工业纯钛在航空航天、舰船、核能等高科技领域均有广泛的用途[1-4]。众所周知,工业纯钛是一种滑移系较少、对称性较低的密排六方金属,在冷加工形变或热处理过程中极易形成织构。Bozzolo指出[5],材料性能20%~50%受织构影响,包括弹性模量、泊松比、强度、韧性、塑性、深冲性、磁性、电导、线膨胀系数等。材料力学性能的各向异性也极大受到基体织构的影响。
目前,大部分研究人员集中于研究钛的轧制织构和再结晶织构,而再结晶织构则主要集中于再结晶初始阶段的晶粒尺寸变化和初始织构的形成[6]。
Liu等[7]研究发现冷轧退火处理后的钛板具有较强的各向异性,经循环相变处理后,各向异性得到了明显降低,同时织构组成类型也发生了明显变化。张贵华等[8]研究冷轧钛板在不同温度退火后的织构变化,结果表明退火后材料发生再结晶形成典型的基面双峰TD织构,退火温度超过700℃时,轧制织构减弱,而再结晶织构增强。江先锋等[9]研究退火工艺对冷轧钛板再结晶织构和屈服强度的影响,结果表明,在650℃下,冷轧纯钛带退火后的再结晶织构主要是(0001)[2110]和(0001)[5610],遗传了纯钛带的冷轧织构。随退火保温时间的延长,织构的取向梯度均逐渐减小,组分和强度趋于稳定,且退火后纯钛带的屈服强度也比较稳定。镁合金与纯钛具有相同的晶体结构,研究者采用波纹异形模具开展镁合金弱化织构研究并取得一定成果。Wang等[10]利用波纹形状的模具将Mg-6Al-3Sn镁合金板轧制成一块波纹状板材,然后再轧平,结果发现这种工艺能够弱化镁合金基面织构。
Sun等[11]将Mg-3Al-1Zn平板切成两块波纹状的板材,再轧平,发现其原本强烈的基面织构发生了偏移。上述研究表明,通过将镁合金表面波纹化然后再轧平的方法能够弱化织构,但是对波纹辊轧制后的再结晶织构研究较少。
本文采用波纹型轧辊开展TA1纯钛轧制,通过对比波-平轧制和平-平轧制,借助扫描电子显微镜(SEM)和电子背散射衍射技术(EBSD)来探讨波纹辊轧制过程中循环波动载荷对钛板再结晶织构的影响,研究分析微观组织变化及织构类型和分布,为TA1的加工应用提供理论基础和技术支撑。
1、试验材料与方法
TA1纯钛板原始尺寸为80mm×60mm×4mm,其化学成分见表1。图1(a)为原始钛板的微观组织形貌,钛板初始晶粒尺寸为34μm,晶粒呈等轴状。

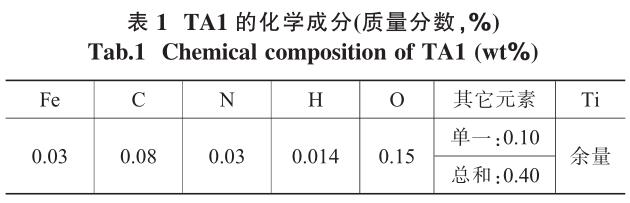
波-平轧制工艺(corrugatedandflatrolling,CFR)分为两道次,第1道次是对TA1钛板进行波纹辊粗轧(corrugatedrolling,CR),波纹辊采用的是准150mm的轧辊,波峰波谷的高度差为1mm。第2道次是平辊整平精轧(flatedrolling,FR),波纹辊粗轧示意图如图1(b)所示。利用管式加热炉将钛板在400℃保温20min,随后进行第1道次的波纹辊轧制,压下率为25%,获得上表面为波纹形状、下表面为平面的钛板,然后再回炉(400℃保温10min),进行第2道次平辊轧制,加热过程中通氩气保护,两道次总压下率为50%。在相同条件下进行两道次都为平轧的对比实验,称为平辊-平辊轧制工艺(flatedandflatedrolling,FFR)。将热轧后的钛板进行线切割,观察其RD-ND平面,该平面尺寸为10mm×2mm,然后将试样放入管式加热炉中于650℃保温1h,进行再结晶退火,保温过程中通氩气保护,最后空冷。
2、试验结果及讨论
2.1组织变化
分别对CFR第1道次波纹辊轧制和FFR第1道次平辊轧制得到的钛板进行观察,其微观组织形貌如图2所示,其中图2(a)~(c)为CFR第1道次轧制后钛板波峰厚度梯度上的三个位置组织,图2(d)~(f)为CFR第1道次轧制后钛板波谷厚度梯度上的三个位置组织,图2(g)~(i)为FFR第1道次轧制后钛板厚度梯度上的三个位置组织。波峰a位置晶粒变形较小,靠近波峰晶粒尺寸更大,且晶粒形貌基本呈现等轴状,并能观察到孪晶,晶粒呈现挤压拉长的特征。波峰b、c位置存在梯度变化,晶粒变形逐渐严重。波谷d位置的晶粒变形非常严重,几乎看不到明显的晶界,晶粒明显被拉长,波谷e~f位置晶粒变形较次之,能看到晶粒发生挤压破碎,有孪晶产生。相对于波纹辊轧制,平轧后的晶粒形貌在板材厚度方向差距不大。可以看出,波纹辊轧制(CR)后晶粒形态在厚度和轧制方向有一定差异,而平轧后晶粒形貌在轧制方向和厚度方向无显著差异。
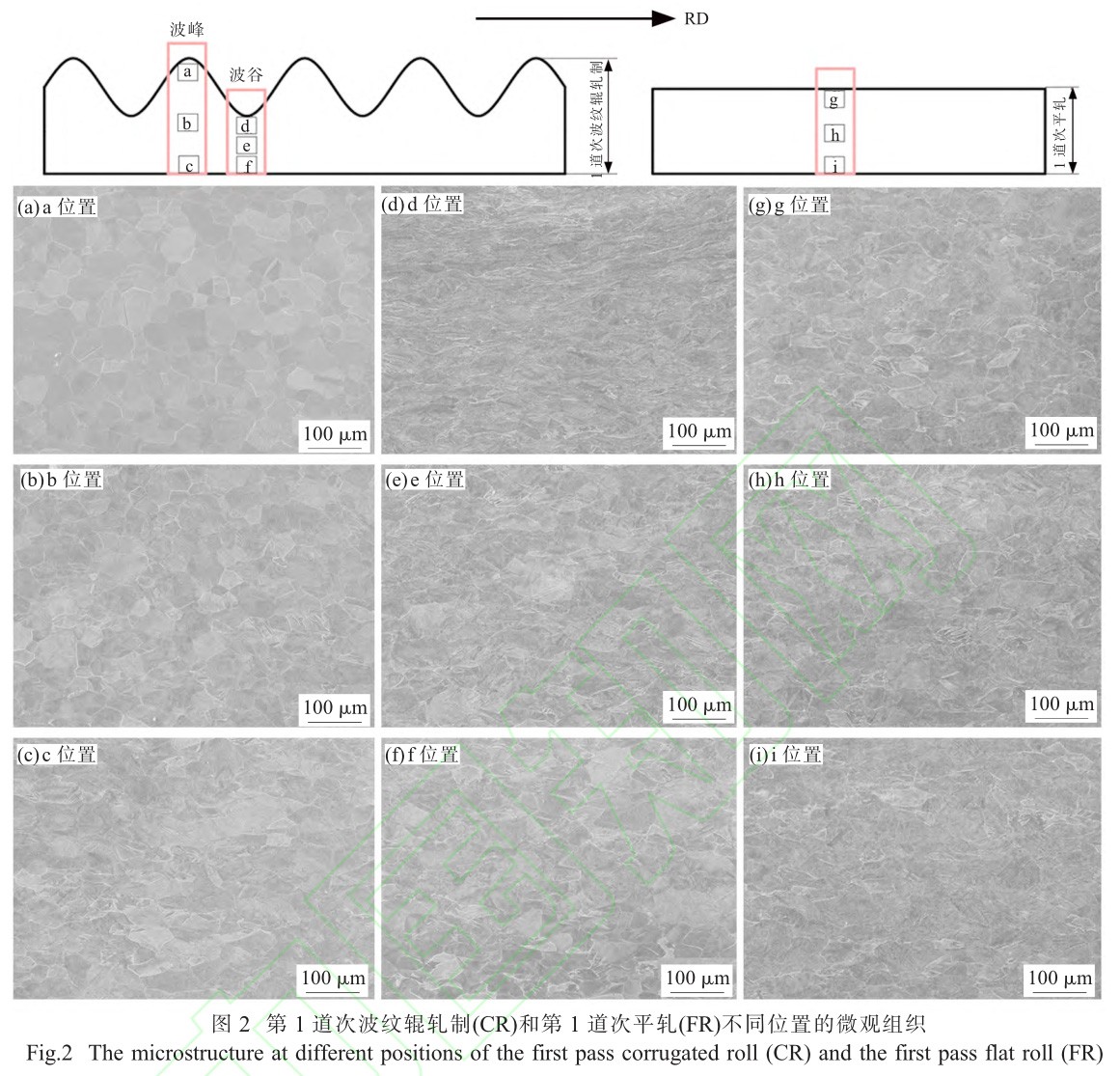
图3为经过CFR和FFR第2道次平轧后钛板的微观组织形貌。图3(a)~(c)对应CFR钛板原波峰位置组织,图3(d)~(f)对应CFR钛板原波谷位置组织,图3(g)~(i)则为FFR钛板厚度方向的上中下三个位置组织。可以观察到原波峰a位置晶粒破碎及孪晶的产生,晶粒发生了动态回复,晶界依旧明显。而原波峰b、c位置晶粒变形严重,变形程度沿厚度方向递增。从原波谷d位置发现靠近原波谷区域晶粒变形更为剧烈,而远离波谷区域变形减弱。原波峰e、f位置晶粒变形程度较原波峰d位置较小,晶粒破碎拉长,变形程度不及d位置。FFR钛板厚度方向的g、i位置的晶粒差异较小,晶粒发生一定程度的破碎拉长,较h位置的晶粒变形更为严重。
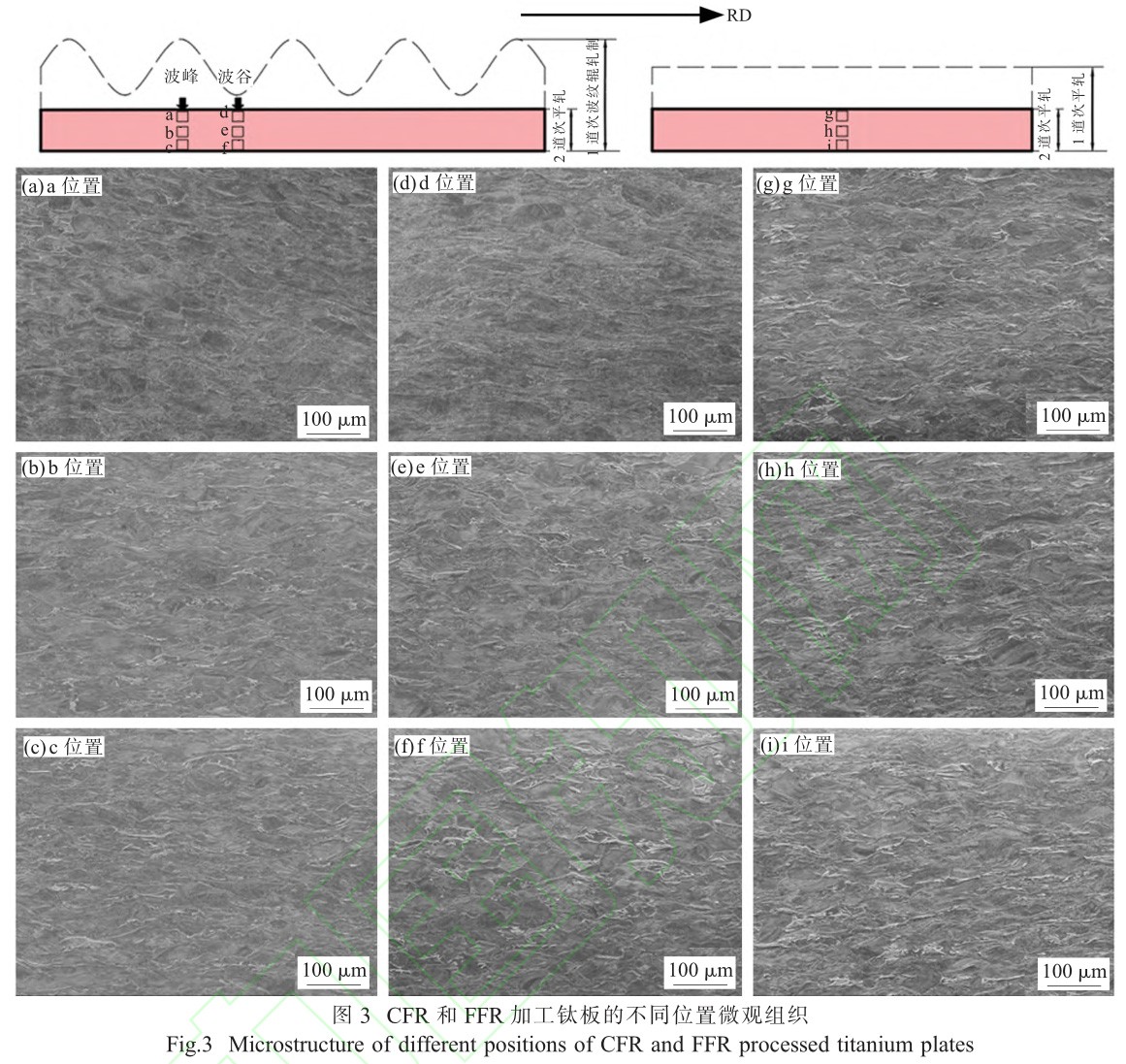
通过对钛板的微观组织观察,发现经过波纹辊轧制后,板材在RD和ND两个方向上都存在微观组织差别,说明CFR工艺能够促使钛板组织变形多样化。这归因于波纹辊轧制过程中应力和应变的大小及方向是波动变化的,而平轧过程相对稳定[10]。
图4为CFR和FFR工艺制备的钛板在650℃下退火1h不同位置的反极图(彩图见电子版,下同)。图4(a)~(c)为CFR钛板原波峰厚度方向的反极图,图4(d)~(f)为CFR钛板原波谷厚度方向的反极图,图4(g)~(i)为FFR钛板厚度方向的反极图。从图中可以看出,经过650℃保温1h处理后,两种工艺的轧制组织均发生了再结晶,晶粒呈现等轴状。表2为平均晶粒尺寸统计结果,从表中可以看出,CFR钛板的晶粒尺寸大于FFR钛板。分别采用横向截线法和纵向截线法测量晶粒尺寸,发现相较于FFR钛板,CFR钛板晶粒的横向尺寸比纵向小,说明CFR钛板的再结晶晶粒更加容易沿ND方向生长,这归因于波纹辊轧制过程中金属流动的特点,CFR钛板近上表面的应变更大[12],在退火过程中促进再结晶晶粒沿ND方向生长。
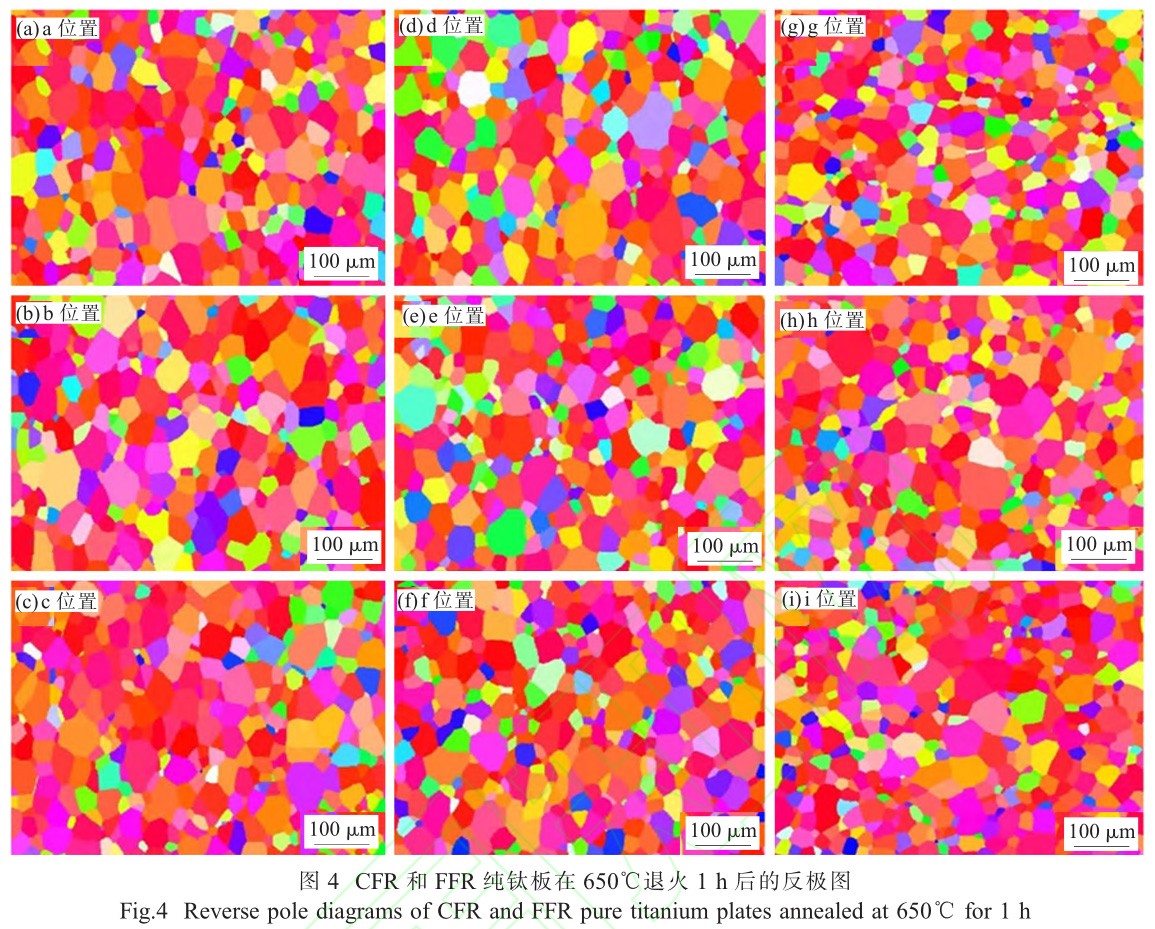
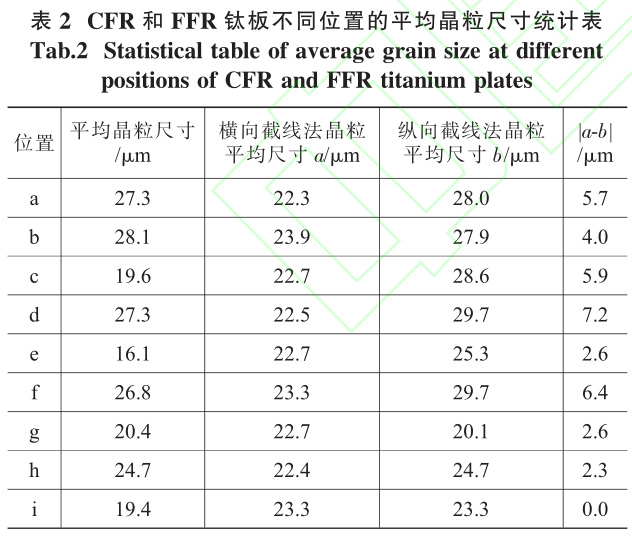
经过轧制退火后的钛板再结晶比例如图5所示。钛板在650℃保温1h处理后都基本完全再结晶,但是波谷位置的亚结构明显要比其它位置的多,尤其是e位置(CFR),相比于原波峰b位置(CFR)和FFR的h位置要大两倍以上,且再结晶比例低。这说明波谷中间区域的再结晶启动较晚,CFR钛板的其它位置优先形成再结晶晶核并长大。
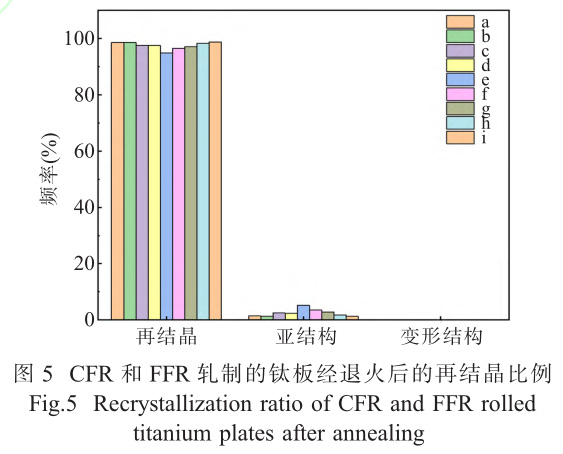
2.2织构演变
图6为CFR和FFR工艺制备的钛板在650℃退火1h后RD-ND面的{0001}极图。原波峰位置a~c的极图最大极密度强度分别为7.50、6.41、10.95。原波谷位置d~f的最大极密度强度分别为7.49、4.97、9.42。FFR钛板退火后厚度方向极图(图6(g)~(i))的最大极密度强度为8.54、10.46、9.70。从图中可以发现,FFR钛板中间区域织构强度较小,两端织构强度较大;且靠近上表面a和d位置的织构强度都分别小于c和f位置的。与FFR轧制相比,CFR钛板近上表面和中间位置的织构呈现一定程度弱化,但是近下表面的织构强度与平轧相近,这表明波纹辊轧制后晶粒旋转变形的差异导致了钛板的织构梯度,近波纹表面区域的织构呈现弱化特征。从a、b、d、e位置的极图看出CFR钛板极密度强点多达4个以上,且在TD方向分散分布,而平轧区域的极密度强点在两个以下,这表明波纹辊轧制能够造成织构分散,从而弱化轧制织构。对于CFR轧制下表面区域c和f位置极图的极密度强点少,织构强度较大,接近平轧工艺,这说明波纹辊轧制对下表面织构的影响较小。
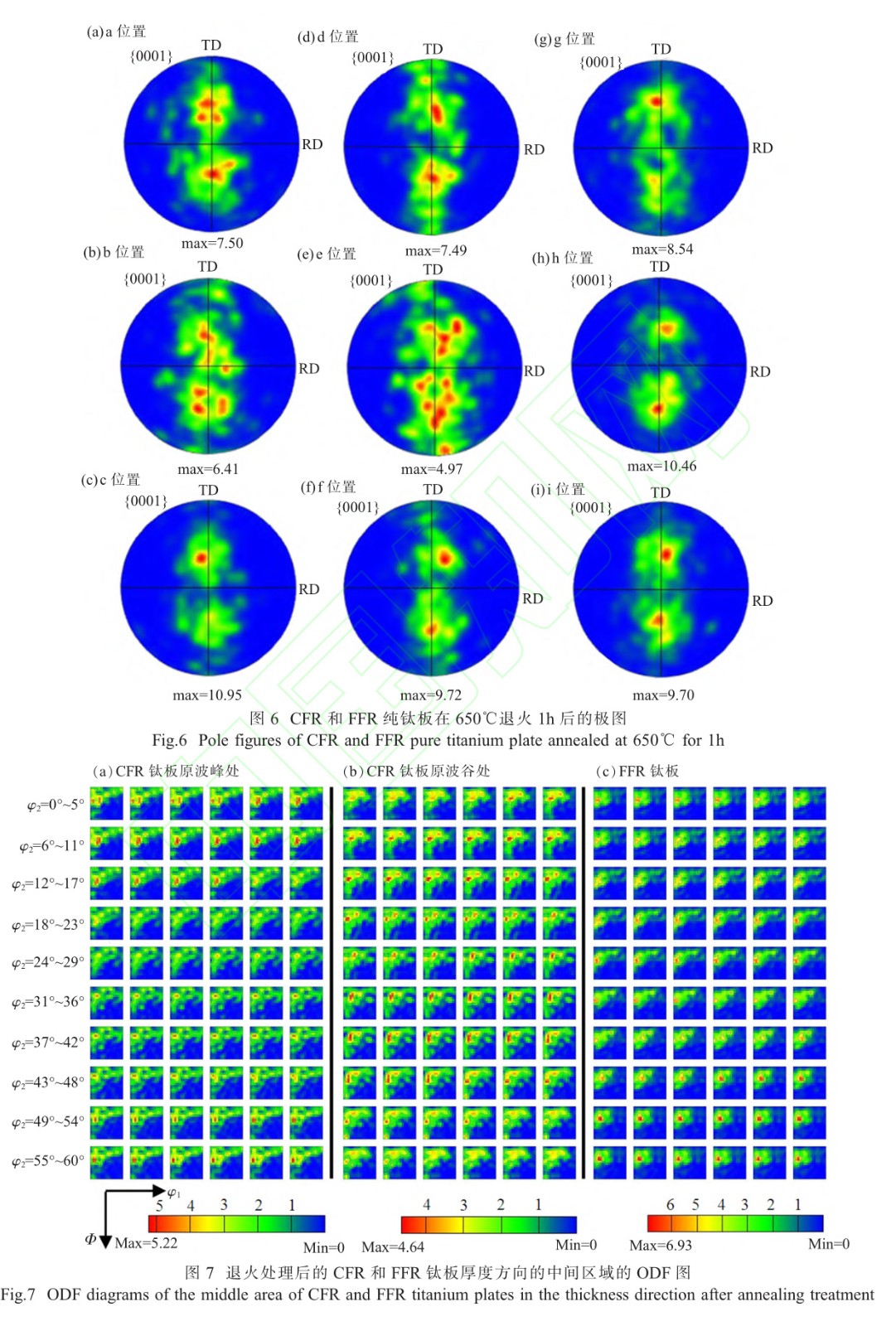
通过{0001}极图可以发现CFR轧制退火处理后织构弱化现象,其再结晶晶粒c轴由ND向TD方向偏转并且在多个位置聚集,织构类型依旧是双峰TD型织构。近上表面位置的极密度强区较为分散,近底面更为集中。通过极图无法对织构进行定量分析,只能停留在定性甚至半定性的水平上,但是可以使用取向分布函数(ODF)对轧制织构进行定量分析[13]。图7(a)为CFR原波峰厚度方向中间区域的φ2的ODF截面图,图7(b)为原波谷厚度方向中间区域的φ2的ODF截面图,图7(c)FFR钛板厚度方向中间区域的φ2的ODF截面图,φ2角度范围0°~60°,截面图之间间隔1°。图7(a)中织构强度最大为5.22,用欧拉角表示为(10°,35°,60°)和(20°,40°,10°),具有织构强点的φ2截面图有46个区域,占比76.7%;图7(b)位置的织构用欧拉角表示为(15°,30°,15°)和(20°,25°,35°),最大织构强度为4.64,织构强点分布较为分散,共47个区域,占比78.3%;图7(c)位置的织构强度最大为6.93,其织构用欧拉角可表示为(20°,35°,50°)和(10°,35°,25°),织构强点集中于共22个区域,占比26.7%。观察到CFR钛板的织构与典型的冷轧织构{1125}<1100>相近[14],江先锋等[9]研究表明纯钛再结晶织构也遗传了冷轧织构。这意味着不论是CFR还是FFR加工退火后,其织构类型是相近的,但是CFR加工退火后织构更为分散,在极图上表现为TD方向上出现更多的极密度强区,但依旧是基面双峰TD织构,如图6所示。
这说明经过波纹辊轧制后,在波动载荷的作用下不同位置处的晶粒发生不均匀变形且受力方向发生周期性变化,在随后退火过程中生成的再结晶晶粒取向更多样化,导致CFR钛板再结晶晶粒取向较FFR钛板更分散,{0001}极图上表现出极密度强区多且分散,最终达到弱化织构这一目的。
3、结论
(1)经过波纹辊轧制后,钛板波峰和波谷位置的显微组织差异较大,波峰处晶粒粗大,波谷处的晶粒变形严重。此外,板材ND方向的组织有渐进性变化特点,板材近表面区域显微组织变形相较于板材厚度方向的中间区域更严重。
(2)经650℃保温1h退火后,相较于FFR钛板,CFR钛板再结晶晶粒尺寸较大,且再结晶晶粒易于沿ND方向生长。
(3)退火后CFR钛板织构更为分散,在极图上表现为TD轴上的极密度强区较多,在ODF图上表现为织构强区范围更大而织构强度小,织构类型相近。而在{0001}极图上,CFR钛板退火后在厚度方向中间区域的最大极密度强度明显小于FFR钛板退火后在厚度方向中间区域的极密度强度,这说明CFR轧制工艺可以一定程度上弱化再结晶织构。
参考文献:
[1]Schutz R W,Watkins H B.Recent developments in titanium alloy application in the energy industry [J].Materials Science and Engineering A,1998,243(1/2):305-315.
[2]Shabani M O,Mazahery A.Application of GA to optimize the process conditions of Al matrix nano-composites[J]. Composites Part B,2013,45(1):185-191.
[3]邵娟.钛合金及其应用研究进展[J].稀有金属与硬质合金,2007,35(4):61-65.
[4]钱九红.航空航天用新型钛合金的研究发展及应用[J].稀有金属,2005,24(3):218-223.
[5]Bozzolo N,Dewobroto N,Grosdidier T,et al.Texture evolution during grain growth in recrystallized commercially pure titanium [J].Materials Science and Engineering A,2005,397 (1/2):46-355.
[6]Rack H J,Qazi J I.Titanium alloys for biomedical applications [J].Materials Science & Engineering C,2006,26 (8):1269-1277.
[7]Liu J M,Chen I G,Chou T S,et al.On the deformation texture of square-shaped deep-drawing commercially pure Ti sheet [J].Materials Chemistry & Physics,2003,77(3):765-772.
[8]张贵华,江海涛,吴波,等.退火温度对纯钛 TA1 织构及各向异性的影响 [J]. 中南大学学报: 自然科学版,2019,50(4):806-813.
[9]江先锋,向顺华,陈乃录.退火工艺对冷轧纯钛带再结晶织构的影响[J].热加工工艺,2011,40(18):167-169.
[10]Wang H Y,Feng T T,Zhang L,et al.Achieving a weak basal texture in a Mg-6Al-3Sn alloy by wave-shaped die rolling [J].Materials & Design,2015,88(25):157-161.
[11]Sun Z,Wu Y,Xin Y,et al.Varying the strong basal texture in a Mg-3Al-1Zn plate by a new wave-shaped interface rolling [J].Materials Letters,2017,213:151-153.
[12]Shimoyama K,Yokoyama S,Kaneko S,et al.Effect of grooved roll profiles on microstructure evolutions of AZ31 sheets in periodical straining rolling process [J].Materials Science &Engineering A,2014,611(12):58-68.
[13]江鸿.纯钛 ECAE 过程三维模拟及超细晶纯钛织构和耐腐蚀性能的研究[D].上海:上海交通大学,2010.
[14]Jiang H T,Liu J X,Mi Z L,et al.Texture evolution of commercial pure Ti during cold rolling and recrystallization annealing [J].International Journal of Minerals Metallurgy & Materials,2012,19(6):530-535.
相关链接