以波音 787、空客 A350 为代表的新一代大型客机,复合材料用量分别占机体结构重量的 50%和52%,现代大型客机复合材料用量已经成为其先进性和市场竞争力的标志[1]。随着复合材料逐步应用于民机主承力结构,机翼-机身等重要连接结构设计构型、失效模式也随之改变,对结构设计提出了新的挑战。
波音 787 曾由于翼根长桁对接结构设计不当,导致交付延期[2],可见其设计难度和重要性。针对复合材料连接结构,国内外学者从设计方案、失效机理、试验验证等角度开展了大量研究[3-10]。
特别随着我国大型民机的研制进展,国内对于复合材料连接结构的设计也逐渐深入。秦杰等[11]开展了民机机翼根部分离面设计,采用两种典型单根长桁加筋壁板根部对接试验开展验证;吴承思[12]针对 3种常见的复合材料蒙皮连接形式,开展了剪切载荷承载能力试验验证及对比分析;雷凯等[13]研究了飞机机械连接混合结构在运营环境极端温度下产生的热应力,在刚度法基础上考虑温度场引起的变形,获取了结构热应力和钉载分布规律;贾宝惠等[14]通过试验和仿真分析,研究了预紧力对连接件拉伸性能的影响;汤平等[15]对复合材料翼身对接方式、外翼中央翼对接面位置等进行了对比和分析。
根据民机适航法规及咨询通告要求,民机结构应遵循损伤容限设计理念,即在整个使用寿命期间避免由于疲劳、腐蚀、制造缺陷或意外损伤引起的灾难性破坏。对于翼根连接结构,必须考虑紧固件松动、破损等潜在的不安全事件[16],并通过设计保证飞机结构的安全。然而目前国内、外对于含损伤复合材料主承力连接结构的相关探讨较少,尚未充分掌握潜在损伤形式对复合材料翼根连接结构的影响规律。紧固件缺失作为一种服役过程中可能出现的、且对民机安全性带来巨大挑战的失效形式,开展相关研究对进一步理解复合材料翼根连接结构力学特性、保证民机安全具有重要意义。
针对以上问题,本文以复合材料机翼翼根下壁板长桁对接结构为研究对象,设计并制备了完好试验件、关键紧固件缺失试验件,一方面通过试验位移、应变监测,对比了紧固件缺失前、后试验件的刚度变化和受力变化;另一方面针对试验无法直接测量的钉载分配等数据,首先对比验证了仿真分析模型的有效性,而后通过仿真对比了紧固件缺失前、紧固件缺失后钉载分配变化以及三叉接头、对接带板的传载比例变化。研究得到的关键紧固件缺失对复合材料翼根连接结构连接刚度、应力/应变、钉载分配的影响规律和定量分析结果,可为民机复合材料翼根连接结构设计、分析和验证提供参考和借鉴。
1 、试验设计
1.1 试验件
试验件取自民机复合材料机翼翼根下壁板对接区域,示意图如图 1 所示。外翼、中央翼壁板均为 T型长桁,共胶接工艺成型,在 1 号肋处通过琴键式水平三叉接头、外部对接带板连接。其中外翼、中央翼壁板均为 T800 级碳纤维环氧复合材料,蒙皮铺层比例为 45/50/10,长桁铺层比例为 60/30/10;水平三叉接头、外部对接带板材料为 Ti-6Al-4V;1 号肋材料为 7050-T7451。
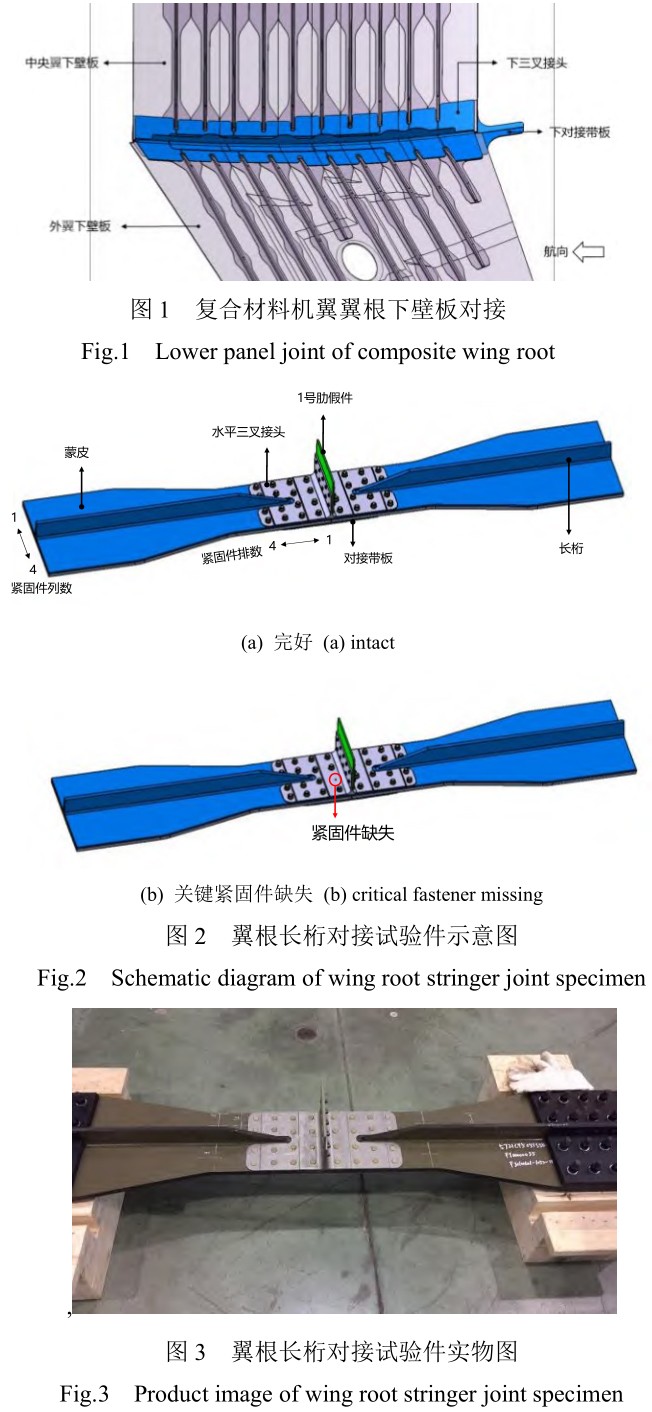
选取翼根下壁板对接结构中的典型区域,设计为翼根长桁对接试验件,如图 2(a)所示。试验件不考虑翼根上反角、后掠角影响,长桁腹板在根部斜削角度为 17.5°。两侧长桁采用对称设计,以外翼侧长桁对接结构为试验考核对象。试验件单侧壁板、三叉接头与对接带板通过 4 排 4 列 14#高锁螺栓连接,按排数-列数的形式对紧固件进行编号;三叉接头立筋与 1 号肋假件通过 2 排 5 列 10#高锁螺栓连接。试验件整体尺寸约为 1900mm(长)×361mm(宽)×172mm(高)。
将连接结构强度校核中裕度最低位置作为缺失紧固件位置,以代表最严酷的情况。根据试验件强度分析结果,定义靠近 1 号肋、靠近长桁腹板区域的紧固件为关键承力紧固件(编号 1-3),将其拆除后作为关键紧固件缺失试验构型,如图 2(b)所示。
试验件实物图如图 3 所示。
1.2 试验内容
试验件共 1 件,首先在完好状态下试验加载至110%参考载荷,而后卸载并开展无损检测,用于验证完好试验件的应变分布及承载能力,记为 LS-01;而后拆除关键紧固件,再次加载至 110%参考载荷,重点考察紧固件缺失后试验件传力特性的变化,记为 LS-02。试验均在室温环境下进行。
为了研究翼根长桁对接结构的传载性能,以及紧固件缺失前、紧固件缺失后连接件应变变化,在试验件重点区域布置应变片,用于测量试验加载过程中的应变数据,如图 4 所示。
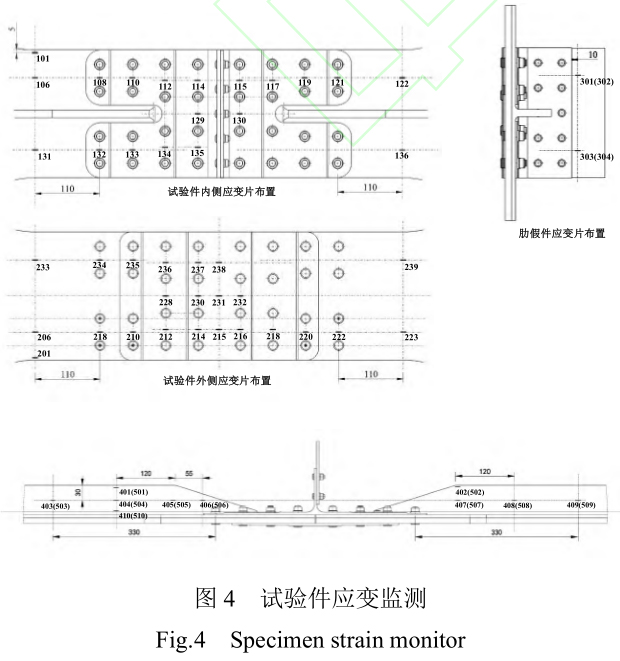
1.3 试验加载
翼根长桁对接拉伸试验在 600t MTS 试验机上进行,试验加载示意图如图 5 所示。试验件两端的蒙皮、长桁与夹具通过紧固件连接,保证加载中心与试验件端部刚心重合;试验件中部肋假件与侧向支持夹具连接,侧向支持夹具可上下自由滑动,以模拟实际飞机结构中 1 号肋对翼根下壁板连接结构的边界支撑条件。
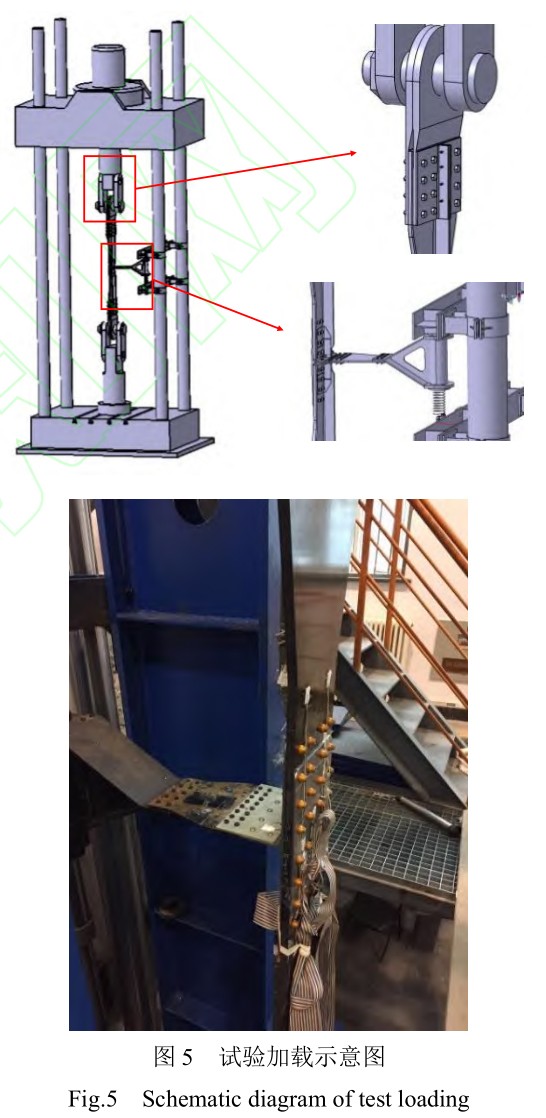
在完成完好试验件拉伸试验后,采用多功能扳手拆除关键紧固件,完成紧固件拆除的试验件如图 6所示。
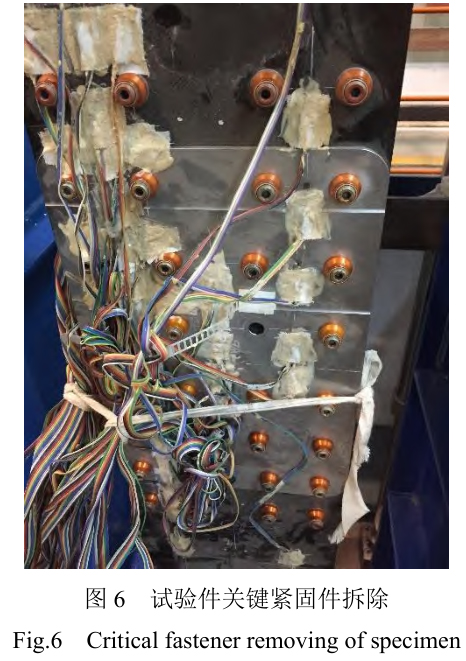
2、 试验验证
2.1 试验过程及结果
LS-01(紧固件缺失前)、LS-02(紧固件缺失后)的载荷-位移曲线如图 7 所示。LS-01、LS-02 的载荷-位移曲线基本重合,表明关键紧固件缺失不会对翼根结构的连接刚度产生显著影响。在民机复合材料翼根连接结构设计中,可见关键紧固件缺失不影响该区域的整体刚度,因此不会导致翼根整体传力路径的变化。
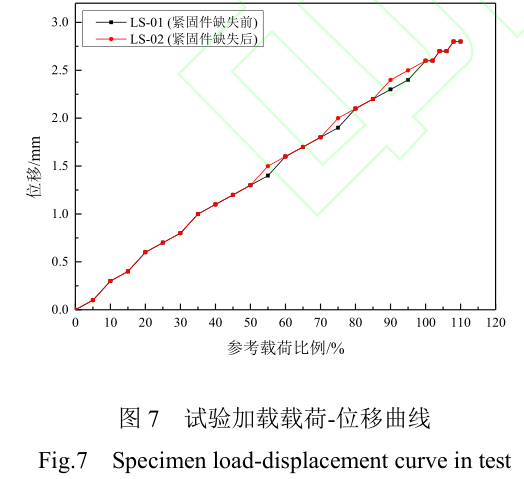
2.2 紧固件缺失对应变影响
为了分析关键紧固件缺失对试验件应变分布的影响,对试验件紧固件缺失前、紧固件缺失后应变监测结果进行对比,分别如图 8-图 10 所示。
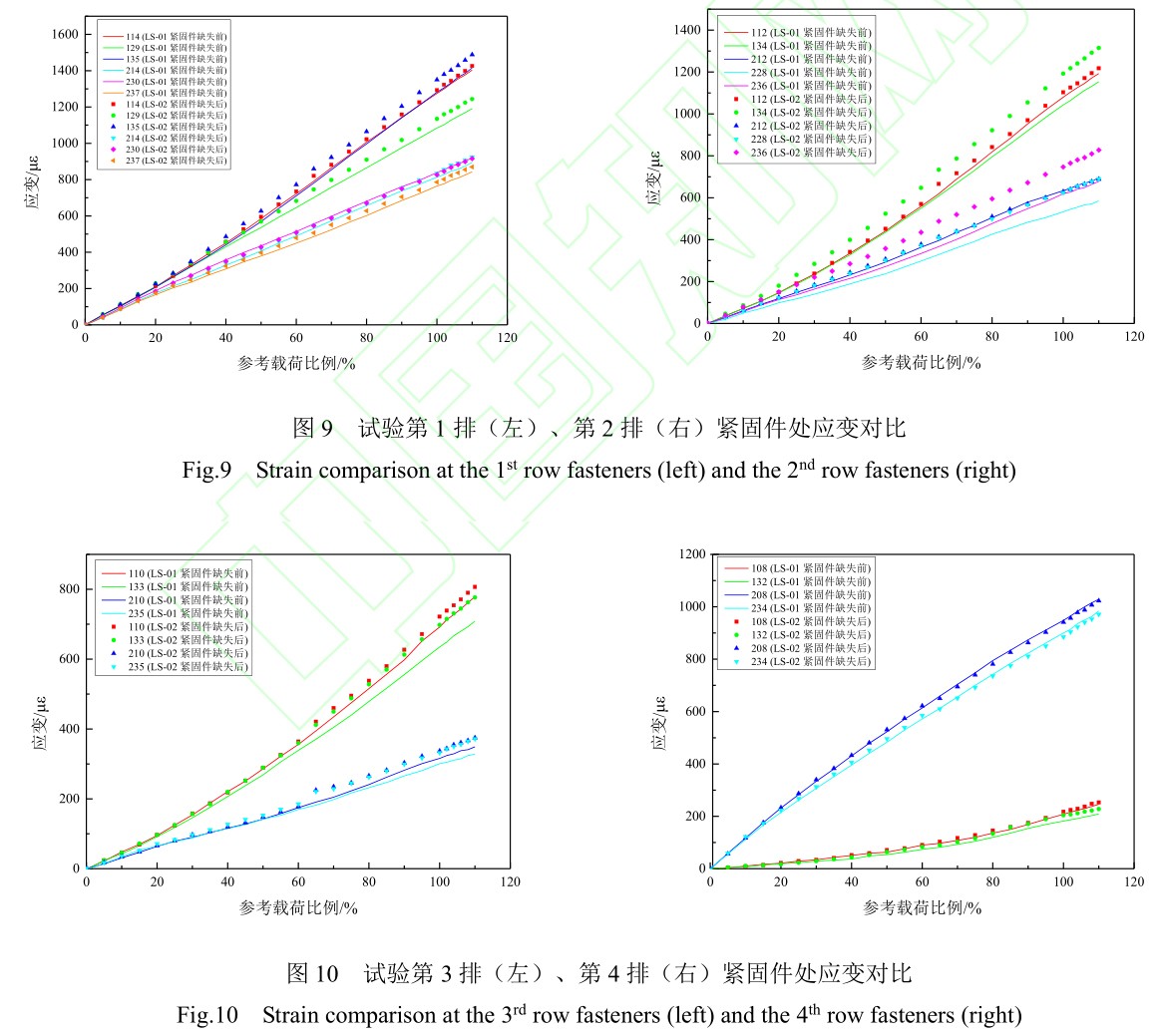
对于试验件远端应变(应变片编号:106、131、206、233)和加载方向对称面处应变(应变片编号:215、231、238),试验件紧固件缺失前、紧固件缺失后并无显著区别(≤3.2%),可见关键紧固件缺失后并未对试验件远端传载、水平三叉接头/对接带板的传载比例产生显著影响。
对于第 1 排紧固件位置的应变片(应变片编号:114、129、135、214、230、237),关键紧固件缺失后,各应变值均略有增加(5%以内),靠近缺失紧固件、远离缺失紧固件位置的应变变化量无显著区别。分析认为,紧固件缺失处由于无钉载,导致对应孔边两侧区域的应变减小;但第 1 排其它紧固件钉载增大,导致对应钉孔两侧应变增大,两者效果叠加,使得第 1 排紧固件处应变变化不大。此外,由于第 1 排处的紧固件缺失后,第 2-4 排紧固件钉载提高,增大了第 1 排紧固件位置的旁路载荷,导致第 1 排紧固件处应变提高。
对于第 2 排紧固件位置的应变片,关键紧固件缺失后,靠近缺失紧固件位置的应变(应变片编号:134、228、236)分别增加了 14.0%、22.1%、17.9%,远离缺失紧固件位置的应变(应变片编号:112、212)无明显变化(<2%)。由于第 1 排紧固件缺失,第 2排靠近紧固件缺失位置的紧固件载荷增加,继而导致对应的应变值增加。
对于第 3 排紧固件位置的应变片,关键紧固件缺失后,靠近缺失紧固件位置的应变(应变片编号:133、235)分别增加了 9.6%和 13.4%,远离缺失紧固件位置的应变(应变片编号:110、210)分别增加了 3.6%和 7.4%,第 1 排处紧固件缺失也显著提高了第 3 排的钉载,但第 3 排处靠近缺失紧固件、远离缺失紧固件的钉载变化量已趋于均匀。
对于第 4 排紧固件位置的应变片,应变片 108、132 位于水平三叉接头上,关键紧固件缺失后其应变值分别增加了 2.8%、9.1%;应变片 208、234 位于复材壁板上,应变值无显著变化。
在民机复合材料翼根连接结构设计中,可见关键紧固件缺失不会对远端应变产生显著影响,即通过远端应变监测无法有效识别紧固件缺失的出现。
紧固件缺失后,主要导致缺失紧固件之后一排处连接件应变的增加,试验测量应变最大增加了 22.1%,局部最大应变增加量还需结合分析模型进一步确定。根据民机设计要求,翼根连接完好试验件需承受极限载荷,关键紧固件缺失后只需承受限制载荷(0.67 倍极限载荷),紧固件缺失后,应重点分析缺失紧固件附近区域各部件的可能失效模式,以保证结构的安全。
3 、数值分析
3.1 有限元建模
试验应变监测仅能捕捉试验件有限位置的应变结果,采用经验证的数值分析模型可进一步分析紧固件缺失前、紧固件缺失后试验件的应变场分布、钉载变化情况。有限元模型前后处理、求解计算采用商用有限元分析软件 Hyperworks 进行,有限元模型如图 11 所示,建模采用的性能参数如表 1 所示[10]。
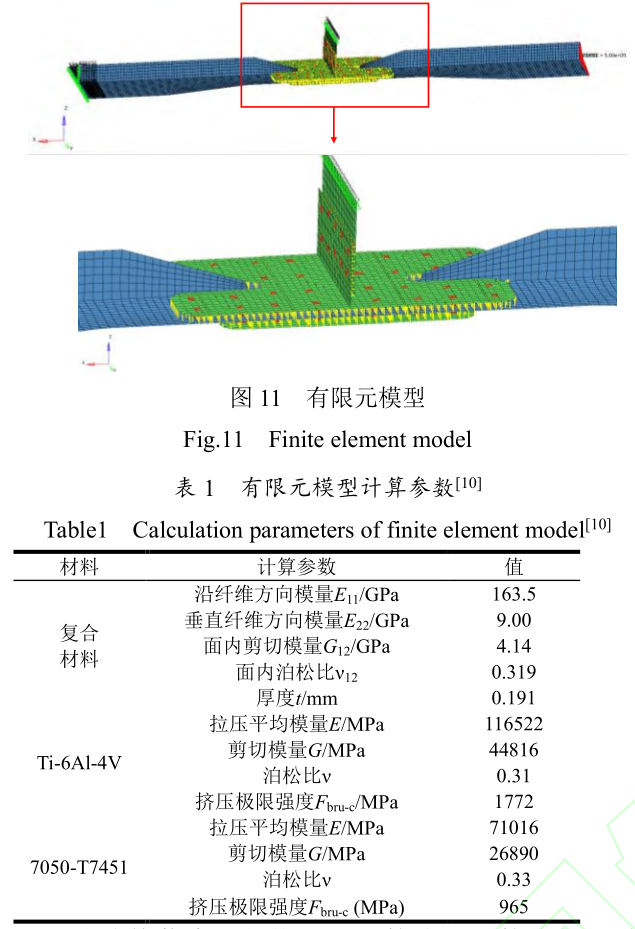
试验件蒙皮、长桁、三叉接头、对接带板、肋腹板假件及夹具均采用壳单元进行模拟,螺栓采用CBUSH 单元模拟,CBUSH 单元与壳单元通过 RBE3单元连接。CBUSH 拉伸刚度采用公式(1)计算:
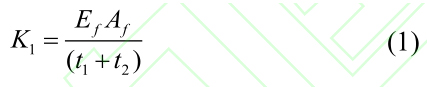
CBUSH 剪切刚度K2 、K3 采用公式(2)计算:

式(1)-(2)中: t1,t2为被连接件厚度,当双剪时t2为中间板厚度; d 为钉的直径; ,a b 是钉的连接类型系数,对于复材结构 a=2/3,b=4.2; n 是与钉的剪切形式相关,单剪时n=1,双剪时n=2;E1,E2是层板的等效弹性模量;Ef、
Af 分别是紧固件的弹性模量和截面积。
CBUSH 扭转刚度K4 取 100 N/mm,转动刚度K5、K6 取 109 N/mm。
使用点对面的 CGAP 单元模拟部件间的接触作用,CGAP 单元的轴向刚度定义为 1010 N/mm,摩擦系数定义为 0。
试验件夹持端约束 UX、UY、UZ,加载端约束UY、UZ,肋假件约束 UZ。参考点与加载端之间通过 RBE2 单元绑定,并在参考点施加 X 方向载荷,用于模拟试验加载。
3.2 计算与试验结果对比
有限元分析应变与试验监测应变对比如图 12 所示,两者误差基本在±10%以内,表明有限元模型可较为准确的反映试验件的传载和受力分布。
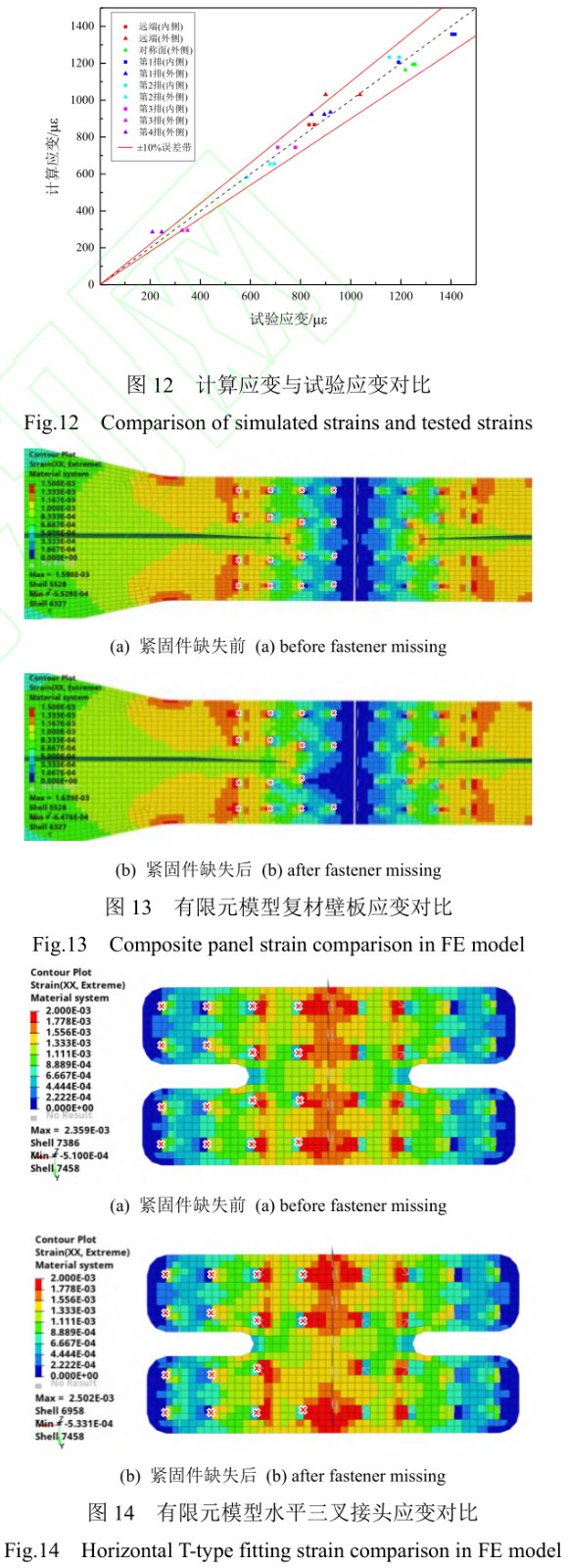
复材壁板、水平三叉接头、对接带板在紧固件缺失前、紧固件缺失后的应变分布分别如图 13-图 15所示。
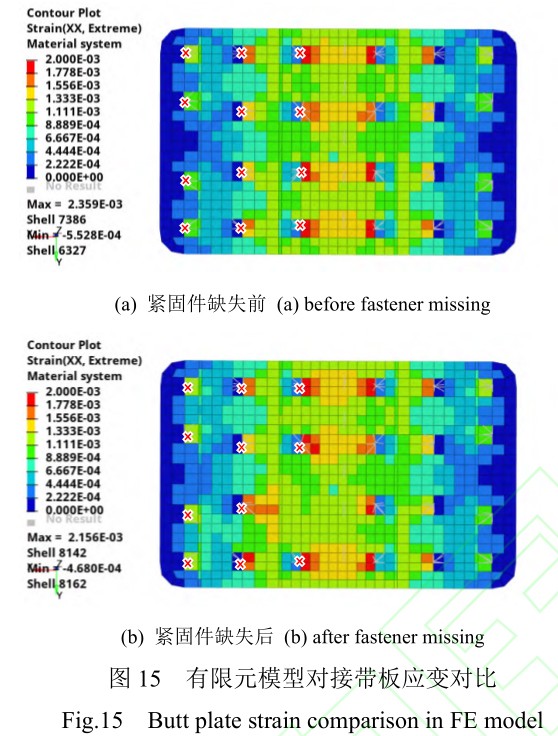
3.3 紧固件缺失对钉载影响
采用有限元模型开展紧固件缺失对钉载的影响规律研究。有限元计算得到的第 1-4 排紧固件载荷对比分别如图 16 所示。编号 1-3 紧固件缺失后,导致其它紧固件钉载均有所增大,特别是靠近缺失紧固件附近,钉载显著提高。图 16 中编号 1-4 紧固件钉载增大约 15%,编号 2-3 紧固件钉载增大约 18%,编号 2-4 紧固件钉载增大约 15%,编号 3-3、3-4 紧固件钉载增大约 12%,其它紧固件钉载增大均在5%-10%之间。
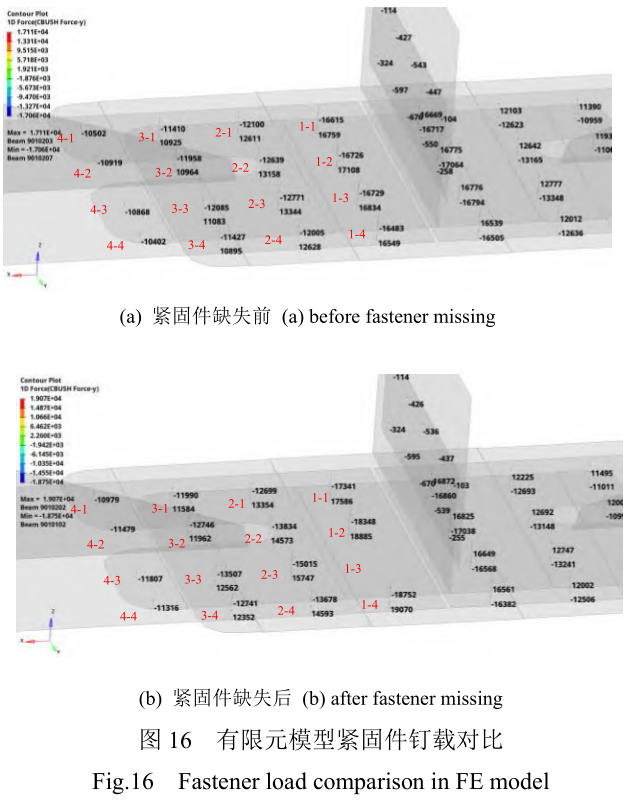
对有限元计算结果中每排紧固件钉载进行汇总,紧固件缺失前、紧固件缺失后传载对比如表 2所示。紧固件缺失后,对各排紧固件的传载有显著影响,第 1 排紧固件传载显著下降,第 2、3 排紧固件传载增大 10%-13%,第 4 排紧固件传载略有上升。计算连接部件传递总载表明,关键紧固件缺失对水平三叉接头、对接带板的载荷分配基本未产生影响。
在民机复合材料翼根连接结构设计中,可见紧固件缺失后,紧固件钉载变化规律与试验件应变变化规律类似,需重点校核缺失紧固件附近区域的裕度是否满足设计要求。
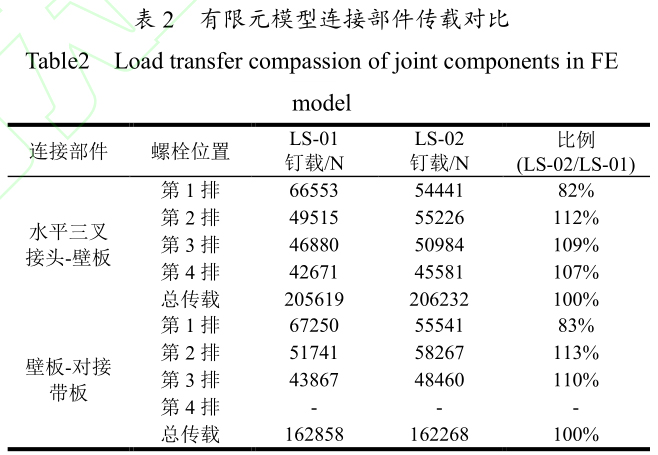
4 、结论
通过试验、仿真相结合的方法研究了关键紧固件缺失对试验件连接刚度、应变分布、钉载分配的影响规律,主要取得以下结论:
1)试验件紧固件缺失前、后试验件的载荷-位移曲线基本重合,表明关键紧固件缺失不会对翼根结构的连接刚度产生显著影响。
2)试验应变监测表明,关键紧固件(位于第 1排)缺失后,第 1 排紧固件位置的应变片数值变化在 5%以内,第 2-4 排靠近缺失紧固件位置的应变片数值显著提高,最大分别提高 22.1%、13.4%、9.1%。
3)有限元计算应变与试验监测应变的误差基本在±10%以内。有限元分析表明,第 1-3 排靠近缺失紧固件位置的钉载显著提高,最大分别提高约 15%、18%、12%,其它紧固件钉载提高均在 5%-10%之间。
关键紧固件缺失对水平三叉接头、对接带板的载荷分配基本未产生影响。
参考文献
[1] 杜善义,关志东.我国大型客机先进复合材料技术应对策略思考[J].复合材料学报,2008(1):1-10.
[2] SOLOSHENKO V. Conceptual design of civil airplane composite wingbox structures[C] // International Council of Aeronautical Sciences –ICAS. 29th Congress of the International Council of the Aeronautical Sciences. St. Petersburg, Russia: Curran Associates, Inc. 2014:2427-2436.
[3] 张绪,汪厚冰,于振波,等.复合材料机身壁板机械连接的强度分析与验证[J].玻璃钢/复合材料,2019(7):85-91.
[4] 梁乐乐,杨胜春,宋贵宾,等.复合材料机械连接强度分析研究[J].塑料工业,2022,50(3):90-94.
[5] 邵家儒,刘牛,曾宪君,等.复合材料机翼结构力学分析及连接设计[J].重庆理工大学学报(自然科学),2020,34(10):126-133.
[6] 李玺,李亚智,磨承杰,等.基于连续损伤力学的复合材料多钉连接失效分析和试验研究[J].机械强度,2022,44(4):911-920.
[7] ZHANG F, ZHANG W, HU Z D, et al. Experimental and numerical analysis of the mechanical behaviors of large scale composite C-Beams fastened with multi-bolt joints under four-point bending load[J].Composites Part B, 2019, 164: 168–178.
[8] KILIMTZIDIS S, GIANNAROS E, KOTZAKOLIOS A, et al. Modeling,analysis and validation of the structural response of a large-scale composite wing by ground testing[J]. Composite Structures, 2023, 312:1-23.
[9] SASIKUMAR A, GUERRERO J M, QUINTANAS-COROMINAS A, et al. Numerical study to understand thermo-mechanical effects on a composite-aluminium hybrid bolted joint[J]. Composite Structures, 2021,275: 1-12.
[10] ZHANG F, HU Z D, GAO L M, et al. Investigation on In-plane Shear Behavior of Large-Size Composite Plates with Multi-bolt Joints[J].Composite Structures, 2020, 232: 1-13.
[11] 秦杰,高伟,陈林霜,等.宽体客机复合材料加筋板根部对接分离面设计[J].西安航空学院学报,2023,41(1):12-17.
[12] 吴承思.复合材料蒙皮纵向连接结构在拉剪载荷下破坏研究[J].机械设计与制造工程,2022,51(9):17-21.
[13] 雷凯,王彬文,成竹,等.飞机多钉壁板混合结构热应力分析与验证[J].应用力学学报,2023,40(1):40-47.
[14] 贾宝惠,方嘉晨,武涛,等.预紧力影响下的复合材料螺接连接件失效安全 性 分 析[J]. 机 械 科 学 与 技 术 :1-12[2023-08-27].https://doi.org/10.13433/j.cnki.1003-8728.20230261.
[15] 汤平 . 两种民用飞机翼身对接结构比较分析[J].航空制造技术,2018,61(13):28-34.
[16] 周广洲 .波音737飞机紧固件缺失的放行[J]. 航空制造技术,2016,1/2:151-153.
相关链接