1、前言
在振动激励条件下,受外界循环剪切载荷作用螺栓连接状态会发生变化,不仅会影响结构的正常功能,甚至会造成严重后果。因此,螺栓连接结构力学性能对电池包连接可靠、结构完好等性能的影响不容忽视。某新能源汽车电池在进行 Z向振动测试试验进行到约 12 h 时产生异响,拆解检查发现其中用于模组固定的一颗螺栓完全断裂,造成振动时异响。该断裂螺栓使用的材料为SCM435 铬钼型合金结构钢,螺栓型号为 M8×96mm,强度等级为 10.9 级。通过理化检验、装配工艺分析和振动测试情况分析多种手段,对该新能源电池模组固定螺栓断裂失效的原因进行了调查分析,便于制定相应的措施避免后期类似事故再次发生。
2、理化检验
2.1宏观形貌分析
通过对断裂失效螺栓的断口进行宏观检查,螺栓断口宏观形貌如图 1 所示,断口的疲劳扩展区面积分别约占整个断口面积的 95%,断裂部位没有明显的宏观塑性变形痕迹,断裂起源于螺栓电池箱体非标螺套啮合的第一个螺牙的牙底处。断口起始区和扩展区局部磨损发亮,裂纹起始区隐约可见贝纹线,扩展区平整光滑,最终断裂区存在较小区域的剪切唇。
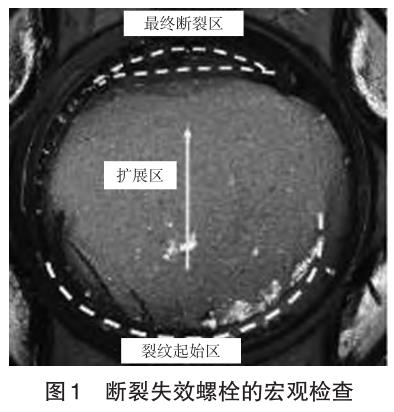
2.2材质成分分析
采用德国斯派克台式直读光谱仪 SPECTRO⁃MAXx 07 对断裂失效螺栓的材质进行初步检测分析,检测分析结果如表 1 所示。由表 1 可见,断裂螺栓的材质符合 SCM435 的 JIS G 4053—2016《机械结构用低合金钢》标准。

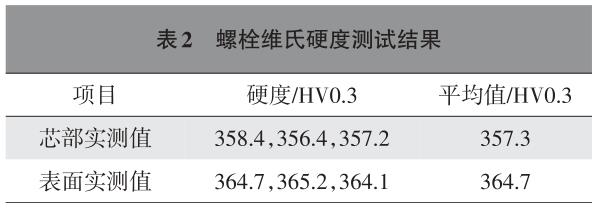
2.3力学性能测试分析
采用 司特尔 DuraScan 50 维氏硬度计对断裂失效螺栓取样进行维氏硬度测试,测试结果如表2 所示。根据 GB/T 1172—1999《黑色金属硬度及强度换算值》可得螺栓的抗拉强度为 1 148 MPa,另外根据 GB/T 3098.1—2010《紧固件机械性能 螺栓、螺钉和螺柱》表 3 要求,螺栓的维氏硬度应在320~380 HV0.3,表面硬度不应比芯部硬度高出30 个维氏硬度值,10.9 级的表面硬度不应大于390 HV0.3,抗拉强度应在 1 040~1 220 MPa。可得知该断裂失效螺栓的硬度和抗拉强度均符合制造标准要求。
2.4螺纹牙型尺寸检测分析
螺栓受力时,螺纹沟槽处容易产生应力集中,其值在很大程度上取决于螺纹沟槽的形状。一般而言,螺纹的沟槽越平滑,应力集中就会越小,疲劳强度则越高。为确认断裂失效螺栓牙型尺寸对疲劳特性的影响,采用影像测量仪VMS-5040MZ对其牙型尺寸进行测量,测量结果如图 2 所示,牙型角为60.899 5°,螺牙底槽R角半径为 0.205 1 mm,符合米制普通螺纹牙型角2α=60°(α表示牙型半角)和底槽R 角半径大于 0.125 P(P 为 1.25 mm)的要求,可见断裂失效螺栓的牙型尺寸符合制造标准要求。

2.5断口扫描电镜检验分析
为弄清该螺栓断裂失效的机理,将其断口物理清洗后置于蔡司 Gemini SEM 460 扫描电镜下观察,如图 3~图 5 所示,可见断口起始区存在磨损现象,且微观形貌主要时疲劳特征,未见明显加工缺陷。扩展区的微观断口形貌主要是疲劳特征,最终断裂区的微观断口形貌主要为韧窝。
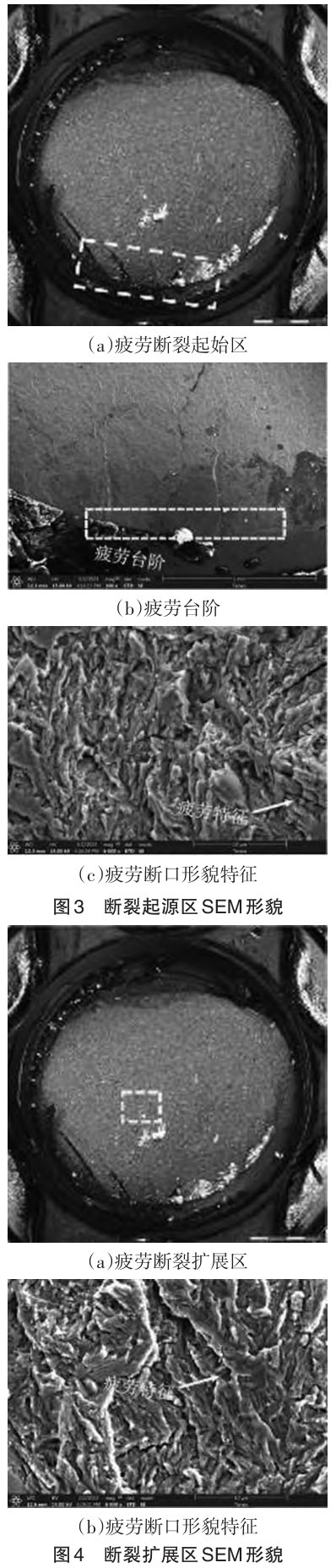
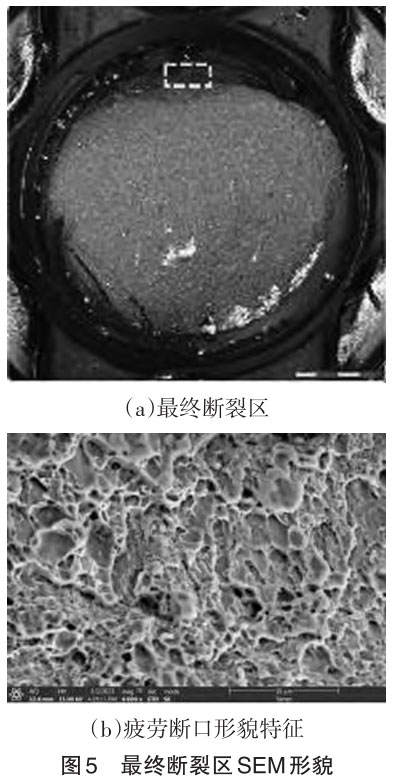
2.6金相检验
将断裂失效螺栓沿轴向剖开并制备金相试样,采用蔡司 Axio Imager.M2m 金相显微镜对断裂失效螺栓的裂纹区断面显微组织进行观察。试样在抛光状态(未侵蚀)时,可见断裂部位没有明显的宏观塑性变形痕迹,断裂起源于螺牙沟槽部位,而后沿剪切面向螺杆中心部位继续扩展至最终断裂,且裂纹起始区及其扩展区断面较为平整(图6a)。金相显微镜同时检测到螺杆上很多螺纹中经和沟槽处呈锯齿状形态的表面裂纹,裂纹的尾部长短不一,且较尖细(图 6b)。
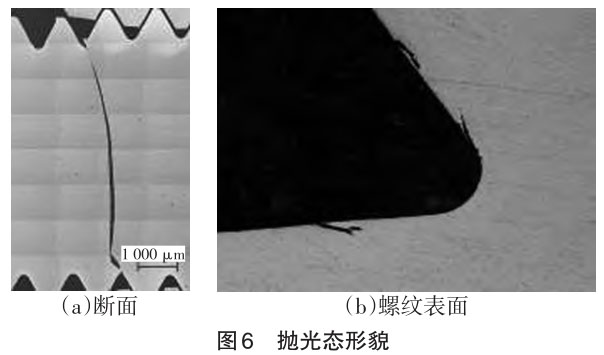
将上述抛光状态试样用 4%的硝酸酒精腐蚀后在蔡司 Axio Imager.M2m 金相显微镜下观察,发现螺纹表面和裂纹周围无脱碳,尾端尖细,应为疲劳扩展裂纹,表面裂纹的纵深度及垂直深度在 55~143 μm 之间(图 7a~7b)。在显微镜下放大 500 倍可见其芯部组织均为针状马氏体位向的回火索氏体+铁素体(图 7c),参照国家标准 GB/T 13320—2007《钢质模锻件 金相组织评级图及评定方法》评级图3进行评定,调质处理的显微组织评定为2级,标准要求1~4级合格,该显微组织属于合格级别。
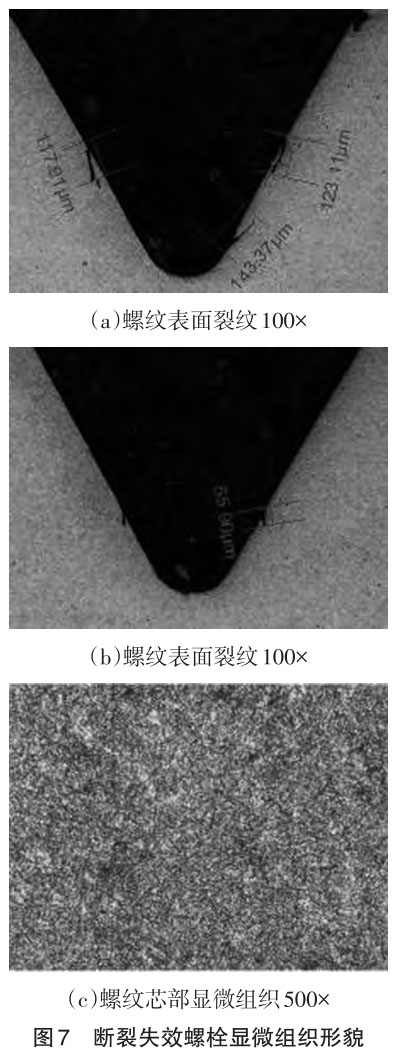
2.7小结
通过对断裂失效螺栓进行断口宏观形貌检验、材质成分分析、力学性能测试和断口扫描电镜检验分析等多种手段的调查,研究结果表明该新能源电池模组固定螺栓的各项性能参数均符合GB/T 3098.1—2010《紧固件机械性能 螺栓、螺钉和螺柱》的要求,由此判定该螺栓断裂失效不是由其本身的制造质量引起的。
3、装配工艺分析
导致螺栓疲劳断裂失效的原因大致有三个方面。
a.螺栓本身存在制造缺陷,如材质不合格、制造缺陷、热处理不当等,在进行 Z 向振动激励下使缺陷成为疲劳源,最终导致断裂;
b.螺栓装配工艺问题,如配合状态问题或螺栓预紧工艺不良等原因,使螺栓在高频振动环境下松动或过载引起疲劳断裂;
c.螺栓连接设计问题,如未充分考虑零部件的承受载荷、安全标准等因素。前面理化检验结果表明,该新能源电池模组固定断裂失效螺栓的制造质量没有问题,因此排除了第一方面的因素。
3.1装配工艺影响分析
为了查找螺栓断裂的原因,对影响电池模组固定螺栓断裂失效的配合关系进行了全面的调查分析,该螺栓断裂部位处于螺纹中部的电池箱体非标螺套锁紧位置(见图 8a),即疲劳断裂位置是螺栓电池箱体非标螺套啮合的第一个螺牙的牙底处。另外,电池模组安装凸台非标螺套承台面处有磨损痕迹(见图 8b),说明在进行 Z 向振动时螺栓连接受外界循环剪切载荷作用发生的自松弛,导致电池模组端板与非标螺套承台面发生振动磨损。同时,在对电池模组检查发现其端板与非标螺套承台面接触的位置也有磨损现象,端板螺栓安装孔边缘还有丝牙痕迹(图 8c)。可见,断裂失效螺栓与电池模组端板存在过盈配合现象,螺栓在拧紧的过程中,螺纹受较大副摩擦力的作用容易在螺纹表面萌生显微裂纹成为疲劳源。疲劳源形成后,在进行 Z向振动时显微裂纹在交变应力作用下不断扩展,直至最终断裂。
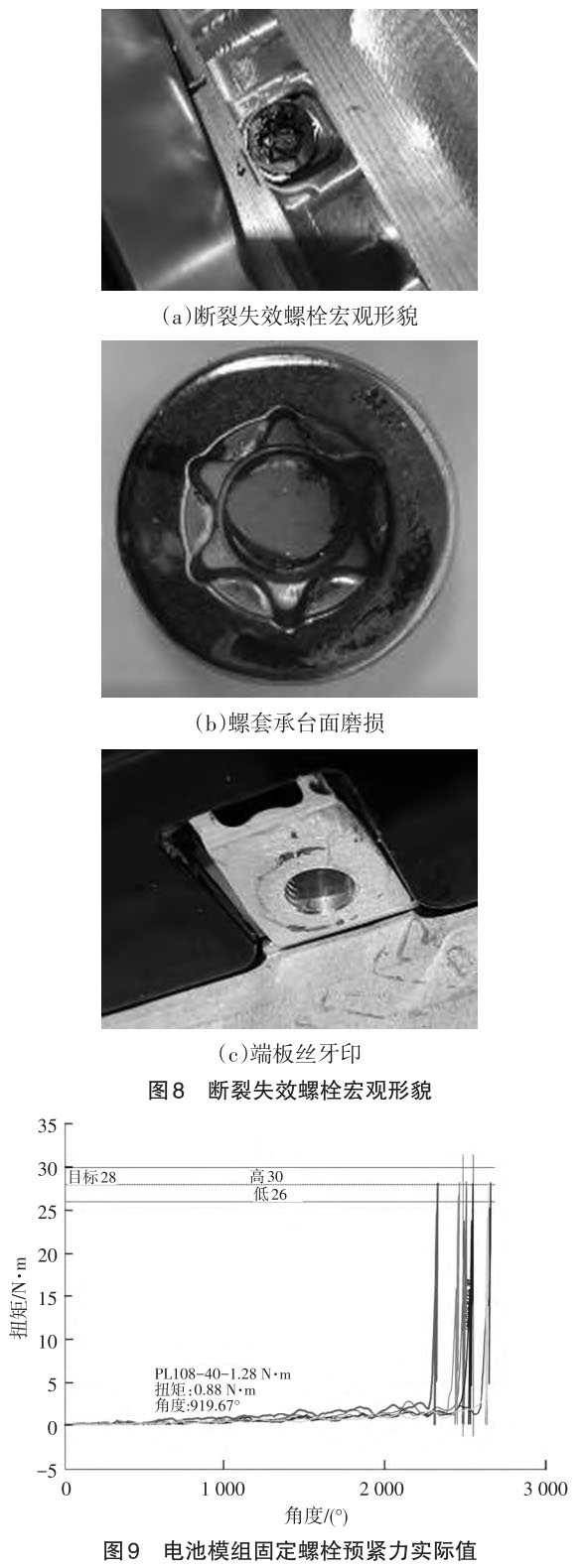
3.2振动前后扭矩值的测量分析
螺栓预紧力的存在,除了使零件之间产生紧密联接,增强联接的刚性之外,还会大幅度降低在拉伸载荷作用下螺杆应力的变化幅度,由此提高了螺栓联接的疲劳强度[1]。在众多的案例中,将螺栓紧固到设计预紧力是提高螺栓副疲劳寿命的有效手段。为此,调取该断裂失效螺栓所在电池模组的全部固定螺栓的实际装配预紧力扭矩数据,如图 9 所示。从图 9 可以看出,实际装配预紧力扭矩均符合工艺参数(28±2)N·m 的设计要求。
在进行 Z向振动测试试验进行到约 12 h 后,对故障电池模组固定螺栓的残余扭矩进行测量,测量结果如表 3 所示。由表 1 可见,故障电池模组固定螺栓在高频振动的作用下扭矩衰减并不明显,且残余扭矩均大于 60%(工艺设计参数要求为(28±2)N·m,满足要求。
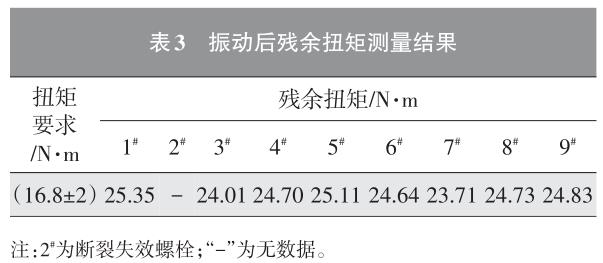
3.3电池箱体模组安装底座平面度对螺栓断裂的影响
如图 10 所示,电池模组由电池箱体上的 9 个固定安装底座平衡支撑,有研究表明,螺栓过早疲劳断裂原因之一是被接触面不平整,因此安装底座的平面度是一项重要的质量指标。从 S-N 曲线(疲劳曲线)可以发现应力幅值越大,允许的循环次数越小,也就是说在这种工况下材料的疲劳寿命越短。该新能源汽车电池模组固定螺栓在振动试验过程中主要承受高周变幅荷载的作用,在整个试验周期中,理论上模组固定螺栓所承受的应力循环次数是固定的,要想增加螺栓的疲劳寿命,只有尽可能减小循环应力幅值,即尽可能保证模组安装底座的平面度满足设计要求。分析螺栓在螺栓连接中的受力情况,螺栓拧紧后,电池模组被夹紧并产生微小的变形,如果电池模组和安装底座之间的结合面处有间隙,螺栓连接中电池模组的整体刚度就会受到影响,刚度比没有间隙的情况要小很多,当承受外部交变疲劳载荷作用时,电池模组的变形幅度也相对比较大,进而导致该部位的螺栓受到的交变应力幅值就比较大。因此,电池箱体模组安装底座的平面度也是影响螺栓断裂的重要因素。
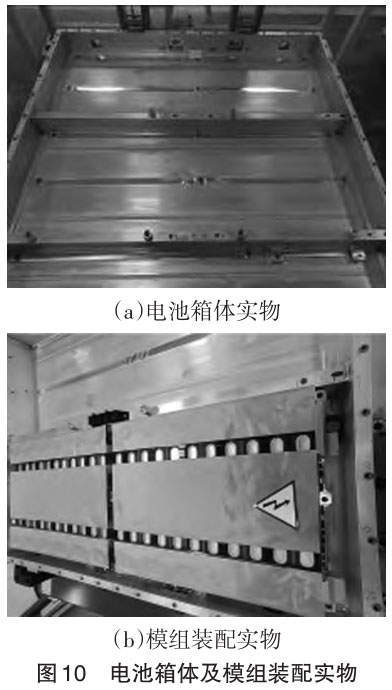
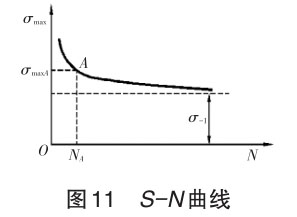
为确认电池箱体模组安装底座平面度对螺栓断裂失效的影响,采用力德三坐标测量仪 GREAT251510 对电池箱体模组安装底座平面度进行测量,测量结果如图 12 所示,可见电池箱体模组安装底座平面度符合设计要求。

3.4螺栓连接设计对其断裂失效的影响
螺栓在实际应用过程中,疲劳断裂是常见失效模式之一。一般螺栓连接的疲劳断裂发生在交变载荷力的作用下,特别是在交变载荷幅值高和频次高的环境中,螺栓连接更易发生疲劳失效[2],因此在设计螺栓连接时需要对其疲劳强度进行评估。
利用有限元软件 OptiStruct 分析评估该电池箱体底部螺纹连接副疲劳强度,根据新能源汽车电池实车装配状态,将振动激励施加于吊耳处,在 Z向振动激励下,应力分布主要集中在底板的螺栓安装孔附近,如图 13 所示。因此,振动环境下螺栓的疲劳强度性能成为评估新能源电池结构振动安全性不容忽视的重要指标。通过对该电池包进行模态分析和随机振动分析,振动外载荷分布(保守)和振动外载荷分布(激进)状态下需要的疲劳强度分别是 59.032 MPa 和 47.453 MPa,而 M8 紧固件基于 VDI2230 的参考疲劳强度为 59.5 MPa。由此可见,振动最大外载荷即便全部加载在紧固件上也可满足要求。
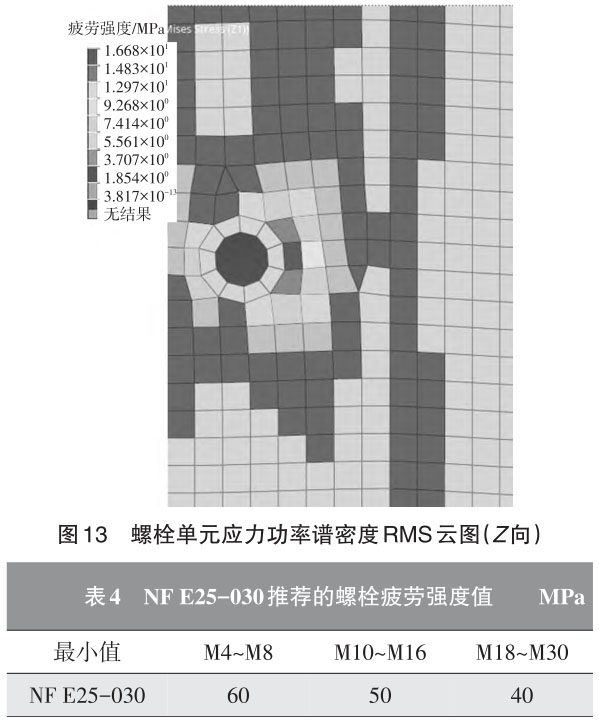
NF E25-030 又给出了高强螺栓的许用动态应力,该推荐值对应的存活率为 99%,置信度为 95%,平均应力为 0.3~1.0 倍的屈服强度,循环次数为3.0×106次。其值如表 4 所示。由此可见,即便振动最大外载荷即便全部加载在紧固件上,该新能源汽车电池模组固定螺栓的疲劳强度仍低于推荐的螺栓疲劳强度值。
4、测试情况分析
参考标准GB 38031—2020《电动汽车用动力蓄电池安全要求》进行随机振动试验。将该新能源汽车电池包通过夹具固定在振动台上,电池包和夹具的固定方式、螺栓规格和实车装配保持一致。控制点传感器布置在夹具与固定电池包的螺栓附近,采用 4 个对角位置的传感器的进行算术平均值控制,功能检查正常后在 Z 向施加随机和定频振动载荷,随机振动功率谱密度见图 14。在随机振动前后进行扫频试验,以测试样品的固有频率,扫频频率 5~200 Hz,振 动 加 速 度 0.5 g,扫 描 速 度1.0 Oct/min。Z 方向振动前后的扫描数据见图 15,由图可见 Z 方向振动前一阶固有频率是70.20 Hz,振动后的一阶固有频率是 68.95 Hz,试验前后主频衰减率为1.78%,变化并不大,说明振动系统的稳定性很好,可见螺栓断裂失效的原因并非是振动设备和振动试验过程中异常导致的。
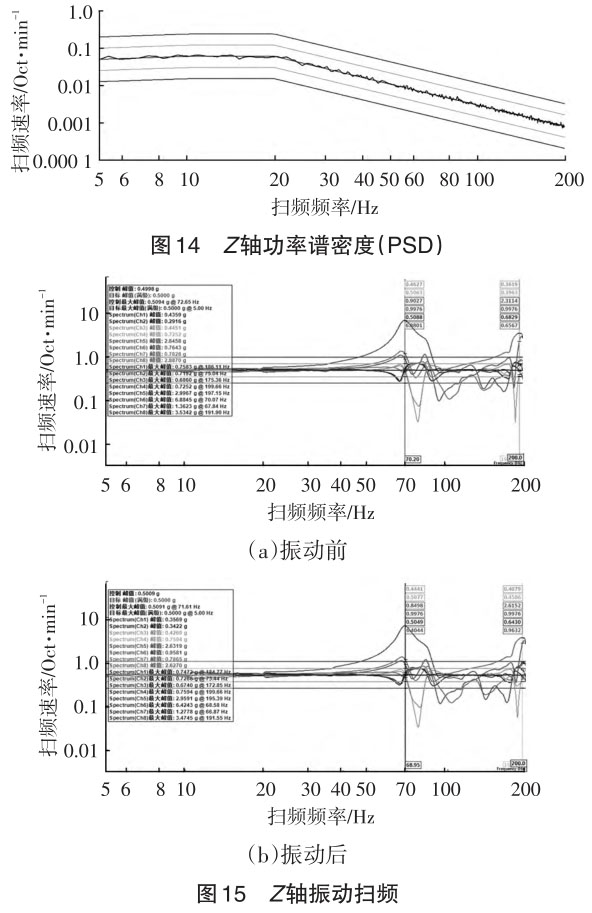
5、结论与建议
该新能源汽车电池模组固定螺栓断裂形式为单向疲劳断裂,断裂的原因是螺栓装配不当。断裂失效螺栓与电池模组端板存在过盈配合情况,螺栓在拧紧的过程中,螺纹受较大副摩擦力的作用在螺纹表面萌生显微裂纹成为疲劳源。疲劳源形成后,在进行 Z向振动时显微裂纹在交变应力和失效螺栓的上下结合面处螺栓受径向剪切力的共同作用下不断扩展,最终导致断裂。建议增加电池模组孔位导正动作,用导向杠使电池模组固定孔与电池箱体非标螺套螺纹孔对正后再安装螺栓紧固。
参考文献:
[1] 郭卫凡,唐文良. 螺栓联接的预紧力与疲劳强度的讨论[J].科技视界,2013(23):65-66.
[2] 余幼民. 螺栓联接的疲劳破坏及改善措施 [J]. 海南矿冶,2001(3):5-8.
相关链接