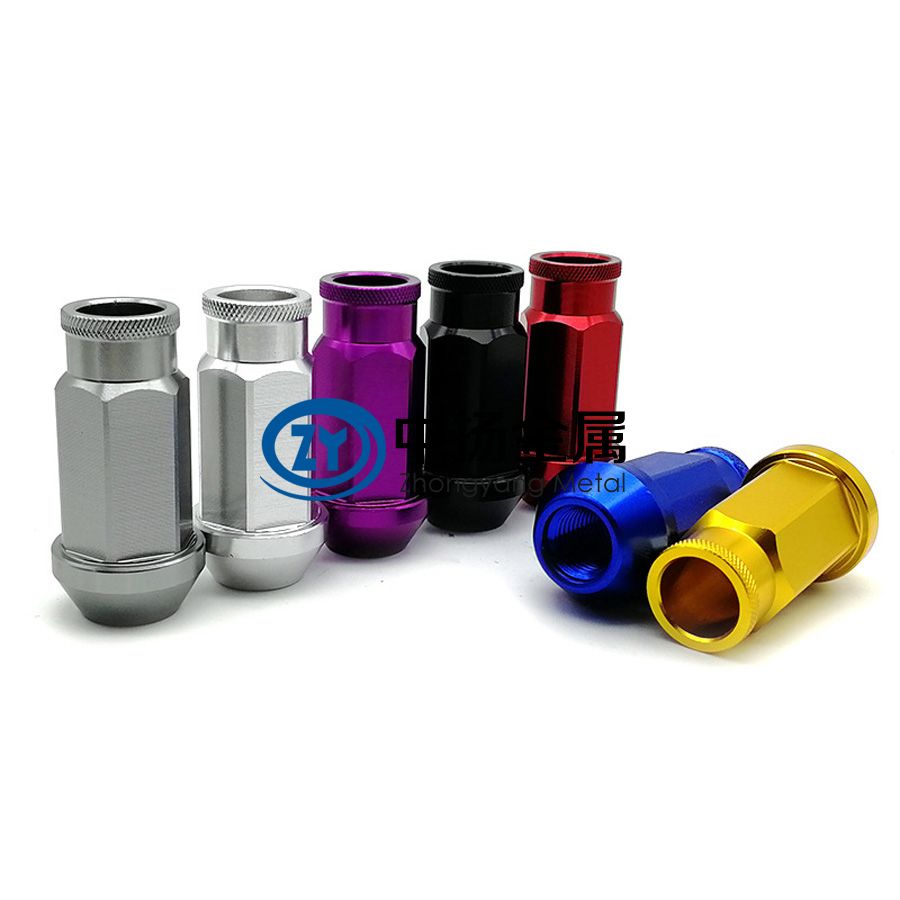
2009年,中国汽车产量达到了1379万辆,成为全球最大汽车生产国,2010年产销双超1800万辆,蝉联全球汽车产销量第一。我国的汽车模具也必将随着我国汽车工业的快速发展而发展。汽车行业的快速发展给国内模具企业带来了前所未有的挑战和机遇,如何把握机遇、紧跟汽车工业发展的步伐,是摆在国内模具工业面前一个亟待解决的问题。
国家新的汽车产业政策已经把汽车模具业列为今后几年重点鼓励和扶持发展的产业,国家颁布的整车特征(限制进口、关键零件本土生产)政策,也为模具企业增加了生产轿车外覆盖件模具的机会。
国内外现有汽车模具标准件
国内外的汽车模具标准件中,几种用量巨大的有:自润滑导向板、斜楔、凹凸v形块、L形导向板⋯⋯这类配件开始是随着我国汽车引进国,如西欧(德、意、法、荷)、东亚(日、韩)和美国以及南非等国家和地区(中国台湾)进口的,之后,国内厂家也开始试制。今后国产汽车配件要逐步国产化,这类模具配件也不会例外。这种用量十分巨大的标准配件,如果继续依照国外使用了近100年的结构研制,是不适合我国国情的。因为它是用一种日本称作高力黄铜“CuZn24A16黄铜”的整体铸造件加工成形后,再镶嵌石墨柱制成的,其加工工艺繁杂,效率低下,费材料、费工时、费设备和人力,特别是大量的耗用铜材更是我国难堪重负的。众所周知,我国是贫铜国家,铜是国内除石油之外第二位严重短缺的战略资
源,必须对耗铜如此巨大的汽车模具标准件进行技术改造、创新。
中国自主知识产权的自润滑汽车模具标准件
上述钛标准件也是滑动轴承的一种,中国自主知识产权的少无切削滑动轴承制造技术,比传统和现有的烧结双金属滑动轴承制造技术更节材、节能,使用设备及投入资金更少,经过了20余年的努力和积累,截止~2010年“汽车模具自润滑复合金属凹凸V形导板的制造方法”发明专利的授权为止,笔者采用烧结一摆辗法,完成了对近百年的烧结双金属滑动轴承(包括了汽车模具标准件)制造技术的全面改造,实现了从材料到双金属滑动轴承的近净成形制造。
最主要的标准件: 自润滑导向板、斜楔、凹凸V形块、L形导向板⋯⋯现在,我们已经完成了汽车模具标准件这类产品的制造技术及配套设备,其组成是:
(1)无油自润滑复合金属垫板,中国实用新型专利。
(2)汽车模具自润滑复合金属凹凸V形导板的制造方法,中国发明专利。
(3)专用摆辗机, 自主专有技术。为创建金属节约型、有中国自主知识产权的汽车模具标准件新产业打下了基础。
再将“双金属轴套零件材料的生产工艺及其设备”(中国发明专利)和“双金属整圆翻边轴套制造技术”(中国发明专利加专有技术),加到一起对它们进行自润滑的延伸开发,就将全面完成“中国自主知识产权的自润滑汽车模具标准件新产业”的创建。
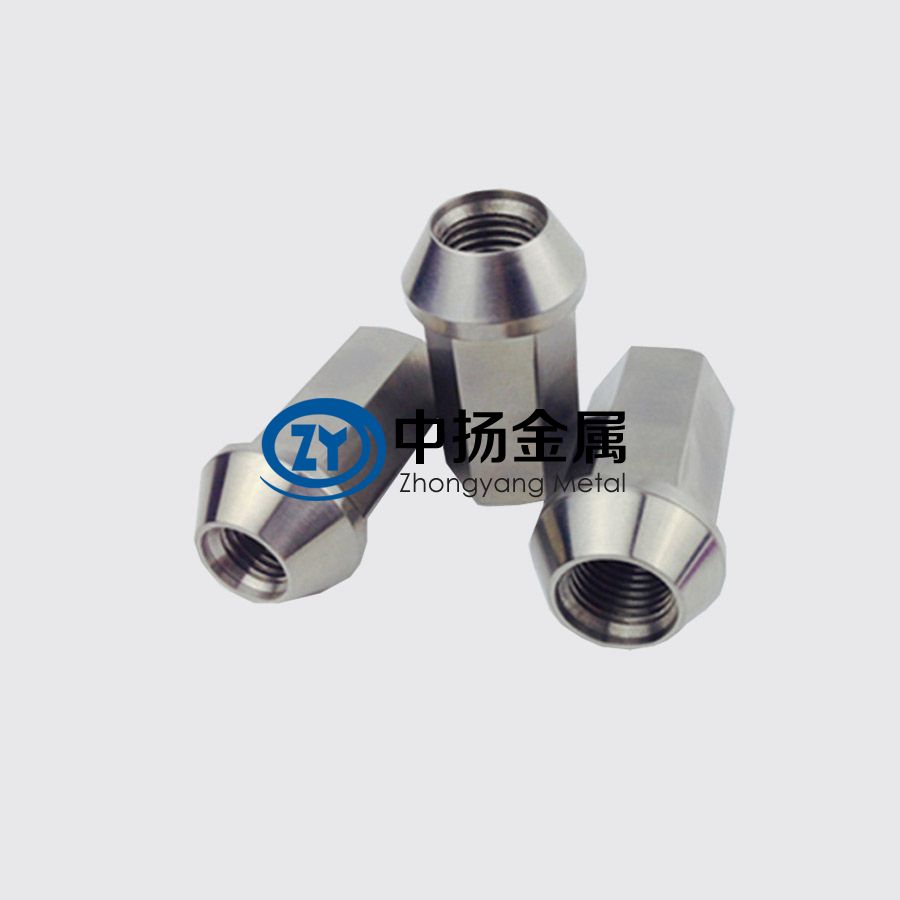
发展中国复合金属汽车模具标准件的再制造产业
再制造,是将旧的复合金属汽车模具标准件,用先进的技术手段进行专业化修复,使其恢复到与原有新品一样的质量和性能的批量化制造过程。再制造是循环经济3R原则(“减量化、再使用、再制造”)当中的再使用的高级形式。
再制造在中国的发展处于起步阶段,汽车零部件就在试点范围之内。
中国自主知识产权的汽车模具标准件,在工况运行中主要损耗是其薄壁减摩耐磨层(平均厚度为0.20mm),目前,经试运行的寿命已超过40万模次(标准要求一般为20万模次),其他组分,厚衬背钢层损耗量甚微,有着充分再制造的条件。
再制造产品,它的原材料就是来源于使用过的模具标准件,与新品相比,可以节约成本50%,节能60%,节约原材料70%。
有了中国复合金属模具标准件新产业,就开启了中国汽车模具标准件的再制造产业。有双金属滑动轴承近净形成形制造设备,就可以完成复合金属模具标准件的修复。
新型模具标准件的实施试样照片见图1和图2。
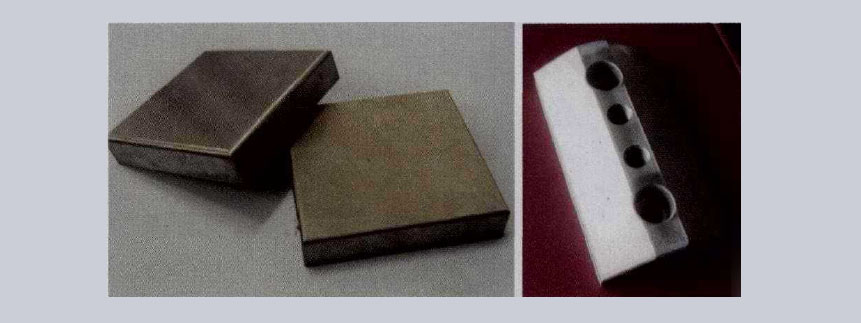
图1双金属自润滑导向板 图2双金属自润滑凹凸V形凸块
结语
(1)这是发展中国复合金属汽车模具标准件和其再制造产业的一种模式,也是业内的发展方向。
(2)中国汽车模具标准件新产业和汽车模具标准件再造业,将为做大中国的汽车制造业打下坚实的基础。
(3)该技术紧跟了国家制造业发展步伐,产业化后,将为建设资源节约型社会做出一定的贡献。
相关链接