汽车接地紧固件是汽车电气系统中不可或缺的一部分,其作用是将电气设备的外露导电部分及装置外导电部分通过导电线束与车身连接起来,形成一个良好的接地回路,如图1所示。本文旨在介绍3种常用的接地紧固件,分别对其结构、应用场景进行分析说明。

随着新能源汽车的发展以及对整车轻量化目标的不断挑战,铝合金等车身材料应用越来越广泛,新型接地紧固件的应用推广显得尤为重要。
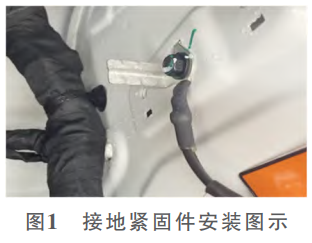
1、汽车用接地紧固件的作用与重要性
1.1提高车辆的安全性能
汽车上电气设备及装置的导电线束虽然看起来比电源线少得多,但却占据着重要地位,因为汽车是运动的交通工具,特别是各种条件恶劣的颠簸工况,以及外部环境对汽车整车及外露零部件的侵蚀,通常容易出现搭铁不良或者线路断路的情况,轻则影响汽车某方面的功能,重则使汽车瘫痪[1]。
接地紧固件分布在汽车全身,主要集中在仪表板管梁、车身底板、前机舱等部位,有些接地部位容易沾泥水﹑油污或生锈,这些情况都可能引起搭铁不良,从而出现功能故障。例如搭铁点处的车身上有漆、发动机搭铁线紧固件松动等,这些都会导致搭铁不良,严重影响用电器的正常工作。
1.2减少电磁干扰
汽车上一些小电流信号(如模拟信号、数字信号等),信号一般比较敏感,容易被干扰。对于娱乐系统天线及高电压工作用电器,由于其工作过程中对周围电磁场影响较大,必须采用接地导线,以达到保证接收信号准确,且对周围线束电磁场影响最小的作用,例如发动机点火线圈供电回路。针对这些位置,采用接地紧固件能够很好地解决应用问题[1]。
1.3满足法规要求
汽车用接地紧固件是保障汽车安全运行的重要部件,其作用是安全可靠地固定接地线束,将车辆各个部分与大地相连,形成一个良好的接地系统。无论是美国法规要求《美国联邦机动车辆安全标准FMVSS609》、欧盟法规要求《欧洲经济委员会ECER100》,还是中国法规要求《机动车运行安全技术条件GB7258—2017》《机械电气安全机械电气设备第1部分通用技术条件GB/T5226.1—2019》等,这些标准都对汽车接地紧固件提出了各种性能要求,目的就是最大程度保证汽车安全。
总体而言,不同国家和地区可能有不同的汽车接地紧固件法规要求,因此,在设计和制造汽车接地紧固件时,需要了解并符合相应地区的法规标准。
2、不同类型的汽车用接地紧固件及其特点
常用的接地紧固件有刮漆螺栓、组合式螺栓、自攻螺栓3种。其各有特点,工程师根据设计需求、应用环境和成本因素等维度综合评估进行设计选型。
2.1刮漆螺栓
刮漆螺栓的螺纹末端设计了若干个刮漆槽,刮漆槽的数量主要根据螺栓的螺纹规格来确定,例如M6规格的螺栓一般设计1个刮漆槽。在螺纹杆部有一组对称的压痕。
这两个结构特征是刮漆螺栓接地功能实现的关键[2]。刮漆螺栓在拧紧的过程中,依靠螺纹末端刮漆槽刮除车身焊接螺母内螺纹上的电泳漆层,电泳漆残渣顺着焊接螺母内螺纹孔脱落,如果内螺纹是盲孔,则需要设计出足够长的深度余量,用于容纳刮除的电泳漆残渣。螺纹杆部对称的一组压痕位置根据实际装配环境进行设计,一般应处于内外螺纹啮合位置,在螺栓拧紧后,压痕部位螺纹因为变形,与内螺纹产生过盈配合,具有一定的锁紧作用。
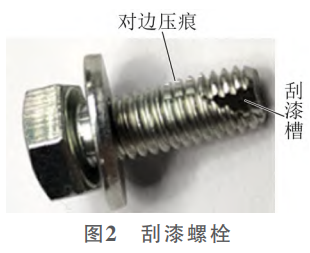
刮漆螺栓如图2所示,结构为六角头螺栓和平垫圈组合件,表面处理为电镀锌。通常为了保证良好的导电性能,电镀表面处理不涂封闭剂。
2.2组合式螺栓
组合式接地紧固件供货状态为螺栓和螺母组合起来一起送到生产线,直接焊接到白车身上。然后随白车身经过电泳、油漆,在总装车间,紧固搭铁端子时,先将螺母拧出,固定好端子,再拧紧螺母。
在涂装车间经过电泳、油漆工艺时,螺母与螺栓螺纹啮合部位无电泳液和油漆浸入,保证了良好的导电接触。
需要注意的是,螺母端面与螺栓端面要保证完全贴合,避免涂装过程中两个端面间浸入异物,造成导电不良。
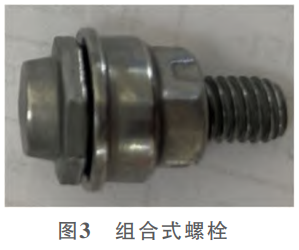
组合式螺栓如图3所示,在焊接前,螺栓和螺母通过规定扭矩工艺组装在一起。表面处理为电镀锌镍合金本色钝化,防腐性能较高。
2.3自攻螺栓
自攻螺栓的螺纹杆呈三棱形,螺栓末端自攻螺纹区经过感应淬火,表面硬度非常高。同时在自攻螺纹区有若干个斜置的刮漆槽,斜置刮漆槽的数量主要根据螺栓的螺纹规格来确定,例如M6规格的螺栓一般设计4个刮漆槽。
自攻螺栓在拧紧的过程中,自攻螺纹区硬度高于被连接件,被连接件的配合孔被挤压形成相应的螺纹,紧固过程中基本没有金属碎屑产生,但是斜置刮漆槽会将经过涂装的车身油漆清除掉,从而实现接触导电功能。自攻螺栓(图4)按照规定扭矩拧入对配件中,表面处理为电镀锌镍合金本色钝化,防腐性能较高。
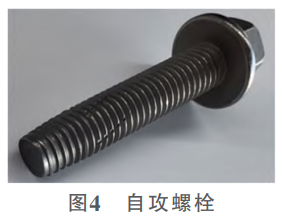
2.4 3种接地紧固件特点对比
接地紧固件特点对比见表1。
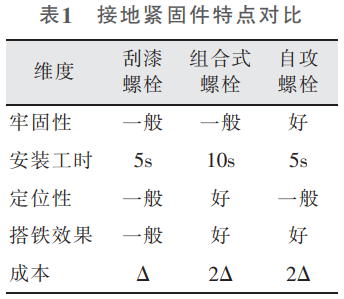
表1从牢固性、安装工时、定位性、搭铁效果和成本等维度对3种接地紧固件进行比较。
综合来说,刮漆螺栓应用较普遍,在一些要求不是很高的安装环境,例如车身内部线束的接地点,这些位置不承受大载荷或者冲击载荷,也不容易接触到腐蚀杂质等恶劣环境,所以能满足基本的接地导电性能即可。组合式螺栓和自攻螺栓表面处理防腐性能较高,一般用在车身外部,例如机舱线束或者底盘部位的接地点,这些位置容易受到外部液体、泥污、道路盐侵害,所以除了满足基本的接地导电性能外,还要提高螺栓的抗腐蚀能力。
组合式螺栓因为是将螺栓头焊接到车身钣金上,采用螺柱焊植焊工艺,车身钣金不需要开通孔。这样在一些车身钣金无法开孔焊接螺母的位置进行应用,保证了车身内外密封效果。例如机舱前围板上的接地点大量采用组合式螺栓。
在一些工况复杂的位置,例如被紧固的电器件承受较大载荷或者冲击载荷,优先采用自攻螺栓,因为自攻螺栓在拧紧到对配件上后,对配件的内螺纹和自攻螺栓的外螺纹配合间隙最小,有一定的锁紧功能,因此牢固性好,提高了紧固可靠性[3]。
3、新型汽车用接地紧固件的设计与制造技术
相对于刮漆螺栓、组合式螺栓都需要在车身上进行焊接施工,而自攻螺栓可以直接和车身上的基孔进行连接达到接地导电功能。这里自攻螺栓接地紧固件特指Taptite2000自攻螺栓。Taptite2000自攻螺栓应用越来越广泛,特别是轻量化材料铝合金车身上,接地紧固件选用自攻螺栓,装配效率得到提升,同时因为自攻螺栓具有锁紧性能,连接可靠性也得到提升。
3.1自攻螺栓设计
自攻螺栓的头部驱动型式一般为六角法兰面结构,与行业标准六角法兰面螺栓产品相比,相同螺纹规格的六角对边尺寸要大一个档,例如M6规格的标准六角法兰面螺栓六角对边尺寸为8mm,而M6规格的自攻螺栓六角对边尺寸为10mm。这样设计的目的主要是为了在生产线上和同规格的普通螺栓进行防错,避免操作者拿错零件或者安装到错误的位置。
自攻螺栓的螺纹杆设计成三棱形,在攻入对手件基体材料时,让对手件基体材料受挤压变形,变形过程中材料延展流动更加顺畅,形成与螺栓规格相对应的内螺纹[4],如图5所示。
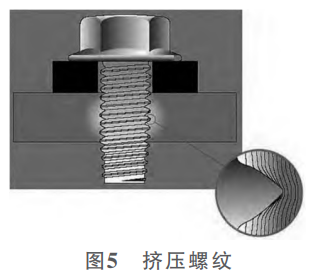
自攻螺栓的末端螺纹区域经过感应淬火。感应淬硬区必须包括整个自攻螺纹区,且第1颗完整螺纹的淬硬层深度在螺纹小径往中心线距离0.2mm以上,如图6所示阴影部分。如果具有特殊的导向端,第3颗完整螺纹应尽可能在感应淬硬区内。
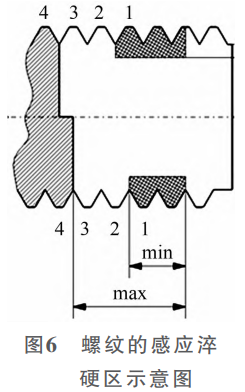
3.2自攻螺栓制造技术
自攻螺栓的原材料需要采用中碳合金钢,经过调质热处理后机械性能为10.9级,关键工艺是Taptite2000自攻螺纹成型和末端螺纹区域感应淬火。Taptite2000自攻螺纹是一种创新的三角杆螺纹设计,即圆弧螺纹,比普通三角杆螺纹紧固件性能更好,保留三角螺纹形状的原理的同时,增加了圆弧。因此,Taptite2000自攻螺纹紧固件具有更卓越的机械性能、装配性能和降低操作人员劳动强度的特性。该螺纹成型需要定制特殊的搓丝板工装,通过增加末端螺纹的不圆度,大大降低了攻入扭矩。以M6规格自攻螺栓为例,普通三角杆螺纹紧固件攻入扭矩10N.m,Taptite2000自攻螺纹紧固件的攻入扭矩只需要6N.m。
为了攻入无内螺纹的对手件基体材料中,自攻螺纹区域局部进行了高频感应淬硬。最后自攻螺栓经过电镀表面处理,不涂封闭剂或者浸涂导电性封闭剂。当前行业应用较普遍的自攻螺栓螺纹是Taptite2000专利螺纹,故单颗螺栓的成本也较高,但是从整个紧固系统来看,这种自攻螺栓的综合使用成本更低[4]。
就3种接地紧固件来说,自攻螺栓也有它的局限性,在车身钣金不能开孔的情况下自攻螺栓无法应用,应选择组合式螺栓。再者,Taptite2000专利螺纹附加成本对小批量用户来说是一个负担,这需要通过其他地方,例如提升总成零件附加值,来进行平衡。
4、结论
汽车接地紧固件设计选用应考虑具体的安装使用环境,最重要的是保证导电性,提供安全可靠的接地性能,能够在特定场景解决电磁干扰问题,同时还要满足安全法规要求。自攻螺栓(Taptite2000专利螺纹)虽然有其优势,但是当前单件成本还相对较高,需要持续扩大行业应用范围以期分摊成本,或者研发出替代产品。组合式螺栓可以解决车身钣金不开孔的搭铁点接地问题,保证密封效果。刮漆螺栓满足一般的车身内部线束接地要求。
无论是哪一种接地紧固件,都面临耐腐蚀的问题,在较恶劣的应用环境中,表面处理防护就显得很关键,目前行业内采用电镀锌镍较普遍,但是在工作状态下,通电的接地紧固件和线束及车身钣金形成原电池闭合回路,极大加速了腐蚀程度,新的防腐材料和工艺需要进一步研究。
参考文献:
[1]王义夫,乔佳伟.发动机线束接地对电控件工作影响的研究[J].小型内燃机与车辆技术,2018(47):12-15.
[2]廖冬琴.线束接地点紧固件工艺分析[J].内燃机与配件,2017(23):26-27.
[3]钱海挺,秦歌.两种新型金属自攻钉的紧固性能研究[J].汽车零部件,2019(12):83-87.
[4]刘金锋,柴之龙,王斯博,等.一种自攻锁紧螺栓及其装配工艺研究[J].汽车工艺与材料,2023(6):25-30.
相关链接