很多人并不了解钛,尤其是钛在建筑领域的应用及开发。 实则,在建筑领域,钛已经被广泛用于制造屋顶、幕墙、外壁等建筑材料,以及艺术雕塑、纪念 碑等装饰品。 近年来,钛在建筑领域的应用发展速度加快,除了国家大剧院的穹顶等使用了钛材以外,在广 州、深圳也出现了用钛装饰的民居,彩色钛冰花款式的房屋装饰也应运而生,丰富了钛在建筑领域 的应用场景。 这是记者近日从由中国有色金属工业协会钛锆分会、独联体国际钛协会等单位指导,西北有色 金属研究院和宝钛集团有限公司主办的首届中国—独联体钛工业发展论坛上了解到的。 “钛在建筑领域的应用已经越来越广泛,其优异的性能和环保节能的特点也为建筑行业带来 了更多的选择。”奥雅丽固新技术(广东)有限公司总经理李谏接受本报记者采访时表示。由此可见,未来,建筑领域钛产业的发展路径已逐渐明晰。 钛在建筑领域应用场景持续丰富 钛产业是推动尖端科技发展和国民经济增长的关键原材料产业,在国家重点项目建设、经济及科技发展中具有不可或缺的重要地位。钛产业发展水平是一个国家综合实力的重要标志,钛以其轻 质、高强度、耐腐蚀等独特优势,在航空、航天、建筑等多个领域发挥着关键作用。
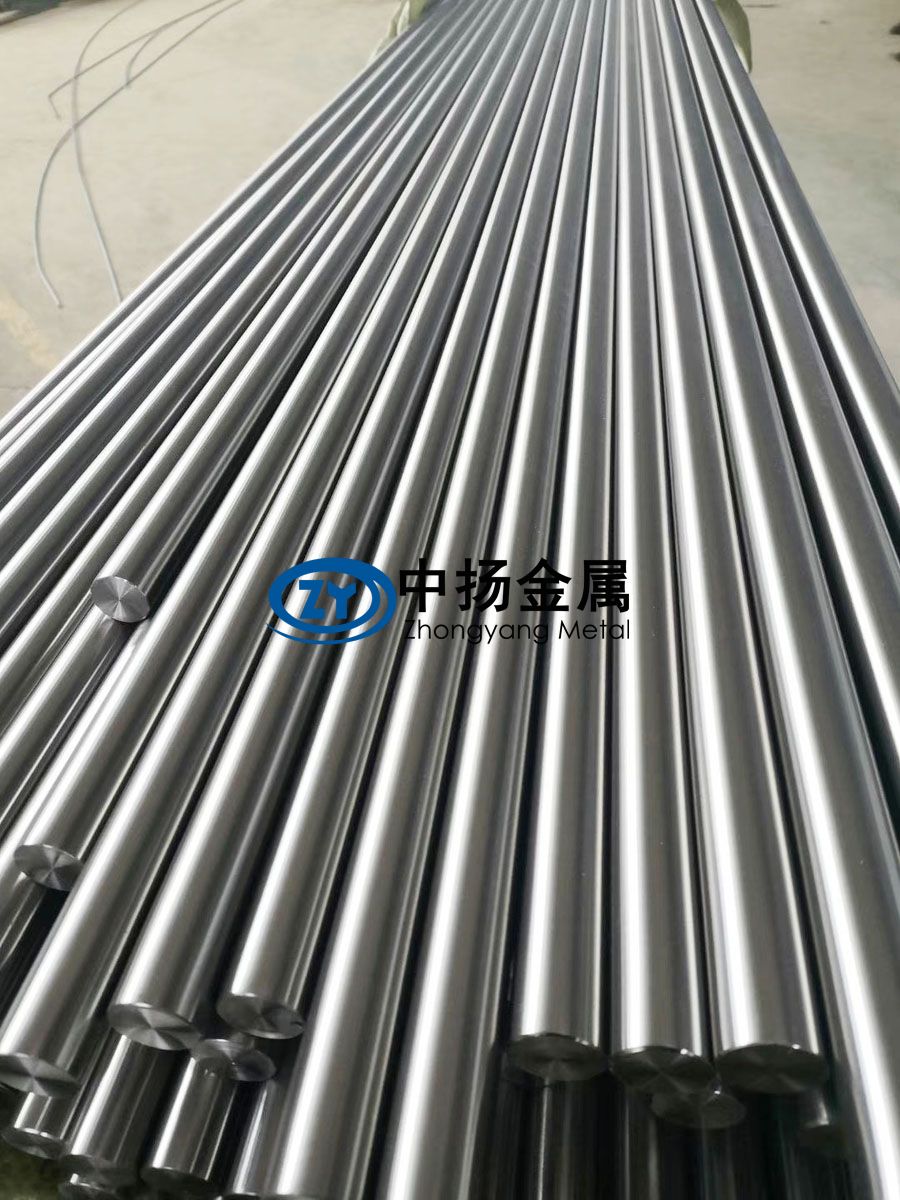
近年来,中国钛产业坚持创新驱动发展战略,不断推动技术创新和产业升级,不断优化产业结构,加强产业链上下游协同,提升产品质量与生产效率,推动了钛在传统产业及战略性新兴产业的拓展 应用,并深耕个性化、大众化、多样化应用场景。 据记者了解,钛在建筑上的应用,始于 1973 年日本大分县佐贺关町的早吸日女神社金黄色屋顶,英国、法国、美国等也均有建筑使用钛合金作屋顶的范例。除屋顶外,建筑外壁、幕墙、封檐板,天棚,港湾设施,桥梁,海底隧道,装饰物,管道等也应用了钛合金。 在中国,钛在建筑领域的应用也不乏案例。国家大剧院壳体由 18000 多块钛金属板拼接而成,面积超过 30000 平方米,钛金属板经过特殊氧化处理,其表面金属光泽极具质感,且 100 年不变色。 除此之外,杭州大剧院、合肥大剧院、宁波中国港口博物馆等的幕墙也都应用了钛合金。 钛在建筑领域极具潜力和优势 随着时代的进步,人们对城市建筑物的要求,尤其对建筑物的美观性要求越来越高。伴随建筑 工业的发展,近年来建筑师追求使用比传统材料更高级的建筑材料。钛的一系列优异特性能完全满 足建筑材料的许多性能要求,因而倍受建筑师及建筑业的青睐。
钛合金具有优异的耐腐蚀性和高温性能,可以抵御酸雨和紫外线的侵蚀,因此在建筑外墙装饰 中有着广泛的应用。钛合金外墙板材不仅美观大方,而且寿命长,减少了维护成本。 在用作建筑屋顶材料时,钛具有轻质高强度的特点,可以为建筑提供更好的支撑,同时也可以减 轻建筑的重量,降低建筑的负荷。因此,钛在建筑屋顶材料中有着广泛的应用。
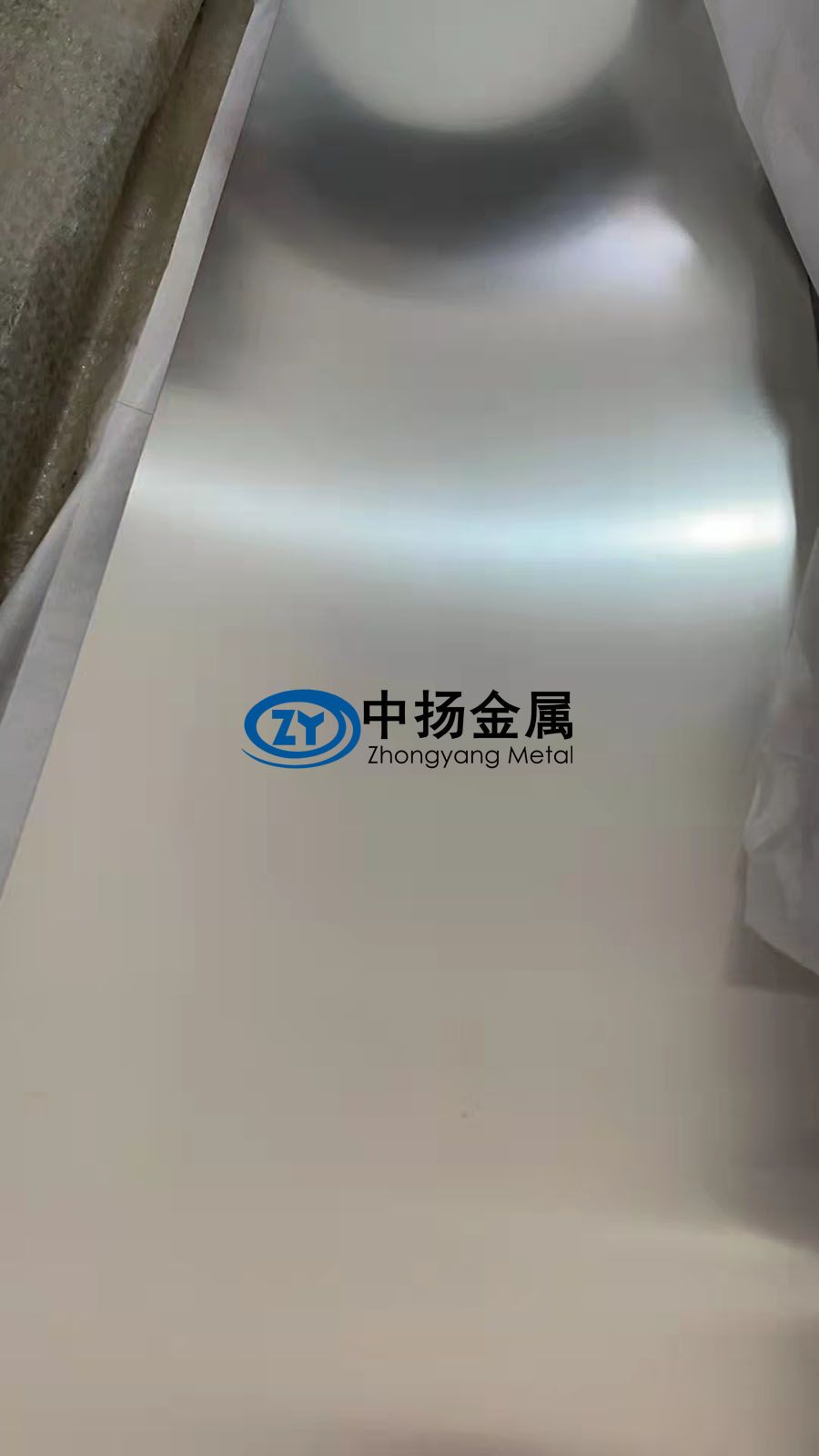
同时,钛具有独特的金属光泽和色彩,也可以用作室内装饰材料,为室内装饰提供更多的选择。 另外,钛也可以用于制作室内家具和装饰物品,使室内环境更加美观。 与会专家也特别强调,钛合金的防腐蚀性非常出色,这主要得益于其在空气中或氧化性、中性水溶液中能够迅速生成一层稳定的氧化性保护膜。即使这层保护膜遭到破坏,也能迅速自动恢复,因此在氧化性、中性介质中具有优异的耐腐蚀性。特别是在我国,由于海岸线漫长,海滨城市面积 大,建筑用钛的潜力巨大。 钛在建筑领域新图景已描绘 近年来,中国钛产业呈现出稳步增长并持续优化的态势,各类主要产品产量与需求量连创新 高。2023 年,中国钛矿产量达到 324.7 万吨,占全球总产量的 37%;海绵钛产量达到 21.8 万吨,占全球 总产量的 63%;钛材产量 15.9 万吨,占全球总产量的 64%;钛材消费量 14.8 万吨,占全球总消费量的59%。 目前世界上有 600 多栋钛的标志性建筑,对于钛在建筑领域的发展,未来的应用前景是非常广 阔的。钛以其独特的性能优势,正在逐渐改变建筑行业的材料选择和设计理念。
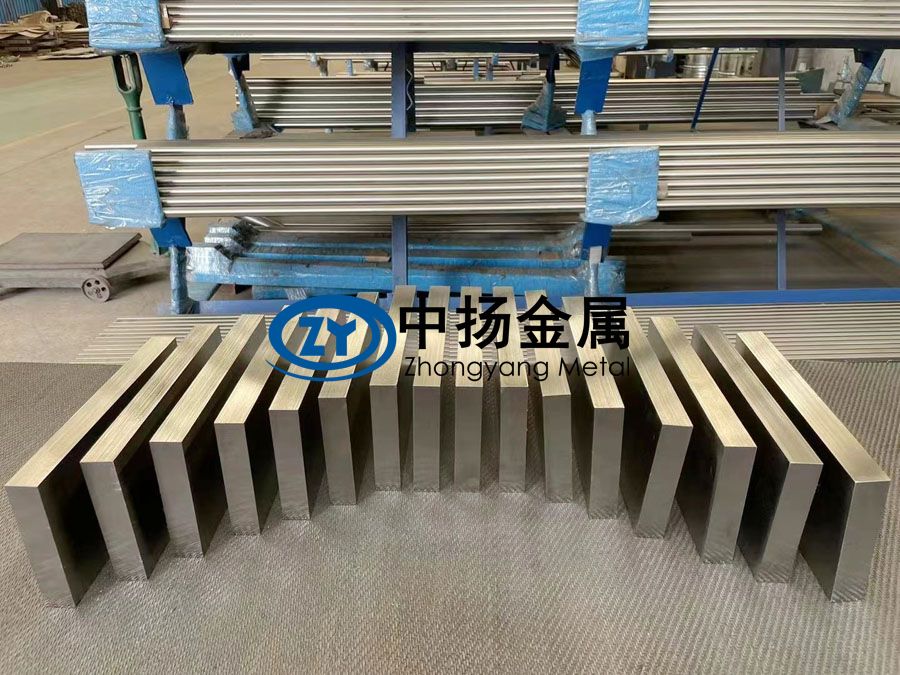
“随着新材料产业的发展,政府对新材料产业的支持也在不断增加。钛合金的环保特性和优异 性能,使其成为绿色建筑和可持续发展建筑的理想材料,有助于推动建筑业向更加环保和可持续的 方向发展。”李谏对记者说,这也为钛在建筑领域的应用提供了政策上的支持和市场动力。 不难看出,政府对节能减排工作的重视,以及市场对绿色建筑材料的需求增加,推动了钛在建筑 领域的应用。例如,推广绿色低碳建材和绿色建造方式,加快推进新型建筑工业化,大力发展装配式 建筑,推广钢结构住宅,推动建材循环利用等。通过这些方式,钛在建筑领域的应用将更加有助于实 现节能减排,推动建筑业的可持续发展。
相关链接