引言
基础能力是决定国家核心竞争力和可持续发展的关键性支撑能力,是保障国家全面安全的核心。
紧固件作为典型的“工业四基”,是工业中应用最广泛的基础产品,也是支撑建设强国和国家经济发展的重要组成部分。中国作为世界上最大的紧固件生产国,每年均保持约10%的增长率,虽然带动了相关制造行业的高速发展,但却面临着低端紧固件过剩、高端紧固件供不应求的局面[1]。
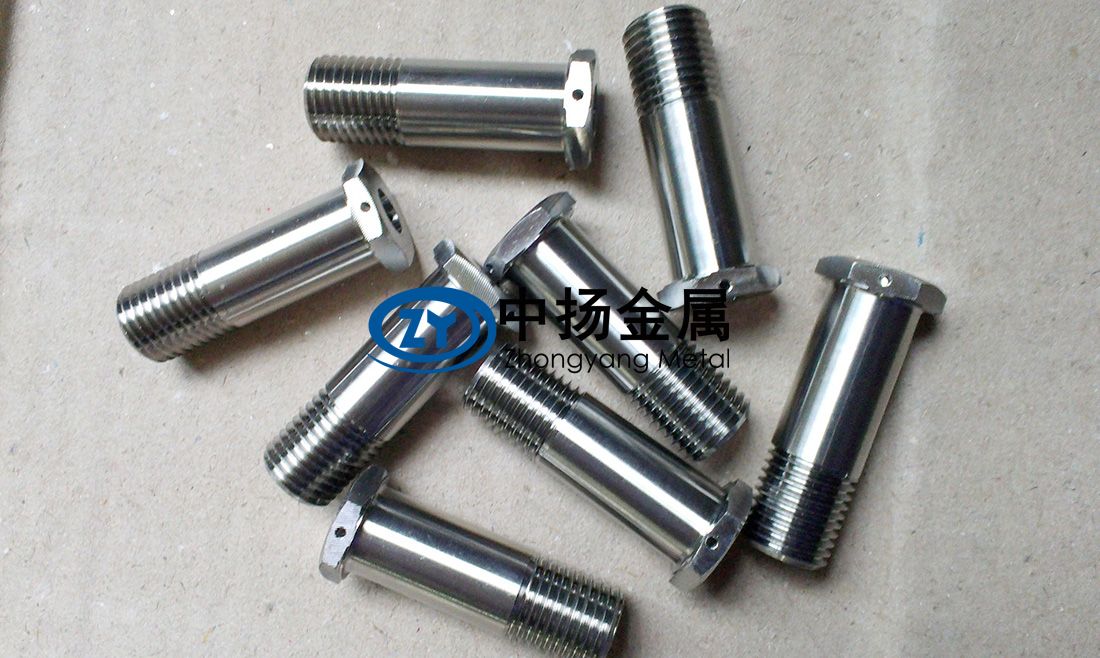
航天用紧固件是典型的高端紧固件,由于航天任务的特点,需要经历复杂、恶劣的环境条件,其产品设计和应用的合理性直接决定了飞行可靠性。除高性能、高可靠性、高精度的需求外,对航天用紧固件产品品种系列的完整性、操作维护的便捷性、批量使用的经济性等均提出了极高的要求。需要对标航天型号需求,在提升自主可控产业链、供应链韧性和安全水平的基础上,凝聚并培养专业力量,提升航天用紧固件的设计能力和技术水平,稳定支撑航天强国建设。
按照航天紧固件全生命周期要素,紧固件的标准体系包括产品标准、管理标准、基础标准、设计及选用标准、制造标准、试验标准、安装操作标准和使用维护标准共8个类别,从纵向管理维度覆盖采购管理单位、设计与选用单位、生产制造单位、安装操作单位、使用维护单位等,从横向设计维度覆盖产品设计、生产、验收、使用、维护等过程。在以上8个类别中,产品标准为最终的实物载体,因此本文主要以紧固件产品为研究对象,通过对航天高端紧固件产品的应用和发展情况进行分析和阐述,结合未来发展需求对紧固件进行展望,推动产学研用一体化发展,支撑航天型号高质量发展。
1、航天紧固件标准体系
紧固件是典型的标准产品,作为工业装配、国际贸易的重要技术依据和认证法规,紧固件标准体系的建设为各国所重视,并组建国际标准化组织紧固件技术委员会(ISO/TC2),开展各项紧固件标准研制。针对航空航天用高端紧固件,由航空航天器标准化技术委员会/航空航天紧固件分技术委员会(ISO/TC20/SC4)制定并管理[2]。目前,ISO紧固件标准有96项,详见图1。从产品类别上主要包含螺纹、镶嵌件等6类,从特性类别上主要包含紧固件尺寸标准和采购规范等8类[3]。
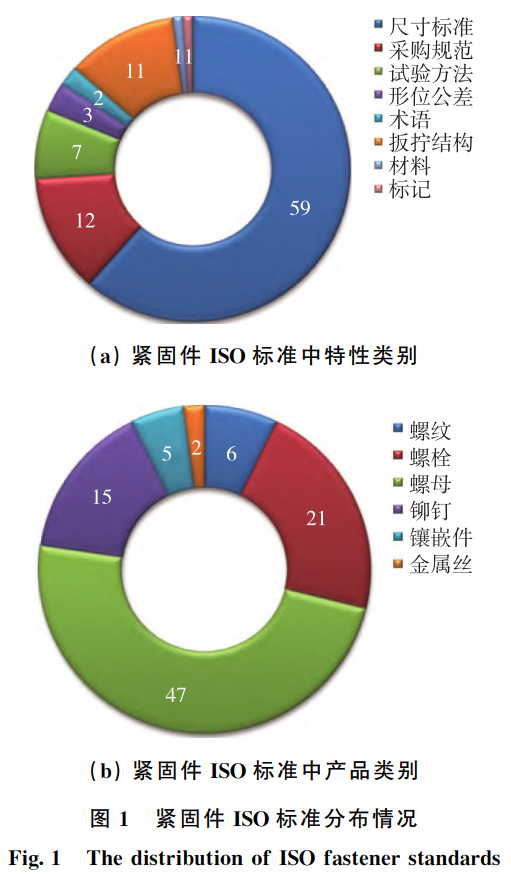
但由于各国的材料体系和工艺水平不一,ISO并未统一紧固件材料、表面处理标准。
在ISO标准体系的牵引下,各国根据工艺水平和应用需求开展标准体系建设。美国航空航天紧固件标准由美国航空航天工业协会AIA和美国国家标准化协会ANSI归口,欧洲由欧洲航空航天制造商协会AECMA归口,都形成了较为健全的紧固件产品型谱,并不断基于本国航空航天需求进行体系的扩展、优化。例如美国的NASM1515《航空航天紧固件系统》[4]是一个健全实用的紧固件型谱标准,包含了航空航天用螺栓、螺钉、螺桩、螺母、铆钉、垫圈、销轴等各产品的型谱划分。我国的紧固件标准起步较晚,但在20世纪50年代末,紧固件作为新中国成立以来第一批颁布的国家标准(GB)受到了高度重视,全国紧固件国家标准化技术委员会(SAC/TC85)开展了4轮全面修订和宣贯[5],并逐渐形成国家标准(GB)、国家军用标准(GJB)等紧固件产品标准体系,广泛应用于机械、电子、交通、建筑、船舶等工业领域。对于航天紧固件来说,主要特点是力学性能好、精度高、可靠性高,而且对材料有严格的要求,在以上标准体系的基础上根据不同场景和型号需求,制定了大量的院级标准、厂所级标准等企业标准,构成了如图2(a)所示的我国航天紧固件产品标准体系,其产品类别主要涵盖螺栓/螺钉、螺柱、螺母、铆钉、垫圈、挡圈、销、螺纹衬套、镶嵌件、组合件等10大类产品,详见图2(b)。
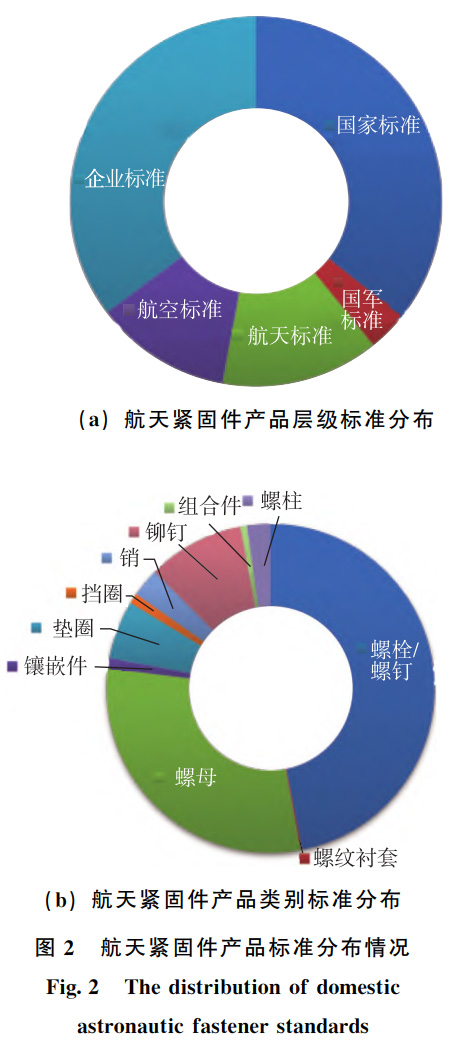
2、航天紧固件材料体系
紧固件材料直接决定了紧固件的力学性能和温度性能,要根据使用需求和使用环境确定材料。ISO将螺栓和螺母的强度等级分为450,600,900,1000,1100,1210,1250,1275,1550,1800MPa,共10个等级;将温度等级分为120,175,235,315,425,450,550,650,730,760℃,共10个等级[6],但对于每个等级大多只规定了化学成分的范围,而非具体牌号。对于航天紧固件来说,对材料的规定不仅要包含材料的牌号,还要规定材料的技术条件。目前,国际上主流的紧固件材料体系以高温合金、钛合金、不锈钢、铝合金为主。
2.1高温合金
高温合金材料的紧固件综合性能优异,能够应用于600℃以上的高温环境下,且具备优良的抗氧化、耐腐蚀性能,广泛应用于航天发动机、气动端头等具有高温烧蚀及大热流气动冲刷等关键部位的连接。我国从20世纪60年代起开展国产高温合金棒丝材的试制,并逐渐在航空航天领域中推广应用[7]。紧固件常用的高温合金材料主要有GH4169,GH2132,GH4738和GH6159等,其材料参数及适用性见表1。
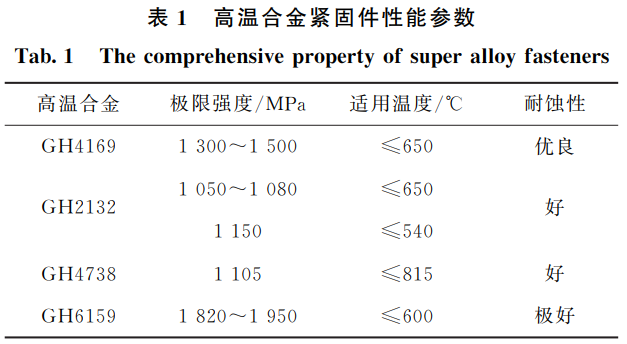
GH4169对标国外Inconel718,是一种沉淀强化型镍基高温合金,以(γ相)奥氏体为基体,在-253~650℃区间内具有良好的综合性能,是航天领域紧固件应用范围最广的高温合金材料。GH2132是一种时效硬化铁基高温合金,国外牌号为A286。与GH4169相比,GH2132的极限强度虽然相对较低,但具有较好的加工塑性和可焊性,因此可制备产品的种类更加繁多[8]。与GH4169相似,GH4738也是一种沉淀硬化型镍基高温合金,对应国外Waspaloy牌号,其高温环境的适应性更强,研究表明GH4738能够在815℃下具有稳定的强度和耐腐蚀性[9]。GH6159合金是在钴基高温合金基础上发展起来的一种新型高强度高温合金,国外牌号为MP159,经过冷拔和时效处理后,强度水平能达到1800MPa以上。
2.2钛合金
钛合金是20世纪50年代发展起来的一种重要的结构金属[10],其在室温下能够形成一层极好的、保护性能的钝化层,因此其耐蚀性能较好,此外低温性能很好,在液氮温度下也能保持良好的塑性和韧性,被称为“太空金属”“海洋金属”[11]。目前我国航天钛合金紧固件主要用于复合材料连接、耐腐蚀性要求较高以及对箭体结构质量要求较为严格的部位。所用的钛合金紧固件材料根据合金元素成分和常温组织形貌大致分为3类:α钛合金(代号为TA)、β钛合金(代号为TB)、α+β钛合金(代号为TC)。钛合金紧固件的材料属性见表2。
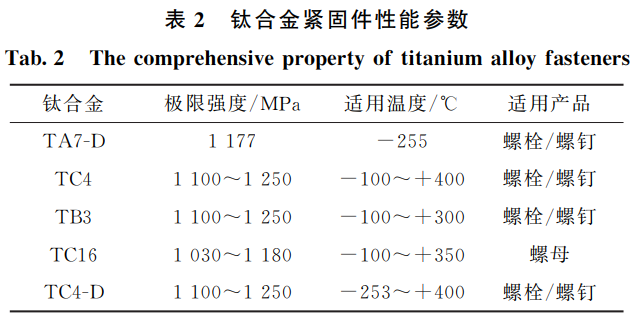
TA7-D是用于超低温环境下的低间隙α钛合金,又称为TA7-ELI。在常温状态下,其抗拉强度为686MPa;在低温条件下,其能够在保证伸长率≥8%时抗拉强度显著提升。TC4对标国外Ti6Al-4V材料,是典型的低Mo当量α+β钛合金,具有密度小、疲劳性能高、材料成本低的特点[12]。TB3钛紧固件最早应用于东方红卫星上,在保持1100MPa极限强度的基础上,疲劳性能略有降低,成本增加。TC16钛合金对标苏联研制的BT16材料,通过退火过程中的再结晶实现优异的室温工艺塑性,在稳定的工艺下可保证冷镦成型的组织均匀性[13]。TC4-D是TC4优选改型,通过控制合金元素Al和V的波动范围及杂质元素含量,提高断裂韧性和疲劳裂纹扩展抗力等损伤容限性能[14],又称为超低间隙钛合金材料[15](TC4ELI)。目前国内紧固件钛合金材料需要在工艺成熟度和产品稳定性方面持续加强建设[16]。
2.3沉淀硬化不锈钢
为适应复杂的工况需求,航天产品在起吊、支撑、集中力传递等局部大载荷承力结构中广泛应用高强钢紧固件。高强合金钢、碳素钢等紧固件是国内标准体系中占比最高的产品[17],但存在回火脆性、氢脆以及耐蚀性差等问题。沉淀硬化不锈钢是在不锈钢化学成分基础上添加不同类型、数量的强化元素,通过沉淀硬化过程析出不同类型和数量的碳化物、氮化物、碳氮化物和金属间化合物,提高钢的强度又保持足够的韧性的一类高强度不锈钢,简称PH钢[18]。根据基体的金相组织可以分为马氏体型、半奥氏体型和奥氏体型3类,其中常用于紧固件材料的主要为马氏体型05Cr17Ni4Cu4Nb和半奥氏体型0Cr13Ni8Mo2Al,0Cr12Mn5Ni4Mo3Al等,其材料参数见表3。
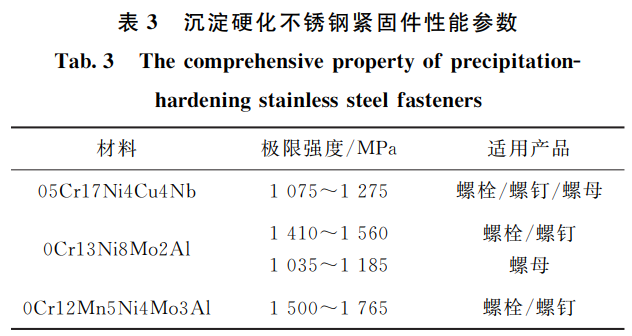
05Cr17Ni4Cu4Nb是在Cr17型不锈钢基础上,加入Cu,Nb等元素研制而成,与美国17-4PH、法国Z5CNU17-04等牌号相近,在保持较高强度的基础上,其耐大气腐蚀和耐酸腐蚀能力明显优于马氏体不锈钢[19],用于取代传统高强钢30CrMnSiA材料。0Cr13Ni8Mo2Al不锈钢对标美国13-8Mo材料,不仅具有高硬度和优良的综合性能,而且在相当大截面上可淬透并获得较好的纵、横向一致性能[20],通过设计不同的热处理制度满足不同的设计需求。0Cr12Mn5Ni4Mo3Al不锈钢与美国17-7PH、苏联CH4材料牌号相近,具有良好的韧性以及加工成型性能,经过适当的冷变形、冷处理以及时效后,可将组织部分转变为马氏体,获得较高的强度[21]。
2.4铝合金
铝合金紧固件凭借其高比强度、高比刚度、成本低廉、耐腐蚀且抗冲击性能良好等特点,成为航天领域首选的轻量化材料。从1906年至今,通过持续开展高合金化、微合金化、纯净化和热处理研究,推动铝合金由静高强度向高强高韧耐蚀综合性能优良发展,其中航天紧固件目前主要采用的是Al-Cu系(2×××系)和Al-Zn-Mg-Cu系(7×××系)[22]。截至2022年,材料发展及铝合金紧固件相关专利的统计结果见图3。
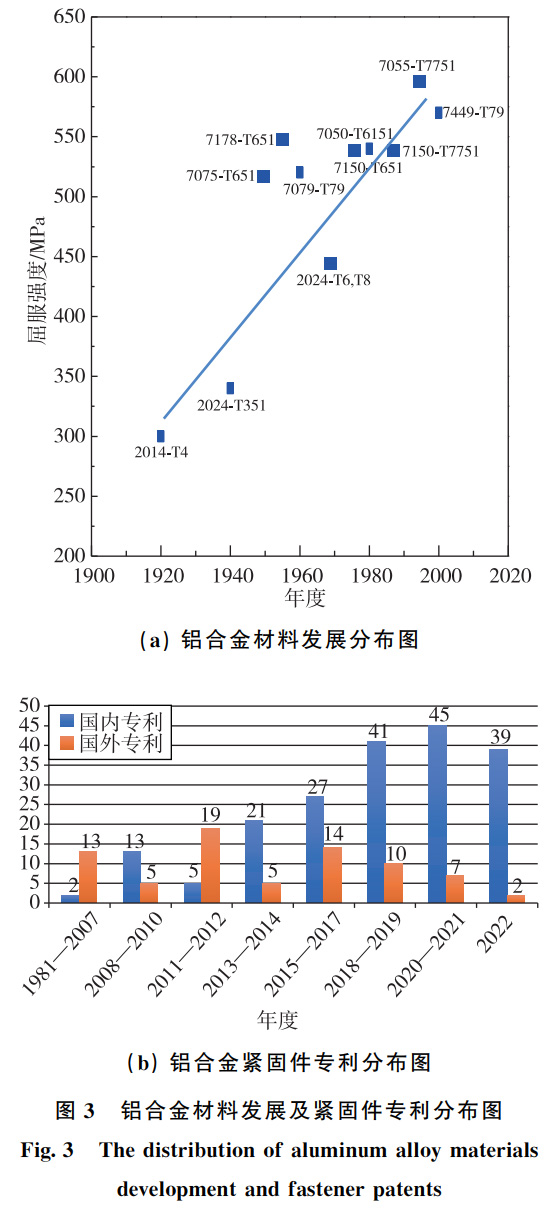
2012年1月,国务院正式印发了《工业转型升级规划(2011—2015)》,提出高端装备制造产业在内的7大战略性新兴产业的重点发展方向和任务,有效促进了基础工业、材料行业的发展。自2013年开始铝合金紧固件材料专利数量呈现逐年上升的态势。从专利分布来看,高强铝合金紧固件的研发基本上是沿着高强度、低韧性→高强度、高韧性→高强度、高韧性、高耐腐蚀性能发展的,时效处理沿T6→T73→T76→T736(T74)→T77方向发展[23]。在合金设计方面的发展特点是合金化程度越来越高,Fe,Si等杂质含量越来越低,微量元素添加越来越合理,最终合金强度大幅度提高的同时,合金又具有优良的综合性能。常用的铝合金紧固件性能参数见表4。
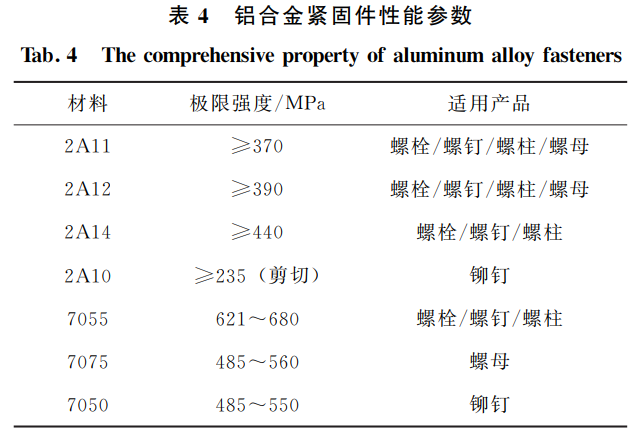
3、航天紧固件表面处理体系
紧固件表面处理是为了实现总体性能,对紧固件表面进行改性,以满足防腐、润滑、耐磨、耐高温氧化、装饰等要求。对于航天高端紧固件来说,表面处理的防腐和润滑是最主要的两类表面防护需求[24]。其中,为避免紧固件基体在环境因素(海洋、潮湿、大气及真空)下通过反应而产生化学腐蚀、电化学腐蚀、电偶腐蚀、缝隙腐蚀[25]、电腐蚀等,受到破坏性侵害,采用涂镀层将基体与外界环境进行隔绝,实现防腐功能;通过选择表面硬质涂镀层或者润滑涂镀层,甚至复合涂镀层[26],减小螺纹副之间的摩擦系数,隔离两种材料的直接接触,提高螺纹副之间的润滑性能来防止咬死。
紧固件的表面处理应与基体材料联合作为一个系统进行设计,使其材料表面获得所期望的功能或性能。表面工程作为美国工程科学院2060年前集中力量加强发展的92项新科学技术项目之一[27],得到了科学界广泛关注。目前紧固件表面防护主要技术大类有电镀、涂覆、转化膜、真空镀膜、热渗技术等。具体细分技术有几十种,如图4所示,包括电镀锌、电镀镉、电镀镉钛合金、电镀锌镍合金[28]、电镀铜、电镀银[29]、电镀铬、电镀镍、喷涂铝屏蔽涂层、喷涂富锌涂层、喷涂二硫化钼、涂十六醇、涂油脂、喷涂达克罗及改进无铬涂层(久美特、美加力、德尔肯、锌加等)、钛合金及铝合金各类阳极化膜层和微弧氧化膜层、磷化、氧化、钝化、草酸盐润滑、氟硼化、离子镀铝、离子镀氮化铬等硬质膜层、热渗锌、扩散镍镉镀层、喷丸、磁力研磨等各类光整技术。
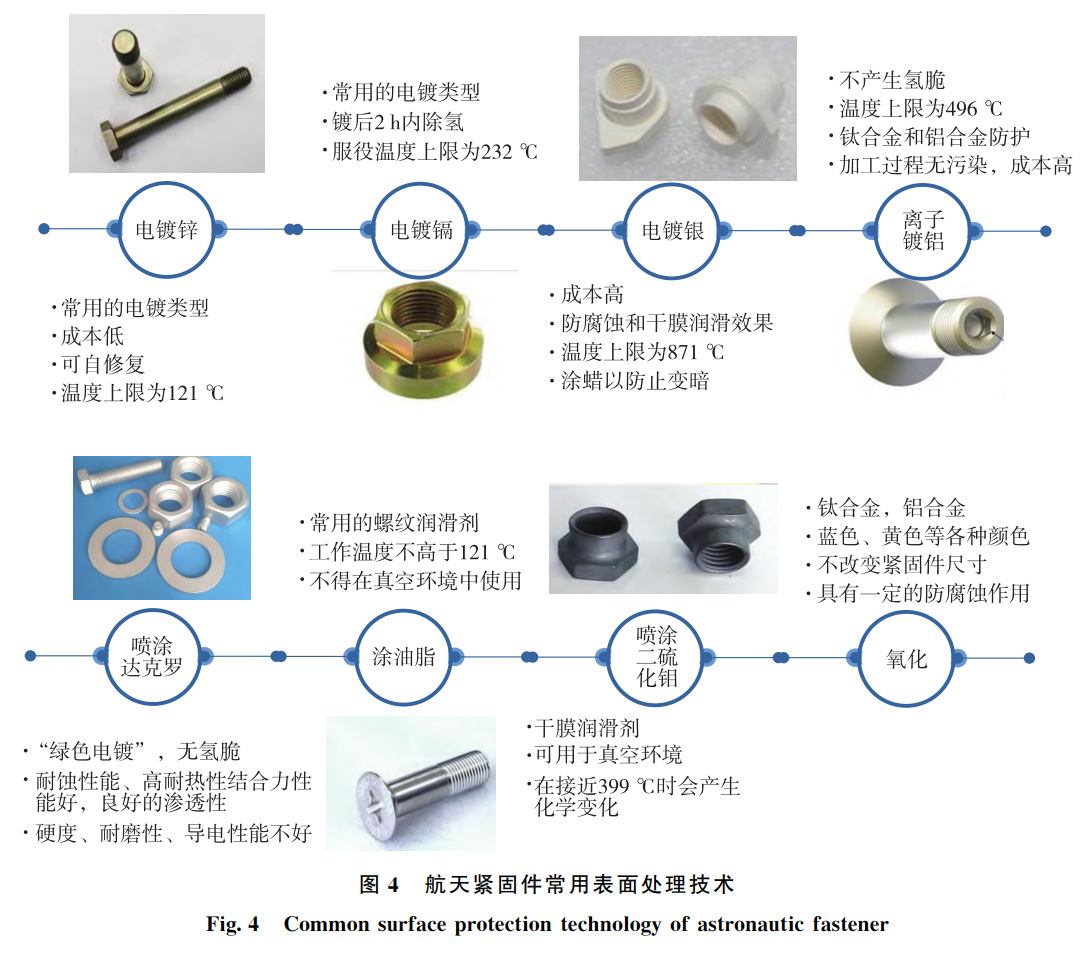
随着微观科学的发展,纳米涂层由于其优秀的表面与界面效应、小尺寸效应、隧道效应,与基体材料形成强的结合力,可显著改善涂层的致密效应,大幅提升涂层对腐蚀介质的屏蔽作用。
目前T35纳米涂层已经在航天紧固件产品中大量应用,详见图5。其能够适应≮720h中性盐雾试验的环境条件,支撑运载火箭的海上发射和沿海发射场高盐雾条件下的任务执行。
此外,为提升产品的一致性,对紧固件的表面处理工艺应进行标准化处理,并作为关键工序开展生产过程控制。
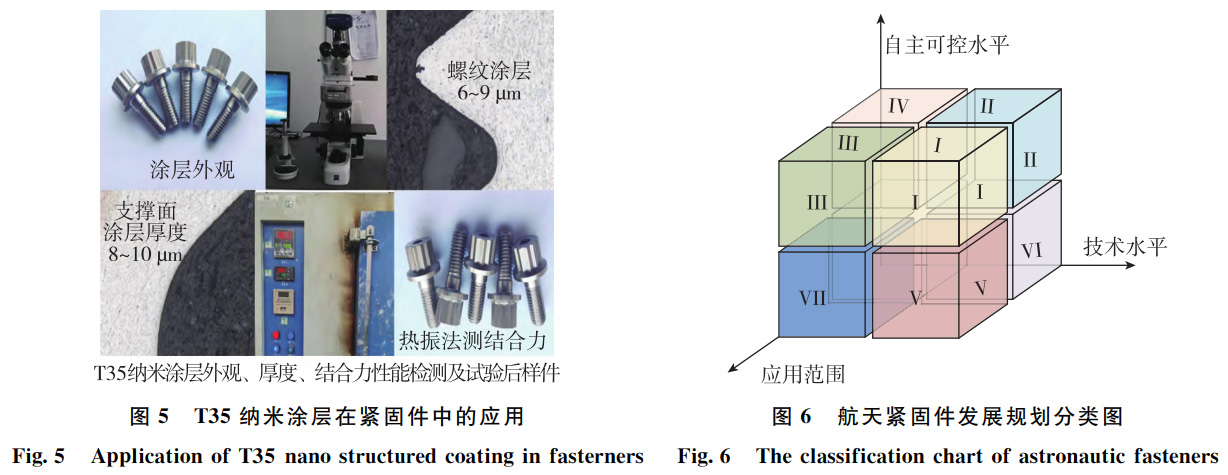
4、航天紧固件产品发展规划
航天紧固件的发展主要以产品性能提升为主,造成各层级标准繁杂,缺乏统筹规划。按照“需求导向、场景牵引、中试验证、串珠成链”的原则,航天高端紧固件产品需要在符合应用场景的前提下才能发挥其性能,因此对标航天强国建设和高质量发展,充分发挥应用需求方的技术牵引能力,考虑产品技术水平、型号应用范围,建立自主可控评价维度,形成图6所示的紧固件发展规划分类。
1)Ⅰ类产品:产品技术水平高、型号广泛应用,自主可控需求高。
该类产品是高端紧固件重点建设和发展的对象,其特点为技术水平先进,且对于自主可控、产品稳定供应要求较高,但技术难度较大,成熟度不足,导致产品的研发速度较慢,成本较高。2)Ⅱ类产品:产品技术水平和自主可控需求高,但型号应用范围不广。
该类产品的特点是应用在极端环境条件下,对型号成败起关键作用,需求数量虽然不大,但需要保证产品的稳定供应。通常一件产品就能决定火箭的成败,例如发动机连接、助推捆绑连接位置的产品。该产品的成本较I类产品更高,通常技术研发难度也更大,是从技术维度上需要重点攻克的对象。
3)Ⅲ类产品:技术水平虽然不高,但产品在型号中广泛应用,需要国产稳定供应。
该类产品应用场景和工艺加工难度均无特殊要求,成本低,在加工、使用过程中未产生过质量问题,但按照实战化要求,需要保持该类产品的大量、及时供应。该类产品应形成稳定供应机制,从管理层面加强过程控制,降低成本。
4)Ⅳ类产品:技术水平和需求数量较低,但需要自主可控。
该类产品在火箭上有一定的应用场景,但技术水平相对较低,成本低廉,竞争优势小,出于型号国产自主可控的指标要求,需要开展国产生产线开发。该类产品应在综合分析应用场景和成本的基础上,通过统标统型和产品化设计向Ⅲ类产品过渡,从而进一步降低Ⅲ类产品在批次鉴定、验收过程中的成本。
5)Ⅴ类产品:产品技术水平高,型号广泛应用,但未实现产品或原材料的自主可控。
该类产品多见于采用国际集采方式的紧固件,例如从美国ARCONIC集团、PCC集团和法国LISI集团等国外高端紧固件生产商大量进口。另外,还有部分产品虽然国内生产,但原材料、关键设备均依赖进口。
按照高质量发展要求,该类产品应向Ⅰ类产品发展,但需要投入大量的基础资源进行自主可控研发。
6)Ⅵ类产品:技术要求高,但应用范围和自主可控需求相对较低。
该类产品作为航空、航天关键紧固件产品,由于国内原材料、生产稳定性等问题,采用直接进口、原材料进口国内加工等方式实现,例如型号中依然存在的Inconel718,A286,Ti-6Al-4Vi等材料,在低冲击分离装置、专用大规格承力螺栓类产品中有所应用。该类产品应坚定不移向Ⅱ类产品过渡,坚持技术研发和原材料开发,实现国内稳定供应能力。
7)Ⅶ类产品:技术水平相对较低,大量依赖进口供应。
该类产品技术水平不高,但由于研制模式或研制成本的考虑,通过进口方式进行配套和供应。其使用量大、成本较低、供应相对稳定,造成改进的动力不足,容易形成空心环节。
8)Ⅷ类产品:技术水平和使用量低,且依赖进口。
航天高端紧固件较少涉及该类产品。
5、结论
紧固件作为典型的机械零部件,是支撑工业建设的重要基础。由于复杂的飞行环境条件和严格的质量管理要求,航天紧固件除了要适应高强度、高耐热、高成型性能的需求之外,还应该注重设计发展规划,并通过提高工艺水平满足苛刻的技术和质量要求。本文通过分析航天紧固件的发展现状,结合航天强国建设目标和任务需求,分析未来航天紧固件的发展趋势。
1)针对紧固件标准体系建设,应秉承“需求牵引、问题导向、装备验证、应用落地”的原则,由型号应用单位构建紧固件顶层规划,着力开展满足快速装配、性能检测及适应极端环境的紧固件产品研发,建立健全航天高端紧固件主干型谱,形成紧固件产品设计要素的建设目标,切实推进产品技术方案统一和统标统型建设及型号高质量应用。
2)针对紧固件材料体系建设,应按照“自主高效、技术先进、绿色制造、体系完整”的思路,全面推进材料国产自主可控发展,以典型产品为试点,推进“单项冠军”模式,避免不良竞争造成供应链路分叉、弱化的现象,从而推进Ⅲ,Ⅳ类产品技术升级和Ⅴ,Ⅵ,Ⅶ类产品向国产化改进。
3)针对紧固件关键工艺和产品质量控制,按照“过程监控、数字驱动、开放融合、精益生产”的高质量发展要求,针对现有生产制造环节管控的精细程度不足的问题,基于PCD(生产过程控制)与SPC(统计过程控制)推进精益制造,实现Ⅰ,Ⅱ类产品强链发展,同时优化紧固件采购和配套流程,避免小批量、特殊需求产品的过度生产,从而推进Ⅳ类产品向Ⅲ类产品过渡。
4)针对未来型号发展对紧固件专业的需求,应立足“优势集中、技术为本、创新创造、勇于开拓”的组织及人才发展战略,提升航天紧固件专业影响力和核心竞争力,集中技术合力开展共性技术研究,拓展新质生产力,带动行业基础技术和产业发展。
参考文献
[1] 王肇宇.国际航空航天紧固件发展现状及趋势研究[J].宇航总体技术,2018,2(4):1-7,30.
[2] 任赤兵.欧美紧固件验收检查标准解读[J].机电产品 开发与创新,2021,34(6):138-144,155.
[3] 高岩.高端紧固件紧固工艺技术研究[D].大连:大连 理工大学,2016.
[4] NASM1515.Fastenersystemsforaerospaceapplications[S].America:AerospaceIndustriesAssociation ofAmerica,2011.
[5] 全国紧固件标准化技术委员会秘书处.紧固件标准实 施指南[M].2版.北京:中国标准出版社,2018.
[6] AnupindiR.Boeing:thefightforfasteners[M].William DavidsonInstitute,2009:4-19.
[7] 朱行欣,胡晓培.国内航空航天用高温合金紧固件发 展现状[J].金属制品,2023,49(3):1-3.
[8] QiH.Review ofINCONEL718alloy:itshistory, properties,processinganddevelopingsubstitutes[J].JournalofMaterialsEngineering,2012(8):96-104.
[9] 刘辉,蔡新宇.热加工参数对 GH738合金动态再结 晶行为的 影 响 [J].钢 铁 研 究 学 报,2014,26(3): 46-50.
[10] FanJK,LiJS,KouHC,etal.Microstructureand mechanicalpropertycorrelationandpropertyoptimizationofanearβtitaniumalloyTi-7333[J].Journal
ofAlloysandCompounds,2016,682:517-524.
[11]李蒙,凤伟中,关蕾,等.航空航天紧固件用钛合金 材料综 述 [J].有 色 金 属 材 料 与 工程,2018,39(4): 49-53.
[12] 胡玉佳.TC4航空紧固件温镦成形及其微观组织研 究[D].上海:上海工程技术大学,2021.
[13] 杨万博.TC16钛合金航空紧固件冷镦塑性损伤研究[D].上海:上海工程技术大学,2021.
[14] 雷文光,韩栋,张永强,等.不同热处理工艺对 TC4- DT钛合金棒 材 组 织 和 性 能 的 影 响 [J].材料 导 报, 2015,29(14):120-123.
[15] 于培师,赵宇翔,吴连生,等.TC4ELI钛合金疲劳裂 纹路径偏 析 与 寿 命 提 升 机 制 [J].机 械 工程 学 报, 2023,59(16):72-81.
[16] 董瑞峰,李金山,唐斌,等.航空紧固件用钛合金材 料发展现状[J].航空制造技术,2018,61(4):86-91.
[17] 刘汉宝.ASME 规范中碳钢和低合金钢材料冲击试 验规定的探讨[J].石油化工设备技术,2019,40(1):1-5.
[18] 王帅,卢红立,石玉红,等.MJ螺纹沉淀硬化不锈钢 螺栓破坏研究[J].强度与环境,2022,49(5):82-87.
[19] 胡庆宽,许永春,金宏.0Cr17Ni4Cu4Nb材料在宇航 紧固件中的应用[J].金属加工(热加工),2021(6):95-98.
[20] 唐科,李岩,胡振兴,等.PH13-8Mo沉淀硬化不锈 钢在航天火工装置中的应用[J].火工品,2022(3): 10-13.
[21] 徐涛,王鹏,周鹏程,等.17-7PH 沉淀硬化不锈钢电 渣重熔过程洁净度的变化[J].特殊钢,2022,43(5):68-73.
[22] 王建国,王祝堂.航空航天变形铝合金的进展(3)[J].轻合金加工技术,2013,41(10):1-14.
[23] 张新明,邓运来,张勇.高强铝合金的发展及其材料的 制备加工技术[J].金属学报,2015,51(3):257-271.
[24] 万冰华,张晓斌,游龚君,等.航空航天紧固件铝涂层 性能 对 比 研 究 [J].电 镀 与 涂 饰,2021,40(24): 1809-1816.
[25] NejadSAT,AlibakhshiE,RamezanzadehB,etal.Theroleofacetylacetoneinalkalinesurfacemodificationbathofelectro-galvanizedsteeltoenhanceprotective functioning of a hybrid silane coating [J].ProgressinOrganicCoatings,2022,171:107048.
[26] 任永跃.电化学制备参数对纳米镍镀层微结构和力学性能调控机制研究[D].天津:天津大学,2019.
[27] ChenJH,XiaYQ,HuYC,etal.TribologicalperformanceandconductivecapacityofAgcoatingunder boundarylubrication[J].Tribology International, 2017,110:161-172.
[28] 卢泰宇,郭绕龙,李艳军,等.螺纹紧固件表面防护 技术综述[J].电镀与精饰,2022,44(12):61-68.
[29] WimanP,Doungkaew K,SiripongsakulT.HydrothermalblackeningonAISI4140steelwithandwithouthydrazinehydrate[J].IOP ConferenceSeries: MaterialsScienceandEngineering,2021,1163(1): 012031.
引用格式:李东,冯韶伟,石玉红,等.航天高端紧固件技术发展现状及展望[J].宇航总体技术,2024,8(5):1-8.
Citation:LiD,FengSW,ShiY H,etal.Thestatusanddevelopmenttendencyofaerospacefasteners
[J].AstronauticalSystemsEngineeringTechnology,2024,8(5):1-8.
相关链接