钛合金是以Ti为主要成分的合金,并含铝、钒、铁和锰等元素以提高其性能。根据相组成不同,钛合金可分为α钛合金、β钛合金和α–β钛合金。其中α–β钛合金(如Ti–6Al–4V)综合性能良好,应用最为广泛。
钛合金被认为是“轻质、高强、耐热”材料的典型代表。它的强度高于钢,密度却仅约为其60%,并可长期服役于300~350℃的温度环境,加之不同型号钛合金展现出的在成形和焊接等方面的工艺特点,使钛合金广泛应用于工程领域。最具代表性的是航空航天领域:航空发动机的风扇叶片和低压压气机/部分高压压气机的叶片/叶轮/叶盘/机匣、航天飞行器的燃料储箱和火箭发动机的外壳等重要零部件多采用钛合金制造。在汽车行业,采用钛合金制成的发动机气门/连杆和排气系统等零部件对车身减重、发动机降噪具有重要意义。得益于突出的生物相容性,钛合金也成为人体植入物和骨骼修复的首选金属材料。
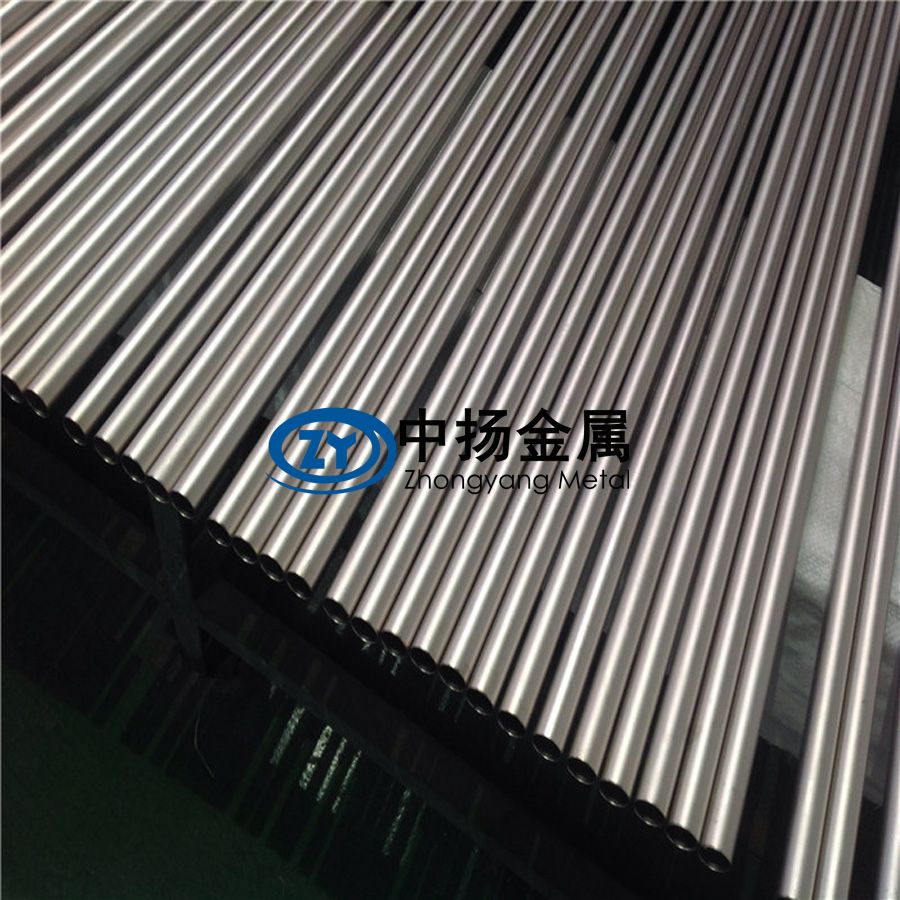
然而,由于强度高、导热系数低和化学活性高等特点,钛合金的机械加工难度较大,面临加工效率低、工具磨损快、加工质量差等问题。中外学者对此展开了一系列研究,探讨了各典型工艺条件下的钛合金切/磨削加工特点以及各类工具的应用效果等。通过这些研究,已基本可以形成对钛合金切/磨削加工特点的较为全面和深入的了解。本文将结合上述方面分析钛合金的切/磨削研究进展。
1、钛合金切削/磨削加工存在的主要问题
(1)切/磨削温度高。钛合金的强度高、热强性好,因此在切/磨削过程中会产生大量热量。然而,钛合金的热导率(低于7W/(m·K))远低于钢和铝合金的;在切/磨削过程中,除部分热量可通过切/磨屑、切削液和刀具/磨具传导外,其余热量中仅少数可及时传导至工件内部,导致大量切/磨削热聚积在接触区。这一方面加快了工具磨损速度,另一方面使工件表面热影响层变厚,降低零件的力学性能。有时不得不降低加工效率以减弱聚积热量的不利影响。
(2)工件材料弹性变形大。钛合金的弹性模量较低,因此在其切/磨削过程中弹性变形较大,制约了加工精度特别是薄壁件加工精度。此外,工件材料的弹性变形和恢复是切削振动的重要诱因。工件材料弹性变形大,则工件材料和刀具/磨粒的接触面积增大,导致刀具/磨粒的后刀面磨损严重。
(3)工具黏附现象严重。钛合金的塑性良好,切削刃和工件材料在接触压强的作用下易产生“冷焊”现象,造成工件材料黏附。另外,钛合金的化学活性高,钛元素在切/磨削温度的作用下易与工具材料中的碳、氮等元素以及空气中的氧元素等发生化学反应,加剧工具与工件材料之间的黏附倾向。黏附的工件材料在剥离时会导致少量刀具/磨粒材料一同脱落。严重的黏附现象是导致切/磨削加工钛合金时工具磨损快的主要原因之一。
2、钛合金切削加工技术研究进展
2.1钛合金的切削加工性
在相同工艺条件下(切削速度100~180m/min,干切),Ti–6Al–4V和正火45钢的车削加工的主切削力相当,前者对应的径向切削力高15%~30%,切削温度(700~800℃)高约7%。相比之下,湿式切削(5%的乳化液)可使切削力降低约10%,切削温度降低约5%,同时表面质量也得以改善。
为获得良好的表面完整性,应合理选择切削用量。总体而言,切削速度越高,表面硬化越严重;进给速度则对硬化程度无显著影响。切削速度、切深和进给速度的增大均可导致表面粗糙度增大。切削表面易产生一定程度的残余拉应力,亚表面则多为残余压应力;增大进给和切深,表面的拉应力水平和亚表面的压应力水平越高。出于切削温度考虑,一般应选用较低的切削速度和较大的切深,同时选用适配的切削液。
2.2钛合金切削刀具选择
切削高温等引起的刀具快速磨损是钛合金切削过程存在的主要问题。因此,开发钛合金切削专用的高性能刀具是未来需要研究的重要课题。
加工钛合金时,涂层硬质合金刀具和聚晶金刚石(PCD)刀具显示出优异的切削性能,尤以PCD刀具为最佳;聚晶立方氮化硼(PCBN)刀具次之;TiC基硬质合金刀具和陶瓷刀具因耐用度低等原因被认为不适用于钛合金切削加工。PCD刀具与钛合金切削的高匹配性主要源自其良好的导热性和极高的硬度:金刚石的导热系数为硬质合金的数倍,更多切削热可通过刀具传导出切削区;极高的硬度则保证了刀具的耐磨性。
采用PCD刀具切削钛合金的刀具耐用度可达硬质合金刀具的数十倍。未来应从刀具制备(焊接、切割和刃磨等)和切削工艺优选(切削用量选择和切削液供给等)等方面入手,降低PCD刀具切削钛合金的刀具成本,进一步扩大其应用范围。
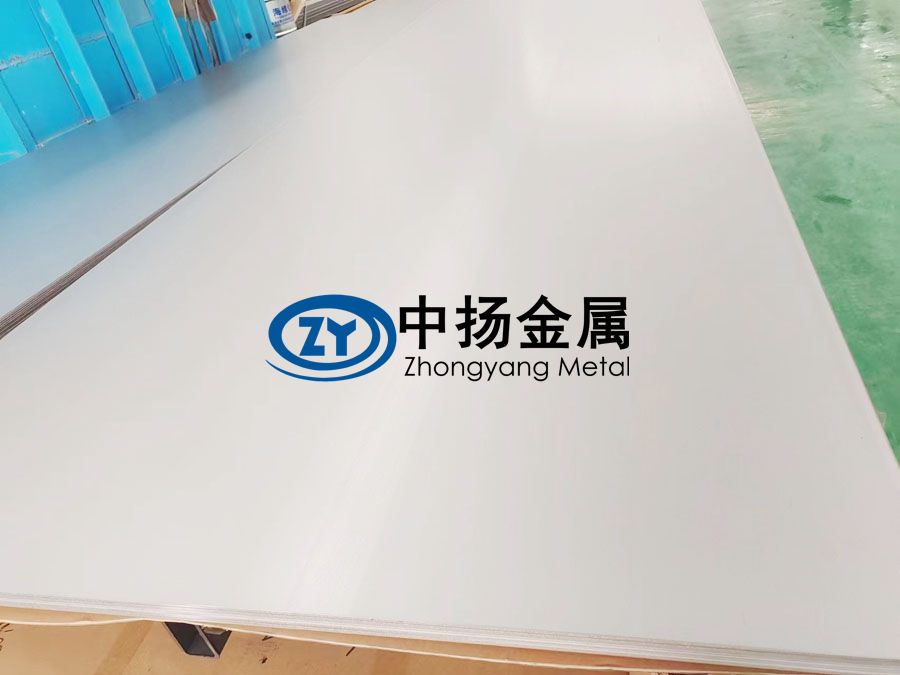
刀具角度方面,一般选择较小的前角切削钛合金,以增大切屑与前刀面的接触长度;同时选择较大的后角,以减小后刀面与加工表面之间的摩擦。
2.3钛合金高速切削技术
高速切削的主要特征是在常规切削的基础上大幅提高切削速度。“高速”是一个相对概念,具体值取决于工件材料的力学性能等。对钛合金而言,一般切削速度超过100m/min即可认定为高速切削。高速切削具有以下优势:
(1)加工效率高。高速切削一般同时采用高主轴转速和快进给速度,从而使材料去除率成倍提高,最高可达常规切削的5倍甚至更高。
(2)可提高工件表面质量和加工精度。高速切削时,由于剪切变形区变窄等因素,切削力小于常规切削时的切削力,有利于保证零件尤其是薄壁件的加工精度;同时,大部分切削热被切屑带走,传入工件的热量比例较低,有助于提高其表面质量和加工精度。
(3)刀具相对寿命长。在高速切削条件下,虽然刀具的使用时长有所下降,但切削效率的提升更为明显,即等量的刀具磨损可完成更多的切削任务。换言之,刀具的相对寿命得到提升。
(4)高切削速度条件下,切削过程产热增多。这对机床的冷却系统以及刀具的耐磨性和热强性等是一个挑战。此外,高速切削还要求机床具有较高的刚度和精度等,以充分发挥其工艺优势。目前美、日、德等国在上述方面的发展水平处于领先位置。
3、钛合金磨削加工技术研究进展
3.1钛合金的磨削加工性
磨削温度高、磨削力大是钛合金磨削加工的显著特点。在普通磨削条件下,Ti–6Al–4V对应的磨削力约为45钢的1.5~2倍,磨削温度高约20%~30%,即使采用导热性好的CBN磨料,磨削温度亦高达400℃。若采用缓进深切工艺磨削钛合金,切削液难以充分冷却整个磨削弧区,应格外注意磨削温度控制。
不同于切削,磨削依靠众多磨刃的微切削作用去除材料,并且为负前角切削,因此工件材料在磨粒的挤压和切削等作用下变形较为剧烈,导致磨削表面往往存在较为严重的鱼鳞状涂覆等现象。提高磨削速度可通过降低单颗磨粒切厚显著改善这一问题。在普通磨削条件下,由于磨削温度较高,磨削后工件表层多为残余拉应力。例如,采用SiC砂轮在普通磨削条件下加工Ti–6Al–4V时,磨削表面的残余拉应力高达500MPa以上。若采用缓进深切磨削工艺,正常磨削时弧区温度仅约为100℃。此时磨削力在残余应力的形成过程中起主导作用,因此表面多为残余压应力。
3.2钛合金磨削砂轮选择
在普通磨料中,SiC磨料与钛合金间的亲和性较低,因此其磨削效果优于刚玉磨料的。若采用刚玉磨料磨削钛合金,为避免砂轮表面产生大规模的材料黏附,须将磨削速度控制在约10m/s。在现有磨具技术水平下,普通砂轮磨削钛合金时砂轮磨损速度较快。
例如,采用SiC砂轮在普通磨削条件下加工钛合金的磨削比仅约为1。选用超硬砂轮时则提升几十甚至上百倍。此外,相对于普通磨料,超硬磨料的导热能力显著增强,因此可以获得较高的材料去除率。另一方面,采用超硬砂轮磨削钛合金时可以避免频繁地修整砂轮,进一步提高磨削加工效率。
即便如此,在工程实践中,仍多采用普通砂轮加工钛合金。制约超硬砂轮广泛应用的原因主要有:(1)砂轮价格昂贵,导致加工成本显著高于用普通磨料砂轮磨削的成本;(2)砂轮修整难度大。因此,后续研究可重点关注超硬砂轮的制备与修整技术。
3.3钛合金磨削温度控制技术
磨削高温是抑制钛合金磨削加工效率的重要原因。对此研究人员从开发新型磨具和改善冷却方式等方面进行了一系列研究,取得了显著效果。
南京航空航天大学徐九华团队将超硬磨料钎焊技术与磨粒有序排布技术相结合,开发出磨粒有序排布钎焊CBN砂轮。该种砂轮磨粒出露高,可提供充足的容屑空间,从而减少磨削(特别是高效磨削)过程中砂轮与工件之间的摩擦。在此基础上进一步开发了开槽钎焊CBN砂轮,可使更多切削液进入磨削弧区。该型砂轮在降低钛合金磨削温度方面显示出明显优势,在大切深的磨削条件下该优势更为明显。在改善冷却方面,主要有热管砂轮技术、低温冷风技术和径向水射流技术等。例如,热管砂轮技术基于内冷却的角度实现对磨削弧区的强化换热,弧区热量经热管迅速疏导,以达到少用或不用切削液的目的;在微量润滑磨削时采用低温冷风技术,可以显著改善磨削弧区的换热状况,同时可以降低砂轮黏附程度。
4、TiAl合金切削/磨削加工技术研究进展
TiAl合金是一类特殊的高温钛合金。它的服役温度比普通钛合金的服役温度高200℃以上,因此拥有广阔的应用前景。TiAl合金共有4种形态:
α2–Ti3Al、γ–TiAl、TiAl3和Ti2AlNb;其中,γ–TiAl因优异的综合性能得到了广泛研究。针对该合金的制备方法和材料特性的研究已较为成熟,针对其切/磨削性能有若干研究,现结合其主要材料特点介绍如下。
与普通钛合金相比,γ–TiAl的塑性较差(室温延伸率≤2%)。因此,在其切削加工过程中,局部材料可能发生脆性断裂,在切削表面形成材料剥离和裂纹。根据车削表面的材料剥离和裂纹的形态推测,层片状显微结构是引起上述表面缺陷的内因:片状晶粒之间的晶界在切削力热的耦合作用下萌生微裂纹并延伸至一定深度,最终导致局部材料被从工件表层“拔出”。
磨削的单颗磨粒切厚远小于切削加工的切厚,磨削表面不存在严重的材料剥离和裂纹现象。另外,γ–TiAl的强度低于普通钛合金的,并且由于铝元素含量较高(原子数占比一般为42%~48%),材料的导热系数有所提升。这对于其切/磨削加工性而言是利好因素。例如,在同一磨削用量水平下磨削加工γ–TiAl和Ti–6Al–4V,前者的磨削比能低,磨削比也显著更高。5钛基复合材料切削/磨削加工技术研究进展钛基复合材料是指在纯钛或钛合金中添加/原位生成硬质增强相而形成的金属基复合材料,在某些应用场合也称为高温钛合金材料。它具有比普通钛合金更高的强度、比模量和更好的抗蠕变性能等,未来有望在航空工业、汽车、船舶等领域获得广泛应用。
针对钛基复合材料切/磨削加工的研究,多集中于拥有良好综合性能的原位生成颗粒增强(TiC等)的Ti–6Al–4V基复合材料。结果表明,材料强度的提高以及增强相的存在提高了钛基复合材料的切/磨削加工难度。用PCD刀具切削钛基复合材料时,刀具磨粒磨损严重;切削Ti–6Al–4V时刀具则以黏结磨损和扩散磨损为主。这可导致刀具耐用度相差数倍甚至数十倍。磨削时,钛基复合材料对应的磨削力高10%~20%,磨削温度高约10%。
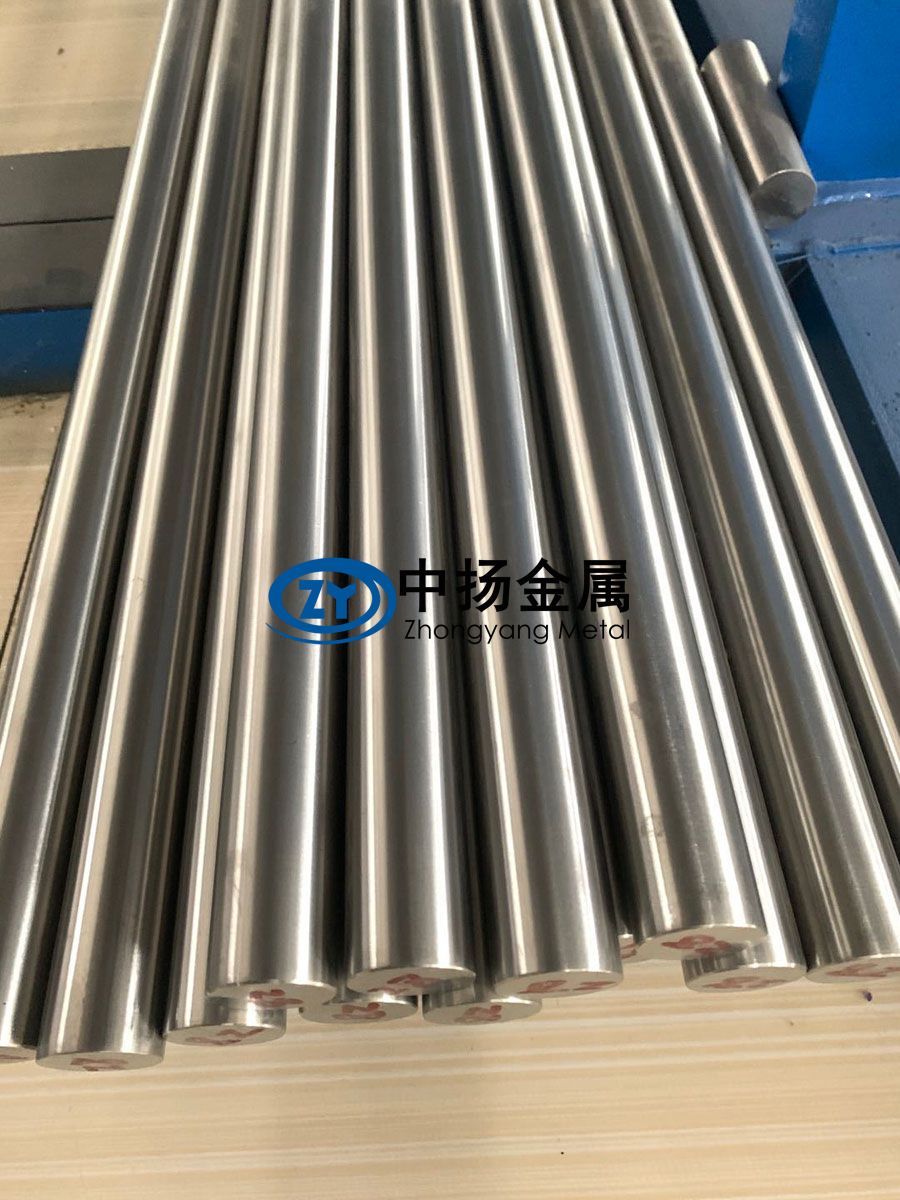
不同于铝基复合材料,限于当前材料制备技术的发展水平,已有研究涉及的钛基复合材料增强相体积分数集中于5%~10%。增强相体积分数对材料的切/磨削加工性能存在显著影响,体积分数越高,切/磨削加工难度越大。因此,在实际应用中,应结合服役环境对材料性能的要求和切/磨削加工成本等因素综合考虑,做出合理的材料选型。
6、本期论文点评
不同CBN砂轮高速加工PTMCs的磨削性能对比李征,等;第5页
钛基复合材料比钛合金强度高且可长期服役于500℃的高温环境,有望在航空发动机重要零部件制造方面获得广泛应用。作为兼顾高强韧性与高硬度的难加工材料,加工性能差是制约其应用的重要原因。本文聚焦于钛基复合材料磨削加工性的表征,从磨削力、磨削温度和表面质量等方面描述了陶瓷CBN砂轮、电镀CBN砂轮和钎焊CBN砂轮磨削该材料的难易程度。文章选题具有较强的工程应用价值。论文总结了砂轮种类和磨削用量对磨削结果的影响,并对其作用机制进行了合理分析;研究结论可为钛基复合
材料磨削加工的砂轮优化和工艺优化提供参考。在后续研究中,可重点关注以下方面:(1)磨削后表层材料的残余应力和显微硬度等方面的力学性能变化以及砂轮磨损形式和机理,完善钛基复合材料的磨削加工性表征;(2)开展钛基复合材料和钛合金的磨削加工对比研究,阐明硬质增强相对磨削加工过程的影响机制,为材料设计和加工性改善提供参考。
PCD刀具车削钛基复合材料刀具磨损的研究濮建飞,等;第11页
钛基复材在航空发动机和汽车发动机关键零部件制造等方面具有广阔应用前景。然而,优异的力学性能也导致其切削加工难度较大,其重要表现是刀具磨损速度快,导致加工成本较高。作者针对刀具磨损问题开展了试验研究,分析了PCD刀具切削钛基复材的刀具磨损形式与机理,讨论了硬脆增强相含量对刀具磨损的影响。研究获得的结论可为钛基复材切削刀具设计提供参考。特别地,作者探讨了增强相种类对刀具磨损的影响。这可从机械加工的角度为钛基复材的增强相选择提供参考。
刀具磨损是影响切削加工过程的重要因素。文章对刀具磨损的形式和机理作了详细介绍,但缺乏刀具磨损对切削过程的影响的分析。此外,作者在后续研究中可选用一定几何参数范围内的刀具进行切削,以阐明刀具前角、后角等重要参数对加工质量的影响,为刀具几何参数优化提供指导。
TiAl合金低压涡轮叶片榫头磨削温度场研究奚欣欣,等;第17页
TiAl合金的密度仅约为镍基高温合金密度的一半,服役温度达700℃以上,有望广泛应用于制造航空发动机的压气机和低压涡轮叶片等重要零件。相比普通钛合金,关于TiAl合金机械加工的研究尚不够深入。
磨削烧伤是制约该材料磨削加工效率的主要原因。在成形磨削时,工件各处磨削温度不一致;若采用试验的方法测温,需设置大量测温点,工作量大且成本较高。因此,本文选择采用有限元分析的手段进行温度场分析。文章报道了上述方法的重要细节,包括几何建模、边界条件设定和热源加载方法等,具有较强指导意义;研究获得的结论可为低压涡轮叶片榫头的磨削烧伤预测和磨削工艺优化提供参考。
不同于平面磨削,在成形磨削过程中,切削液对工件各处的冷却效果存在差异。在以后的研究中应将该点纳入考虑,以提高仿真条件与实际磨削过程的接近程度。此外,建议选用多种热源分布模型开展仿真,并对其结果差异及产生原因做详细解释,从而为成型磨削温度分布和烧伤预测奠定基础。
冷风微量润滑纳米粒子体积分数对钛合金磨削性能的影响王晓铭,等;第23页
磨削温度高是钛合金磨削加工过程中存在的主要问题之一。目前常用的降温方法是加大切削液供给,但对环境污染较为严重。若采用固体自润滑砂轮干式磨削,则存在磨屑不易排出的问题。微量润滑配合低温冷风可通过纳米粒子减摩等方式降低磨削温度;同时,压缩空气可在一定程度上避免因砂轮堵塞引起的工件表面质量恶化。本文中对冷风纳米粒子微量润滑磨削技术的降温效果及其作用机理进行了详细介绍,分析了纳米粒子的体积分数对磨削效果的影响等重要问题。研究结果可以为提高微量润滑磨削质量、扩展该方法的应用范围等提供参考。
文中缺乏对磨削后砂轮形貌的描述,以表明在此冷却润滑条件下的排屑情况。在后续研究中可拓宽磨削输入条件范围,如不同纳米粒子种类与几何参数、更高冷风供应压力和更大磨削用量,提高冷风纳米粒子微量润滑磨削的材料去除率、改善磨削表面质量。
颗粒增强钛基复合材料车削试验研究霍福松,等;第30页
相比钛合金,钛基复合材料比模量高,耐磨性和抗蠕变性能好,有望广泛应用于航空航天和汽车船舶等行业。但添加硬质增强相也导致其切削加工难度更高。作者针对这一问题展开研究,具有一定的工程实践意义。本文从切削力、切削温度和切削表面粗糙度三方面评价了颗粒增强钛基复合材料的切削加工性,探讨了切削用量对上述加工性指标的影响规律,并在此基础上获得了最佳的切削用量范围。研究结论可为颗粒增强钛基复合材料的切削参数优选提供参考。
文章并未重点突出硬质增强相对钛基复合材料切削过程的影响,包括不同切削用量水平下增强相的去除形式和增强相对切屑形成过程的影响等。此外,高速切削具有效率高和刀具相对寿命长等优势。在后续研究中,作者可针对钛基复合材料的高速切削加工性开展研究,并以本文的普通切削为对比,阐述高速切削效果的优劣及其原因,以提高钛基复合材料的切削加工性能。
相关链接