紧固件享有"工业之米"的美誉,是应用量最大的基础零部件,近两年我国紧固件产量持续增长,年产量超过了900万吨,居世界首位。高强度紧固件广泛应用于机械、汽车、桥梁、建筑等领域,具有承载力高、施工简便等优点,已成为工程连接中的重要手段。近年来,随着机械、汽车、建筑、桥梁等强度水平的要求不断提高,紧固件的强度及服役条件也越来越高[1-3]。在当前"碳达峰"和"碳中和"政策下,汽车、高铁、航空、航天、国防等国家重大装备制造用螺栓对长寿命高强度紧固件有紧迫需求。高强度紧固件可在相同夹持力下,减小自身尺寸实现降低自重并扩大装配空间,因此,可对被连接部件进行功能和体积优化,满足整体减重和性能优化的目的。据报道,上海大学成功研制出16.8级和19.8级紧固件,香港九号码头栈桥实际应用14.9级塔吊锚固大螺栓,新能源汽车因结构设计及轻量化发展,在多个部位应用14.9级得高强度紧固件。据了解,一架现代飞机所用的紧固件总重量可占飞机总重的5%~6%,而一架中型飞机上的各类紧固件可达到200~300万个。仅在飞机减重方面,高强度紧固件就有巨大的市场需求。由此可见,高强度紧固件钢具有很好的市场发展前景。高强度化是钢材发展的重要方向,但也带来了韧塑性降低、疲劳破坏和延迟断裂敏感性增加等挑战。在追求高力学性能的同时,材料还需具备良好的工艺适应性和服役性能,以确保在实际应用中的可靠性。因此,实现材料生产、零件制造与服役评价之间的技术匹配至关重要。这要求在材料设计和加工过程中,综合考虑力学性能与工艺性能,以满足现代工业对高强度钢的多重需求。
1、典型高强度紧固件应用分析
紧固件连接是结构件重要连接形式,应用场景广泛,要求复杂。对于紧固件,要求高可靠、长寿命,需综合考虑良好的力学性能、加工性能及热处理性能,针对特定的应用环境和产品,需单独设计制造工艺和模具等,以实现高耐磨、高表面质量以及高的抗疲劳性能。紧固件产品一般需进行保载荷、契负载、坚固性、扭矩、疲劳等试验评价,特定性能和应用环境实施特别评价,确保安全可靠。分析关系图如图1所示。
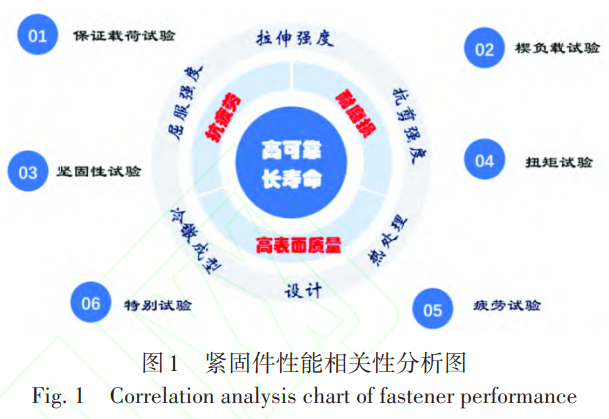
1.1 动车紧固件
动车紧固件在服役过程中面临极为严苛的应用环境,主要特征包括:①极寒与极热条件下的工作,伴随显著的温差变化;②车速差异大,且震动频繁;③在运行中承受拉压、剪切和弯曲的交变载荷;④重载与高疲劳的工作状态。随着高速动车组动力系统向大容量、大型化和更高功率转速的不断发展,工况条件变得愈加复杂和苛刻。在这样的环境下,螺栓的断裂失效成为影响高速动车组安全运行的重大隐患,直接关系到人民的生命和财产安全。高速动车组高强度螺栓属于准高周疲劳[4],因此,对高速动车组高强度螺栓的性能要求显著提高,需要考虑螺栓的强度、屈强比匹配、韧性指标和纯净度等,同时在材料选择、设计和加工工艺上进行全面优化,以确保其在极端工况下的可靠性和耐久性。
1.2 风电紧固件
风电紧固件长期野外服役,环境恶劣,维修困难,要求在正常连续工作情况下,必须保证使用寿命20a以上。近年来,风电行业向大容量的兆瓦级别快速发展,目前,已有超15MW设计和应用。全球海上风电的装机容量正在迅速增长,成为风电行业的重要组成部分。与陆上风能相比,海上风能具有多项显著优势:首先,海上风电占地面积较小,系统运行稳定,电力生产能力大,运行效率高;其次,海上风能资源通常比陆上高出20%至40%[5];最后,海洋环境中风速较大且风向变化幅度小,有助于减少风电机组的磨损,从而延长其使用寿命[6]。然而,海上风电场的工作环境相对恶劣,存在高盐浓度和较大的沉积率,导致金属腐蚀速率显著加快[7]。这种环境条件使得海上风电机组的螺栓及相关紧固件的服役寿命大幅降低,严重时甚至可能引发风电机组倒塌等安全事故。因此,风能紧固件需要有更强的机械性能、更高的耐腐蚀性及长期稳定可靠的疲劳性能。
1.3 汽车紧固件
汽车紧固件种类繁多,其中非标准紧固件质量要求最高。如汽车发动机连杆螺栓、飞轮螺栓、轮毂螺栓等由于其要求很高的质量和良好的稳定性,大部分依赖进口[8]。保证动力传递安全的发动机连杆、缸盖飞轮、变速箱螺栓等,一半以上采用10.9级及以上的高强度紧固件。从召回的汽车来看,事故的60%~70%都与紧固件有关[9]。尽管国内汽车紧固件企业与国际先进水平仍有差距,但经过长期发展,我国紧固件企业已建立了一定的产业基础和优势。随着汽车市场竞争的加剧,尤其是新能源汽车的快速崛起,汽车紧固件在轻量化、环保和长寿命等方面的要求不断提升。这促使企业加大技术创新和产品研发力度,以适应行业发展的新需求,提升市场竞争力。
2、高强紧固件钢研究进展
2.1 高强紧固件用钢发展
高强紧固件的研发始于20世纪初,最早在美国、联邦德国和日本取得成功,而我国的相关研究则是在1960年代才开始应用。早期的高强紧固件由于面临延迟断裂的问题,其强度一般不超过1000MPa,采用的主要是中碳钢或中碳含硼钢[10-11]。19世纪末,英国、法国和美国等国开始开发中碳铬镍钢(CrNi钢),但由于镍资源日益紧缺,逐渐转向在钢中添加铬、锰和钼等元素,形成了铬钼系列高强钢(如CrMo钢)[12]。这些Cr和CrMo系钢因其优异的耐延迟断裂性能,广泛应用于高强度紧固件的制造,如40Cr、SCM435(35CrMo)和SCM440(42CrMo)等,至今仍是10.9级和12.9级紧固件的重要原材料。从20世纪50年代开始,美国、德国和日本等国充分利用微量硼(B)元素显著提高钢的淬透性,进而降低合金元素的使用和成本,逐步开发出一系列硼钢。这些硼钢逐渐取代了许多中碳钢和中碳合金钢,成为制造8.8至10.9级高强紧固件的主要材料[10]。
目前,中低碳硼钢已成为高强紧固件的重要钢种,以锰硼(MnB)系列为主,同时还有铬硼(CrB)、锰铬硼(MnCrB)和锰钒硼(MnVB)等系列,因此,微合金化硼钢的发展显得尤为重要。然而,由于硼在抗回火软化方面的能力较弱,热处理过程中易导致奥氏体晶粒粗化,从而增加延迟断裂的风险。但我国开发的ML15MnVB和日本研发的钛微合金化FIRST硼钢等,均展现出优良的抗延迟断裂性能[13]。随着对合金化理论认识的深入,含硼钢将在未来得到更广泛的应用,推动高强紧固件的技术进步和性能提升。
2.2 超高强度紧固件用钢发展
随着结构件对更高应力设计需求的增加和轻量化发展的趋势,12.9级以上的超高强度螺栓需求愈发迫切。然而,当钢材强度超过1200MPa时,疲劳破坏和延迟断裂问题变得更加突出,特别是螺纹螺栓作为缺口零件,其缺口敏感性更高,面临更大的风险。在延迟断裂机理的研究推动下,国外超高强螺栓钢的开发进展迅速。例如,日本住友金属推出的ADS系列和神户制钢的KNDS系列马氏体型耐延迟断裂超高强螺栓钢,经过合金成分和回火温度的优化,其抗拉强度可达到1200~1500MPa,同时回火抗力也显著提升。
此外,美国工业紧固件协会(IFI)近期发布了已实现工业化应用的15.8级和16.8级超高强紧固件,这些材料与SAE8640相似,通过控制下贝氏体组织的形成,大幅提高了紧固件的耐延迟断裂性能。这些进展为满足现代工程对超高强度螺栓的需求提供了重要支持。
21世纪初,我国也开发出耐延迟断裂高强度ADF系列13.9级和14.9级螺栓马氏体型超高强螺栓钢,并得到应用[14]。近期据报道,董翰研究团队已试制出19.8级超高强度紧固件。随着理论研究的深入,在钢中导入更多的氢陷阱可有效解决延迟断裂问题[15-16],在含钼钢中,大量碳化物作为氢陷阱,有效抑制氢引发的脆性破坏。回火过程中,细小的碳化物析出并展现出显著的二次硬化现象,从而提高了回火抗力。此外,钼的添加还可以减少杂质元素在晶界的偏聚,增强晶界强度。因此,钼的引入不仅能确保钢材的高强度,还显著提升了其耐延迟断裂性能。
2.3 高强度非调质紧固件钢发展
用非调质钢生产紧固件,可简化生产工序,缩短生产周期,具有节能环保等特点,应用日益广泛。黄志国等[17]从晶粒细化、位错强化等方面探讨了10.9级非调钢的强韧性机理,研究了冷镦钢轧材和深加工紧固件的组织性能调控的重要性;董秋瑶、王利军等[18-19]均发现加工硬化时效处理规律,随着时效温度升高,强度和硬度先增大后减小,屈强比变化不大,塑性得到改善。董秋瑶等[18]从机理上揭示了该现象的原因,认为是冷加工过程形成了大量位错胞,阻碍位错运动,同时,基体中的纳米级铌、钒碳氮化物,经时效处理后碳氮化物和铁素体基体中的碳、氮原子发生扩散至位错处,形成柯氏气团,起到钉扎位错的作用,从而提高强度、硬度和塑性。目前,非调质钢在紧固件制造中主要通过冷作强化。然而,在实际应用中,10.9级及以上的非调质钢高强度紧固件面临一些挑战,如模具磨损严重以及冷拔工艺与产品质量稳定性之间的匹配问题,因此,亟需进一步研究和改进。这使得非调质紧固件钢在市场上,尤其是在应用量大的带螺头螺栓领域受到限制。尽管如此,冷作强化型非调质钢的优势在于省去了退火和调质处理工序,避免了热处理可能引发的一系列质量问题,特别是在保证细长螺栓的直线度方面,冷作强化型钢表现优异,有效解决了调质钢在长螺栓热处理过程中的难题,具有重要的推广价值,广泛应用于U型螺栓、球销、长螺杆等,如图2所示。我国非调质紧固件技术起步于20世纪80年代,形成了MFT8、MFT9、MFTl03个牌号。日本钢企开发的非调质钢紧固件牌号见表1,高强产品涵盖了900~1200MPa一系列级别。
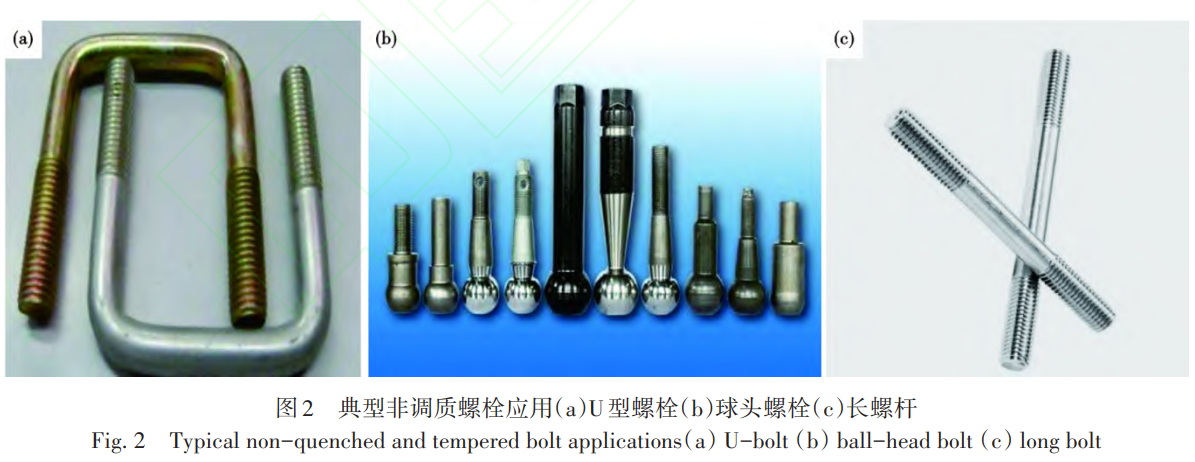
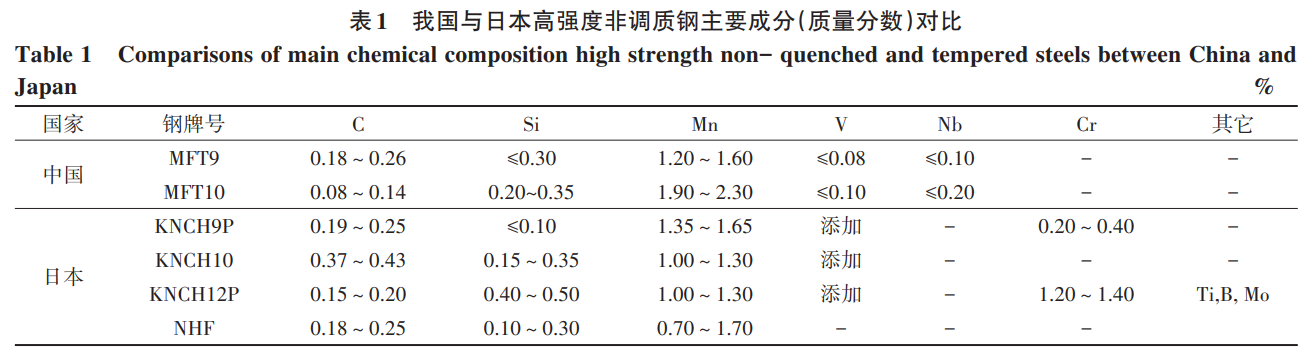
3、高强度紧固件钢关键技术研究及应用
3.1 成分设计研究
高强度紧固件成分设计取决于产品的热处理方式、抗延迟性能及产品性能,一般10.9级产品选用中碳Cr钢、CrMo钢,为降低成本,近年来,CrB钢和MnB钢被广泛应用于高强度紧固件的制造中。合金元素Cr和Mo在这些钢材中扮演了重要角色,其主要功能包括:首先,提高钢的淬透性,使得钢材在热处理过程中能够获得更好的硬度和强度;其次,提升高温强度和蠕变强度,确保高强度紧固件在高温环境下的稳定性和可靠性;第三,增强抗腐蚀性和抗氧化性,提高紧固件在恶劣环境中的使用寿命;第四,改善抗磨粒和摩擦磨损性能,提升使用过程中的耐久性;最后,提高奥氏体粗化温度,确保在高温条件下钢材的组织稳定性。
针对高碳硬线紧固件钢,研究者冯运莉等[20]发现,加入Cr合金元素能够优化钢材的微观组织,减少铁素体的形成,增加索氏体的含量,从而显著提升抗拉强度,增加75~100MPa,同时断面收缩率也提高了约2%。Mo作为高强度紧固件的主要强化元素,对合金钢的强度提升效果显著。惠卫军等研究指出,Mo元素在原奥氏体晶界的偏聚能够增强合金钢的晶界结合强度,提高钢材的回火抗力及耐延迟断裂性能。早期研究认为,当w[Mo]超过1.15%时,钢的耐延迟断裂性能不会再提高[21]。然而,来自日本久保田公司
的专利显示,2010年他们成功研发出1800MPa级的马氏体型超高强螺栓,其中,w[C]约为0.40%,而w[Mo]高达3%~10%,其抗延迟断裂性能甚至优于35CrMo钢[22]。另在合金化方面,Ni元素能够显著提升合金钢的力学性能,但由于其成本较高,通常需要控制在较低水平。研究表明[23],当Ni含量过高时,会导致马氏体转变温度降低,从而增加孪晶马氏体和残余奥氏体的含量,这些残余相会降低合金钢的屈服强度。此外,冯春雨等的研究表明[24],微量w[B]≥0.005%的加入能显著提高合金钢的淬透性,其效果优于铬、锰等传统合金元素。
为了进一步提升抗延迟断裂性能,研究者们通过添加细化晶粒元素和碳化物形成元素,同时,降低晶界元素的含量,来改善钢的性能。杨作宏等[25]指出,Nb的加入能够有效阻止奥氏体晶粒的长大,从而提高合金钢的粗化温度。V作为理想的沉淀强化元素,能够提高奥氏体的粗化温度,R·CCochrance等[26]研究发现,V促进晶粒细化,同时增加淬透性和回火稳定性,并形成明显的二次硬化效果。惠卫军等[27]的研究也表明,V的加入能够提升合金钢的回火抗力,细化奥氏体晶粒,并形成VC氢陷阱。此外,适量的Ti元素也能显著改善合金钢的耐延迟断裂性能[28],但过量的Ti会形成夹杂物Ti(C,N),影响钢的整体性能。HasegawaT等[29]的研究结果与惠卫军的结论相似,表明,w[Ti]的最佳加入量应控制在0.03%~0.06%。最后,研究结果表明,钢中P、S含量较高时,会在晶粒边界偏析,降低抗延迟断裂性能。通过降低钢中P、S的含量,减少晶界偏析,可以显著提升高强度紧固件钢的综合性能。因此,优化合金成分和控制杂质元素的含量,是提高高强度紧固件钢性能的重要途径。通过这些研究,可为未来高强度紧固件的开发提供理论基础和实践指导。日本钢企与国内设计的高强度紧固件钢牌号化学成分见表2。
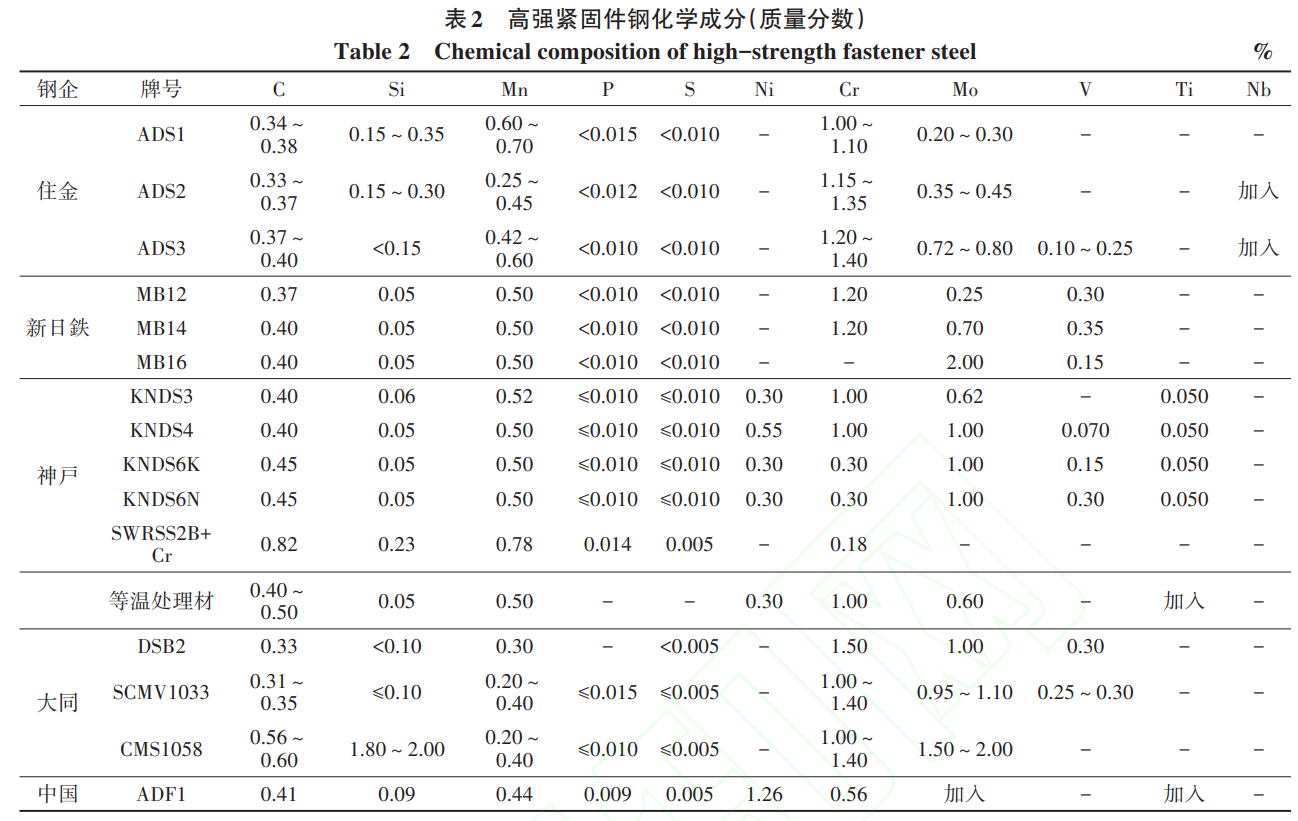
3.2 纯净度控制研究
夹杂物的存在割裂了金属的连续性,剥落后就成为凹坑或裂纹,在冷镦成形时极易形成裂纹源,热处理时易造成应力集中,产生淬火裂纹,影响金属的力学性能、加工性能和耐蚀性能,高强度紧同件对夹杂物应严格控制。为减轻夹杂物带来的危害,需要严格管理和控制炉料准备、冶炼操作。通过选用优质原料并提前预判有害元素,采取针对性措施可显著减少杂质含量;在冶炼过程中,选用优质耐材,采用合适的精炼渣及工艺措施,大幅提升钢液纯净度;在连铸过程中,通过中间包冶金、结晶器冶金等技术,进一步减少夹杂含量。非金属夹杂物在钢中主要以氧化物、硫化物和点状不变形夹杂存在,根据GB/T10561—2023标准A法进行评级。但GB/T6478—2015《冷镦和冷挤压用钢》对夹杂物未做明确要求,而是根据需方要求协商,并在合同中注明,钢材才进行非金属夹杂物检验。目前,国内外紧固件制造单位,对高强度紧固件钢均提出了明确的要求,按GB/T10561—2023最严重视场法,合格级别见表3。夹杂物的严格要求,对实现紧固件的高疲劳、高强度、高稳定性非常有益。
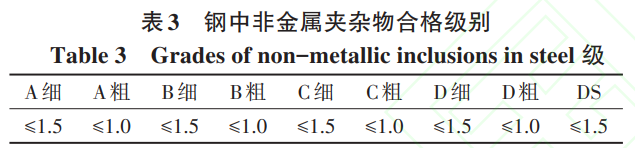
3.3 抗氢至延迟断裂研究
随着螺栓强度等级的提升,虽然能够带来更高的承载效益,但与此同时,氢致延迟断裂的风险也显著增加,尤其是在抗拉强度超过1200MPa时,材料的氢敏感性更加突出[13,29-30]。氢致延迟断裂具有延迟性、突发性和不可逆的特征,通常表现为批次性发生,对结构的安全性造成较大威胁。氢脆的机理极为复杂,其断裂现象也多种多样,国内外学术界提出了多种氢脆理论,包括位错钉轧理论、晶界聚集理论、氢气泡理论和脆化相理论等。因此,如何提高高强度螺栓的抗延迟断裂能力,成为近年来研究的热点之一。
研究表明,并非所有的氢都是有害的。根据氢与材料的结合能(Ea)高低,氢陷阱可以分为可逆和不可逆两类。可逆氢陷阱会促使氢向应力集中处扩散并富集,从而增加延迟断裂的敏感性,这种情况是有害的。相对而言,均匀分布的非可逆氢陷阱能够提高钢材的耐延迟断裂性能。通过在钢中引入更多的氢陷阱,是解决延迟断裂问题的有效途径[15-16]。
在高强度钢中,氢致延迟断裂主要是由可逆陷阱中的扩散氢引起的。氢陷阱不仅包括碳化物粒子,还涉及多种晶粒缺陷,如空位、位错、晶界、碳/氮化合物(夹杂物)以及相界等。这些不同类型的氢陷阱在材料中发挥着不同的作用,且在材料变形过程中,由于各相组织的改变和晶体缺陷密度的增加,氢的运动过程变得更加复杂[31]。
因此,研究者们正在探索如何优化钢材的微观结构,以增强其抗氢脆能力。通过控制合金元素的添加和热处理工艺,可以有效地调整氢陷阱的分布和类型,从而提高材料的整体性能。此外,开发新型的氢陷阱材料以及改进现有材料的氢扩散特性,也是当前研究的重点方向。
综上所述,提升高强度螺栓的抗延迟断裂能力不仅需要深入理解氢脆的机理,还需通过材料设计和工艺优化来实现。这一领域的研究将为高强度紧固件的安全应用提供重要的理论基础和实践指导。表4列出了不同氢陷阱结合能Ea和升温速率的数据[16,32],其中碳化物作为氢陷阱的能力与其分布、形态及尺寸有关。综合以上信息,改善高强度紧固件钢耐延迟断裂性能关键技术及措施见表5。
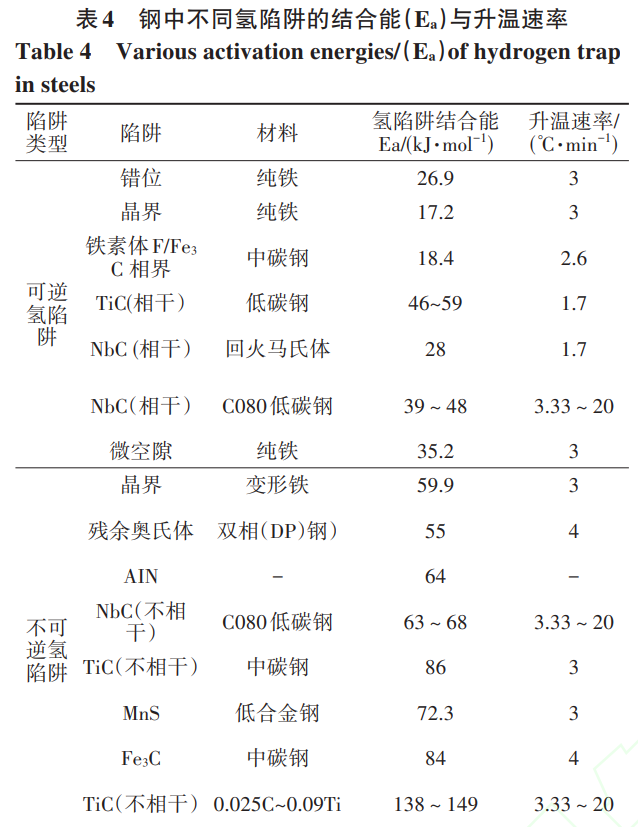
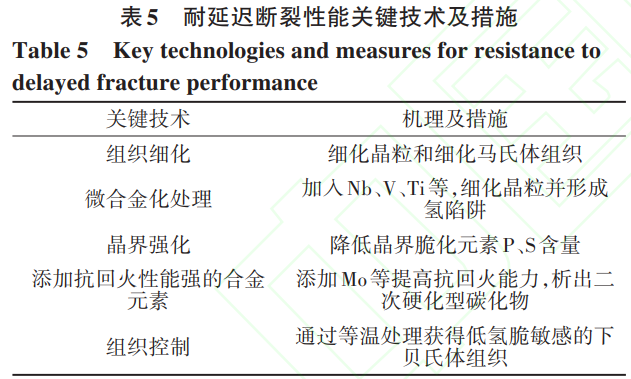
下面重点介绍组织控制对抗延迟断裂的研究
1)下贝氏体组织控制:高强度螺栓在热处理过程中采用合适的热处理工艺尤为重要,它不仅可以改善螺栓的显微组织,还可以降低螺栓对氢脆的敏感性。研究表明,显著的氢脆特征主要源于应变过程中残余奥氏体发生的马氏体转变,贝氏体对氢脆不敏感。如果采用等温处理代替淬火+回火,可以得到氢脆敏感性小于回火马氏体的下贝氏体组织。图3为高强度贝氏体型螺栓,在36%盐酸溶液中10次酸浸后利用慢应变拉伸试验,评价氢脆敏感性结果,可以看出,贝氏体型螺栓强度达到1500MPa时,还略低于传统调质工艺10.9级敏
感性。
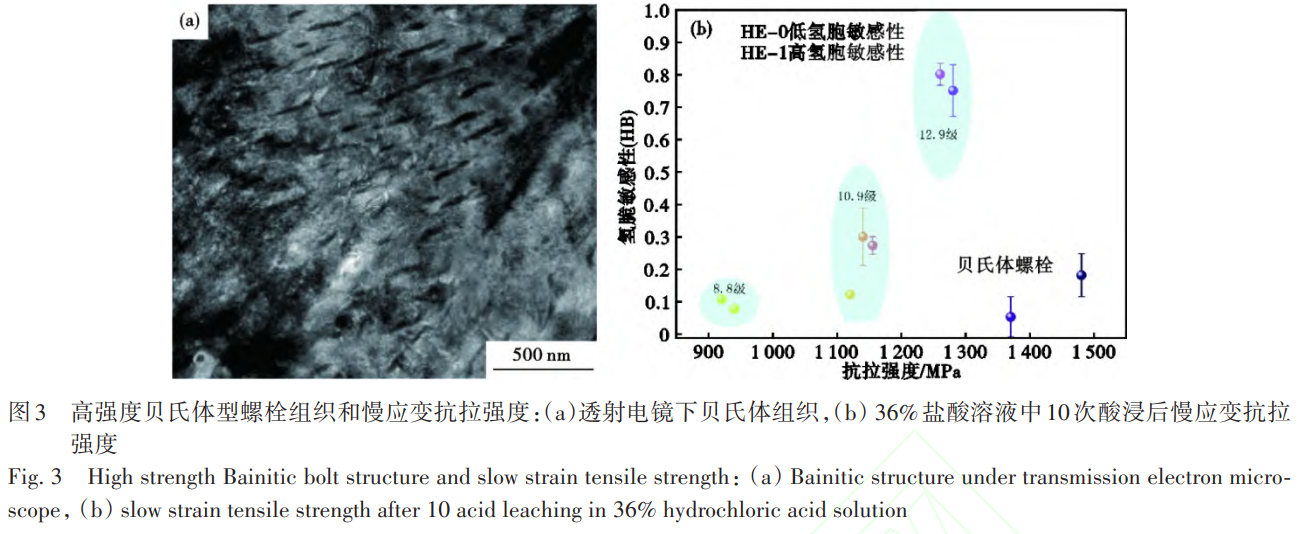
2)索氏体组织控制:神户制钢在本田03MAccord发动机螺栓开发过程中,充分利用高碳钢盘条冷加工硬化、包辛格效应、新冷镦模设计及应力松弛现象等,成功开发出1600MPa级紧固件钢。该钢接近100%珠光体组织,富松等在珠光体丝表面做聚焦离子束加工,钢丝由平行于拉丝方向的铁素体(α)相和渗碳体(θ)相构成,制备了相对于α/θ界面不同方向的带缺口悬臂梁试样。然后,在电解充氢下实施了压头压入弯曲试验[15],试验结果如图4所示,研究表明,对氢脆弱的α/θ界面与拉伸轴平行,拉丝珠光体钢在拉丝方向上具有出色的抗氢脆性[33]。目前珠光体钢冷加工后强度已超过3000MPa,对超高强紧固件制造是选择之一。
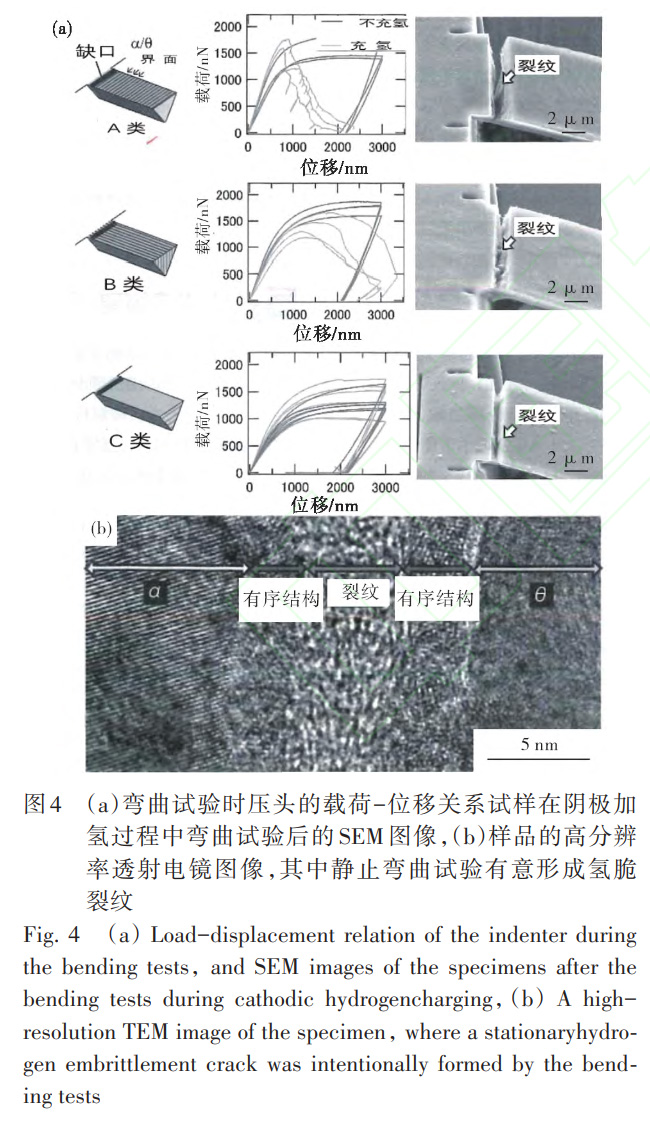
3.4 高强度紧固件钢制造技术
紧固件钢的性能对螺栓的生产和性能有着重要影响,因此,研究高强度螺栓的母材具有重要的意义和研究价值。目前,国内多家企业如兴澄特钢、宝钢和青钢等,均已具备生产高强度冷镦盘条的能力。兴澄特钢采用390mm×510mm的超大断面连铸坯,而宝钢则通过320mm×425mm的连铸坯或模铸工艺来制造高强度螺栓钢。为确保铸坯的质量,兴澄特钢引入了高洁净冶炼、低过热度浇铸、结晶器电磁搅拌、凝固末端电磁搅拌和轻压下等先进技术。
高强度螺栓用冷镦钢的生产工艺流程包括初轧机、火焰清理和连轧开坯等多个环节。在这一过程中,中间坯料经过抛丸处理、超声波探伤、红外检测、修磨以及高线轧制(配备测径仪和在线影像探伤仪),最终完成精线加工。这一系列严格的工艺控制,不仅提高了产品的质量,也降低了缺陷率。
通过上述工艺技术生产的Cr(Ni)Mo(V)系列高强度冷镦钢,代表了国内的最高水平。这些钢材的主要特点包括成分稳定且波动小、有害成分(如P、S、H)含量低、夹杂物含量少、脱碳现象轻微、表面质量良好、偏析程度低以及淬透性优良。此外,盘条的冷镦开裂率也显著降低,为高强度螺栓的应用提供了可靠保障。兴澄开发的高端紧固件钢已成功应用于燃油车发动机5大关键部件和新能源车电池包、防撞梁等核心部位及高铁、桥梁等重大装备和工程领域。
此外,在盘条轧制过程中苏世怀等[34],利用形变诱导相变机制,通过控轧控冷,实现了在线获得球状渗碳体组织,解决了困扰非调质冷镦钢应用的形变位错稳定化、冷加工性等难题,开发出在线球化或退化中碳冷镦钢和软质化合金冷镦钢等系列产品,盘条的在线控轧控冷技术,可缩短球化退火时间,部分紧固件产品满足直接拉拔,具有良好的应用前景。随着“双碳”目标的推进,行业内积极开展氢冶金探索,增加废钢使用量,减少CO2排放。这一转型不仅符合国家的环保政策,也为高强度螺栓的生产提供了新的思路。
综上所述,高强度紧固件钢的研究与应用对螺栓的生产和性能至关重要。国内企业如兴澄特钢、宝钢等通过超大断面连铸坯或模铸工艺,坯料经过严格的表面处理、超声波探伤和控轧控冷等技术措施,显著提升了产品质量,降低了缺陷率,确保了高强紧固件钢的高质量。
在合金成分设计方面,Cr、Mo等元素的加入提升了钢材的淬透性和抗腐蚀性,改善了抗延迟断裂性能。研究表明,通过微量B、Nb和V的添加也能有效提高钢材的性能。此外,夹杂物的控制对高强度紧固件的性能至关重要,需严格管理冶炼过程以减少杂质含量。随着“双碳”目标的推进,行业内积极探索氢冶金技术,增加废钢使用量,减少CO2排放,这为高强度螺栓的绿色化发展提供了新的思路。通过以上技术研究与应用,国内高强度紧固件钢的制造水平不断提升,为产业升级指明了方向。
4、展望
随着新能源环保技术装备、大型轨道交通装备及工程、航空航天设备等高端制造产业的快速发展,高强度紧固件钢作为螺栓制造的重要材料,其性能和质量直接关系到紧固件的使用效果和安全性,超高强度紧固件钢的发展前景广阔,主要体现在以下几个方面:
(1)材料研发:随着钢铁材料基因工程的研究深入和冶金技术的进步,超高强度紧固件钢的成分和微观结构将进一步优化,以提高其强度、韧性和耐腐蚀性。低氢脆敏感高强度贝氏体钢快速发展和应用,紧固件工程应用强度级别将突破16.8级。
(2)生产工艺:先进的生产工艺,如控轧控冷技术和在线韧化处理技术,低氢含量控制技术及超纯净控制技术将被广泛应用于超高强度紧固件钢的制造,以提升其性能和降低生产成本。高强紧固件钢中w[H]低于1×10-6,有害夹杂物尺寸进一步缩小,以实现优良的综合疲劳性能。
(3)环保与可持续发展:在全球对环保要求日益严格的背景下,超高强度紧固件钢的生产和应用将更加注重资源的节约和环境的保护,发展绿色制造技术将成为重要趋势。电炉钢冶炼及氢冶金品种占比大幅提升。
(4)智能化与数字化:随着工业4.0的推进,智能制造和数字化技术将在超高强度紧固件钢的生产、检测和管理中发挥越来越重要的作用,提高生产效率和产品质量。钢中成分控制更精确,主元素波动范围应达到w[C]±0.01%,w[Si]±0.02%,w[Mn]±0.02%,w[Mo]±0.01%,满足紧固件行业智能化发展并实现紧固件性能稳定。
综上所述,高强度紧固件钢的发展前景广阔,未来将朝着高性能、低成本、环保和智能化的方向发展。
参考文献
[1] 邱林波,刘 毅,侯兆新,等 . 高强结构钢在建筑中的应用现状 研究[J]. 工业建筑,2014,44(3):1-5.
[2] 並村裕一 . 鋼構造に使用されるボルト用鋼材[J]. 鋼と 鉄,2002,88(10):600-605.
[3] ALBRECHT P,NAEEMI A H. Performance of weathering steel in bridges[R]. Nchrp Report,1984.
[4] 束德林. 金属力学性能[ M]. 北京:机械工业出版社,1987.
[5] 钟盛钢, 张先鸣 . 风电用与钢结构用高强度紧固件的差异[J]. 金属制品, 2009, 35(6): 62-65.
[6] 孙一琳.全球海上风电市场现状与展望[J].海上风电,2020, (9):40-43.
[7] 詹 耀 . 海上风电机组的防腐技术与应用[J]. 现代涂料与涂 装, 2012, 15(2): 15-18.
[8] 冯 琴.浅述大陆冷镦钢的生产和发展[J].螺丝世界,2008,112:84-85.
[9] 沈德山, 张先鸣 . 汽车紧固件用冷镦线材的现状[J]. 金属制 品, 2009, 35(3): 33-35+38.
[10] 惠卫军, 董 瀚, 翁宇庆 . 高强度螺栓钢的发展动向[J]. 机 械工程材料, 2002, 26(11): 1-4.
[11] Azuma K,Chida T’Tarui T,et a1. Development of super higll⁃ strength bolts with tensile strengths of 1600 to 2000 N/ram2[J]. Int. J. Steel Struct. ,2009,9:291.
[12] Cobb H M. The history of stainless steel[M]. Materials Park, Ohio: ASM International, 2010: 3 1
[13] 惠卫军,董 瀚,翁宇庆 . 高强度螺栓钢[M]. 北京:冶金工业 出版社,1999:1.
[14] 李 阳 , 张永健 , 惠卫军 , 等 . 1500 MPa 级 高 强 度 钢42CrMoVNb 的 氢 吸 附 行 为[J]. 金 属 学 报 , 2011, 47(4): 423-428.
[15] Lynch S. Hydrogen embrittlement phenomena and echanisms[J]. Cortes. Rev. ,2012,30:105
[16] HUI Wei-jun1DONG Han1 WENG Yu-qing,et a1.Delayed frac⁃ ture behavior of CrMo·type high strength steel containing titanium[J]. Journal of iron and steel research international. 2005,12(1):43-49.
[17] 黄志国,曹永政,李艳艳,等. 10. 9 级紧固件用贝氏体型非调质 冷 镦 钢 的 研 究 现 状[J]. 金 属 热 处 理 , 2023. 48(8):219-225.
[18] 董秋瑶,陆恒昌,张林祥,等 . 冷拔与时效对 10. 9 级紧固件非 调质钢的影响[J]. 钢 铁, 2024. 59(11) :165-172.
[19] 王利军,阮士朋,等,高强度螺栓用非调质钢的研制与应用[J].钢 铁,2018. 53(11):102-106
[20] 冯运莉,杨海丽. 微合金元素Cr对高碳钢线材组织性能的影响 [J]. 钢铁钒钛,2003,24(4):31-34.
[21] 惠卫军, 董 瀚, 翁宇庆, 等. Mo对高强度钢延迟断裂行为的 影响[J]. 金属学报, 2004, 40(12): 1274-1280.
[22] 董 瀚, 廉心桐, 胡春东, 等. 钢的高性能化理论与技术进展 [J]. 金属学报, 2020, 56(4): 558-582.
[23] 范长刚, 董 瀚, 时 捷, 等. 镍含量对2200 MPa级超高强度 钢力学性能的影响[J]. 金属热处理, 2007, 32(2): 16-19. .
[24] 冯春雨 . 浅谈合金元素在钢中的作用[J]. 冶金标准化与质 量, 1996, 34(8): 20-23.
[25] 杨作宏, 陈伯春 . 谈微合金元素 Nb、V、Ti 在钢中的作用[J]. 甘肃冶金, 2000, 22(4): 20-22.
[26] R. C. Cochrance,W. B. Morrian. Shadow response ofvanadium to phase change characteristics of steels used in high strength pipe 1iIIes[J]. METALS TECHNOLOGY,1981,12:458-464.
[27] 惠卫军,董 瀚,王毛球,等. 钒对高强度钢耐延迟断裂性能的 影响[J]. 金属热处理,2002,27(1):1-3.
[28] 惠卫军,董 瀚,翁宇庆,等. 钛对高强度钢耐延迟断裂性能的 影响[J]. 钢铁研究学报,2002,14(1):30-33.
[29] Hasegawa T,Nakahara T,Yamada Y,et a1. Delayed Failure of Steels for High—Strength Bolts[J]. Wire JInter,1992,(12):49-58.
[30] 陶晓燕, 沈家华, 史志强. 我国钢桥高强度螺栓连接的发展历 程及展望[J]. 铁道建筑, 2017, 57(9): 1-4.
[31] 张先鸣. 氢脆研究的新进展[J].紧固件,2011(32):104-107.
[32] K. Tomatsu, T. Amino, T. Chida, S. Uji, M. Okonogi, H. Kawata, T. Omura, N. Maruyama, and Y. Nishiyama : ISU Int. , 2018,(58):340-340.
[33] Kenichi Takai, Takehide Senuma, Eiji Akiyama. Prospective Re⁃ search of Fundamental Factors and Characteristic Evaluations of Hydrogen Embrittlement[J], Ferrum ,2020,25(3):1-4.
[34] 苏世怀,于同仁,惠卫军,等,免后续热处理节能型冷镦钢产品 开发及应用技术[J]. 中国冶金,中国钢铁工业协会、中国金属 学会冶金科学技术奖获奖项目简介,2015,25(10):77-77.
相关链接