在航空与船舶领域,钛棒、钛锻件及钛板三类型材凭借差异化工艺与性能特征,形成互补性技术布局。钛棒多采用TC4(Ti-6Al-4V)或TA17(Ti-4Al-2V)材质,通过熔炼、锻造或挤压成型,抗拉强度≥895 MPa,屈服强度≥825 MPa,满足ISO 5832-3外科植入物级标准及ASTM B348棒材规范,其低温韧性(-196℃冲击功≥25 J)与高比强度(钢的2倍)使其成为飞机起落架轴杆、船舶推进器主轴的优选材料。钛锻件通过自由锻或模锻工艺实现晶粒细化,以TC4、Ti-75(Ti-6Al-2Nb-1Ta-0.8Mo)为代表,晶粒尺寸控制在5-20 μm,抗疲劳强度较铸造件提升30%以上,且残余应力降低至≤50 MPa,符合ASTM B381锻件标准,适用于航空发动机高压压气机盘、舰船深海耐压壳体等关键承力部件。钛板以TA1/TA2工业纯钛及TC4合金为主流,采用热轧+冷轧复合工艺,厚度精度达±0.05 mm,表面粗糙度Ra≤1.6 μm,执行ASTM B265板材标准,兼具耐海水腐蚀(腐蚀速率≤0.0015 mm/a)与电磁屏蔽特性,广泛用于飞机蒙皮、船舶舱壁及声呐导流罩。
从材质演进看,航空领域正向高强β钛合金(如TB8/TB9系列)倾斜,其抗拉强度突破1200 MPa,同时通过Al-Mo-Si系合金优化实现600℃长期耐热性;船舶领域则聚焦TA17、Ti-31(Ti-3Al-2.5V)等焊接友好型合金,焊缝强度系数≥0.9,适应大型舰体分段建造需求。执行标准体系呈现军民融合趋势,航空领域在GB/T 3620.1基础上引入AMS 4928(航空用钛板)、AMS 6945(高强钛棒)等军标,船舶领域则强化GB/T 3621与DNVGL-OS-C401船级社规范的协同认证。工艺创新方面,钛棒精密冷轧技术可将直径公差压缩至±0.02 mm,减少后续机加工量;钛锻件近净成形技术使材料利用率从60%提升至85%,结合等温锻造工艺可将变形温度波动控制在±10℃以内,保障组织均匀性;钛板超塑性成形(SPF)技术利用850℃下延伸率≥300%的特性,实现复杂曲面一体成型,减重效果达20%-30%。未来发展趋势将聚焦低成本化(如低合金化TA系列替代TC4)、功能集成化(如钛板-复合材料层压结构)及智能化制造(锻造过程数字孪生模拟),推动钛材在航空发动机整体叶盘、船舶氢燃料储罐等尖端场景的深度渗透。
以下是中扬金属针对航空与船舶领域用钛棒、钛锻件、钛板三种型材的对比分析,从形态工艺、性能特点、应用场景、执行标准及发展趋势等维度展开:
一、材质对比
型材类型 | 常用钛合金牌号 | 材质特性 | 典型应用场景 |
钛棒 | TC4(Ti-6Al-4V) | 综合性能优异(抗拉≥895MPa),耐高温(400℃),中等塑性 | 航空发动机轴、船舶液压管路 |
TA2(工业纯钛) | 高耐蚀性(C5级环境)、低强度(抗拉≥345MPa),易加工 | 船舶海水泵阀杆、航空非承力支架 |
钛锻件 | TC11(Ti-6.5Al-3.5Mo-1.5Zr) | 高温性能强(500℃长期使用),抗蠕变 | 航空发动机涡轮盘、船舶曲轴锻件 |
Ti-5Al-2.5Sn | 焊接性好,低温韧性优异(-196℃) | 航天低温燃料储罐、极地破冰船部件 |
钛板 | TA1/TA2(工业纯钛) | 高成形性(延伸率≥25%),耐点蚀 | 船舶耐压壳体、航空机舱防火隔板 |
TC4(Ti-6Al-4V) | 高比强度(抗拉≥950MPa),抗疲劳 | 舰载机蒙皮、潜艇声呐导流罩 |
二、应用前景对比
型材类型 | 航空领域前景 | 船舶领域前景 |
钛棒 | 新增长点: | 新增长点: |
- 超音速客机发动机高压转子(耐温>600℃) | - 深海采矿船机械臂驱动轴(抗高压腐蚀) |
- 电动飞机轻量化导电钛棒(替代铜合金) | - 氢燃料船低温液氢输送管(防氢脆) |
钛锻件 | 技术趋势: | 技术趋势: |
- 等温锻造工艺普及(β相区控形,提升组织均匀性) | - 大型LNG船双燃料发动机曲轴一体化锻造(单件重量>20吨) |
- 3D打印预成型毛坯(减少材料损耗) | - 耐蚀-耐磨复合锻件(表面渗氮处理) |
钛板 | 创新方向: | 创新方向: |
- 超薄钛板(0.1mm)用于柔性机翼蒙皮(可变形飞行器) | - 超宽幅钛板(宽度>4m)用于全钛船体外壳(减少焊接缝) |
- 高导热钛板(掺杂石墨烯)用于热防护系统 | - 钛-钢复合板(爆炸焊接)降低成本
|
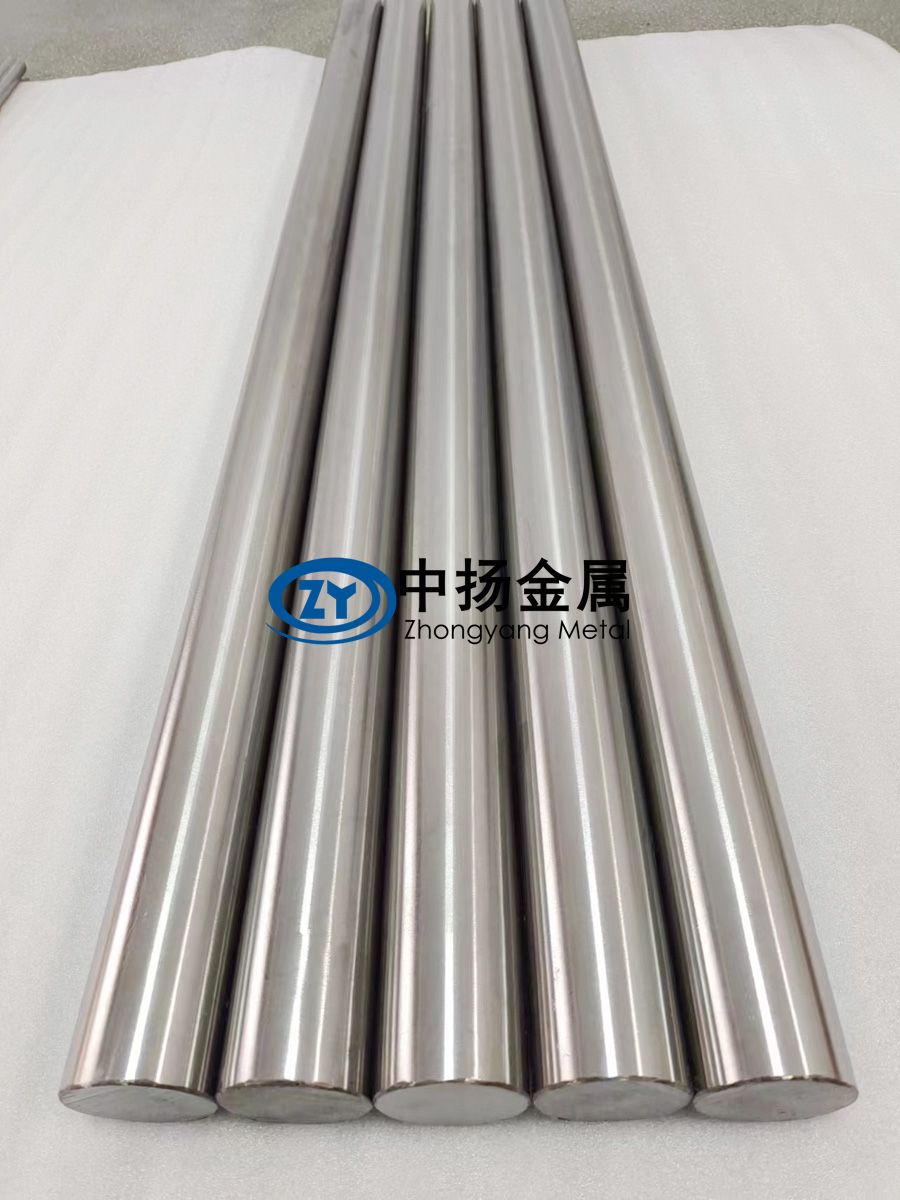
三、综合对比表(含材质与前景)
维度 | 钛棒 | 钛锻件 | 钛板 |
核心材质 | TC4(60%)、TA2(30%)、TA18(Ti-3Al-2.5V,10%) | TC11(50%)、TC4(30%)、Ti-1023(β钛合金,20%) | TA1/TA2(70%)、TC4(25%)、TA9(Ti-0.2Pd,5%) |
未来技术 | 纳米晶钛棒(ECAP工艺提升强度30%) | 增材制造+锻造复合工艺(缩短交付周期50%) | 激光冲击强化钛板(疲劳寿命提升2倍) |
市场预测 | 2025年航空需求增长25%(C919量产驱动) | 船舶锻件市场规模达$8亿(2027年,LNG船扩产) | 舰艇钛板渗透率超40%(替代传统HY-80钢) |
环保挑战 | 熔炼能耗高(需推广氢能电弧炉) | 锻模寿命短(研发陶瓷涂层模具) | 酸洗废液处理(推广干式喷砂替代工艺) |
四、形态与制造工艺对比
型材类型 | 形态特征 | 核心制造工艺 | 典型加工流程 |
钛棒 | 圆柱/方棒状,直径10mm~500mm | 熔炼铸造→热轧/冷拉→矫直 | 真空电弧熔炼→锻造开坯→多道次轧制→表面车光 |
钛锻件 | 异形结构(如法兰、轴类) | 自由锻/模锻→热处理→机加工 | 钛锭加热→锻压成型(变形量>50%)→去氧化皮→精铣 |
钛板 | 薄板/中厚板,厚度0.5mm~100mm | 热轧→冷轧→退火→表面处理 | 铸锭热轧至坯板→多道次冷轧(厚度公差±0.05mm)→酸洗 |
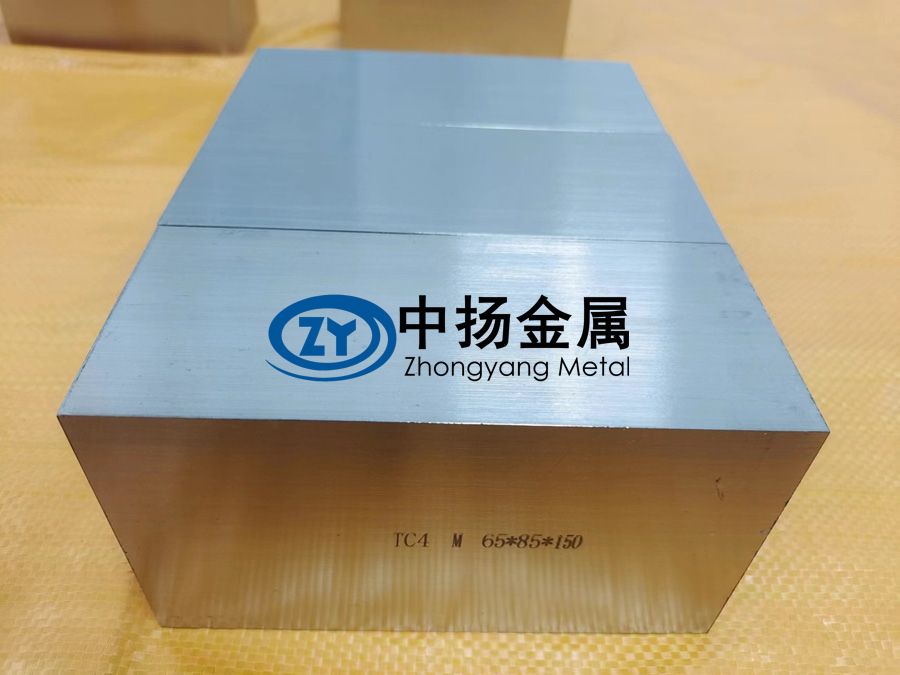
五、性能与材料特性对比
性能指标 | 钛棒 | 钛锻件 | 钛板 |
强度 | 中等(如TC4抗拉≥895MPa) | 最高(锻造细化晶粒,TC4锻件抗拉≥1100MPa) | 适中(冷轧态抗拉≥950MPa) |
各向异性 | 低(轧制方向均匀) | 可控(通过锻造流线设计优化方向性) | 较高(轧制方向强度↑15%) |
耐腐蚀性 | 均匀耐蚀(盐雾测试>5000h) | 局部易因残余应力引发微区腐蚀(需喷丸强化) | 表面氧化膜致密(耐海水腐蚀等级C5-M) |
疲劳寿命 | 中高(S-N曲线斜率-0.1) | 最高(锻造消除缺陷,疲劳极限≥500MPa) | 中(表面划痕敏感,需抛光处理) |
六、应用场景与典型案例
应用领域 | 钛棒典型应用 | 钛锻件典型应用 | 钛板典型应用 |
航空领域 | 发动机压气机叶片轴(波音787) | 起落架主承力框(空客A350) | 机身蒙皮(F-22战斗机) |
船舶领域 | 潜艇声呐阵列支架(俄罗斯“北风之神”级) | 螺旋桨叶根锻件(中国“蛟龙”号深潜器) | 船体外壳耐压板(日本“苍龙”级潜艇) |
共性场景 | 液压管路系统(耐高压腐蚀) | 阀门阀体(高温高压工况) | 防火隔层(舰艇机舱A60防火分隔) |
七、执行标准与检测要求
标准维度 | 钛棒 | 钛锻件 | 钛板 |
国际标准 | AMS 4928(航空级钛棒) | AMS 6945(β钛合金锻件) | ASTM B265(商用钛板) |
成分控制 | O≤0.20%、Fe≤0.30%(航空级) | 杂质总量≤0.4%(需真空自耗重熔) | H≤0.015%(防氢脆) |
无损检测 | 超声波探伤(Φ≥20mm棒材) | 渗透检测(表面裂纹)+X射线(内部缺陷) | 涡流检测(厚度≤6mm板) |
机械测试 | 室温拉伸+高温蠕变(发动机用棒材) | 低周疲劳测试(循环次数>10⁴) | 杯突试验(冷成型性评估) |
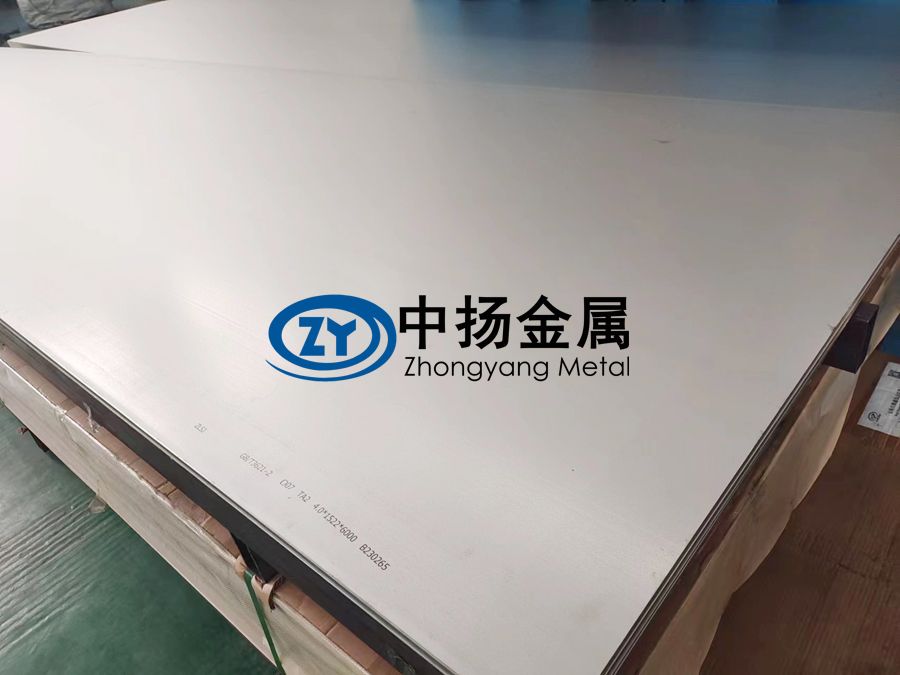
八、成本与市场趋势分析
分析维度 | 钛棒 | 钛锻件 | 钛板 |
原材料成本 | ¥200~400/kg(TC4) | ¥500~800/kg(模锻模具费占比30%) | ¥150~300/kg(冷轧薄板溢价高) |
加工损耗率 | 15%~25%(车削余量) | 40%~60%(锻坯→成品) | 5%~10%(剪切/冲压成型) |
技术趋势 | 精密冷拉技术(直径公差±0.02mm) | 等温锻造(β相区变形,提升组织均匀性) | 超宽幅轧制(宽度>3m,减少焊接接头) |
需求增长点 | 航空发动机高压压气机转子(C919增量需求) | 船舶大型曲轴锻件(LNG船用双燃料发动机) | 舰载机电磁弹射轨道用高导磁钛板 |
结论
性能导向:钛锻件在高承载关键部件不可替代,钛板侧重轻量化与耐蚀覆盖,钛棒适合轴类/管系;
成本结构:锻件因模具和材料损耗成本最高,板材规模化生产更具经济性;
技术迭代:航空领域推动钛棒精密化(纳米晶强化),船舶领域需求超厚钛板(>80mm);
选型策略:
航空优先:锻件(结构件)>钛板(蒙皮)>钛棒(次承力件);
船舶优先:钛板(耐压壳)>钛棒(管路)>锻件(推进系统)。
相关链接